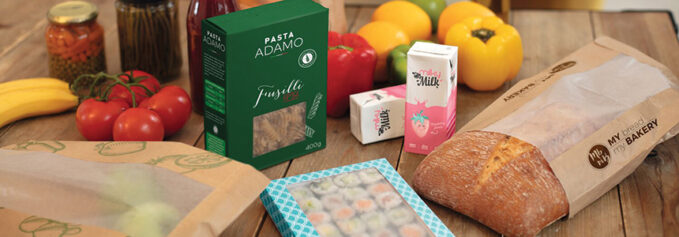
by Cassandra Balentine
Specially formulated coatings and papers present a physical barrier between a product and packaging to protect against moisture and grease. These are increasingly developed to be more sustainable without compromising safety.
Papers Versus Coatings
There are a few differences between barrier coatings and barrier papers for flexible packaging.
Above: Ahlstrom’s Cristal Transparent packaging providers natural barrier properties while also creating a view to the product it protects.
“The main difference is that barrier paper typically refers to papers formulated with barrier properties against moisture and grease. This is usually done at the paper mill level during the paper manufacturing stage,” explains Mark Hill, SVP, R&D, INX International Ink Co.
On the other hand, “barrier coatings are typically applied to a substrate after it is manufactured and provides properties like moisture, oxygen, or grease resistance to the substrate,” he adds.
Sharon Beeman, VP of Global Sales, S-One Labels & Packaging, points out that a barrier paper already has inherent barrier properties, while barrier coatings can be applied to paper, film, board, or other substrates.
A coating is one way to create a barrier paper, says Dr. Lars Hancke, manager, business development, flexible packaging, hubergroup. He explains that another option is to create a barrier with the help of a film. “Barrier coatings can, for example, also be used to create mono-material plastic packaging that can be recycled more easily.”
Barrier paper is specifically designed to provide barrier performance as part of its structure. “Barriers to grease and oil, oxygen, and liquid water can be built into the paper manufacturing process. Barrier coatings can be used in conjunction with barrier papers to further increase performance and enable additional barriers to moisture,” comments Zack Leimkuehler, VP, business development, Ahlstrom.
Target Industries
Food packaging is the primary market for barrier coatings and papers.
This is because food and other industrial packaging materials are sensitive to oxygen and moisture. “The main reason is to prolong shelf life and withstand certain storage conditions,” says Hill.
“Barrier papers with a heat seal layer target flexible packaging converters. Most foods need a barrier to keep the contents fresh within the package. The barrier offers extended shelf life,” notes Beeman.
Barrier papers are gaining importance in packaging due to a trend from film to more sustainable paper packaging, shares Hancke.
Leimkuehler points out that there are many different industries where a barrier technology is desired. “These can be barriers to regulated materials like formaldehyde or mineral oil, where the paper is key in protecting the material from transferring into or out of the structure. One of the primary targets is in the flexible packaging space where paper can offer better sustainability than historically used fossil-based films or where compostability or recyclability is desired.”
Barrier papers and/or coatings are prevalent in many printed applications as they serve as the primary brand communication in packaging materials, including digital print spaces.
Leimkuehler adds that barrier papers can be used in a variety of printed applications, and the entire supply chain is important in the development of these applications. “Packaging converters play a critical role in converting the final packaging material from barrier papers.”
Barrier Papers/Coatings
Barrier papers are a core component in many flexible packaging applications today, and are growing in market share due to the preference for a more sustainable solution as opposed to fossil-based films and plastics.
“Some common examples of how barrier papers are used in flexible packaging include non-perishable food packaging, perishable food packaging including refrigerated/frozen foods, and packaging that requires longer shelf life such as microwave packaging,” shares Leimkuehler.
The primary component of all barrier papers is cellulose. Leimkuehler explains that cellulose is a natural polymer, which is an ideal raw material from a sustainable standpoint. It is readily recyclable and compostable, and there are already high recycling rates for cellulose-based papers.
Other raw materials include a variety of additives that contribute to the technical performance of the material, and help papermakers tailor solutions specifically for their end use and end of life.
Beeman says they can be made from high-quality Kraft paper on the exterior with a heat-sealable layer on the inside.
Recyclability is increasingly in demand. While paper has a high rate of recycling, Beeman admits that it depends on how much and what type of barrier was applied to the paper. From there it is determined if it can be recycled in the paper-only bin or as mixed recycling.
S-One Labels & Packaging offers a solution in EMEA and is working on one for the U.S. “In February, S-One Labels & Packaging released FlexPaper Barrier Paper. This solution is the first paper-based coated structure in the S-OneLP EMEA line specifically designed for HP Indigo Digital Presses. FlexPaper Barrier Paper meets the demand from converters who want a paper-based pouch web that will help them to save money, increase profits, print faster, and have the ability to place low minimum order quantities,” shares Beeman.
She adds that FlexPaper Barrier Paper is manufactured as a multilayer of paper and plastic. The line achieves best results with HP Indigo but also works well with a range of flexographic press solutions.
Additional benefits of FlexPaper include a FSC-certified paper component, puncture resistance and heat sealability, high opacity, a polyethylene (PE)/EVOH COEX sealant layer designed to prevent leaking and keep contents fresh, oxygen barrier property tp extend shelf life of packaged goods, and a white paper layer that eliminates the need for white ink to help lower ink costs and provide faster print speeds.
Barrier coatings are also designed to create more sustainable flexible packaging solutions.
Beeman explains that barrier coatings are typically applied on top of the paper to add the barrier. They are applied by using typical paper machine coaters, off-machine coaters, and printing presses.
In terms of recyclability, they are generally compatible with recycling processes. “They use water as a carrier so they can be made to be recyclable, making them ideal for use in sustainable packaging solutions,” notes Beeman.
hubergroup Print Solutions offers an oxygen barrier coating—the HYDRO-LAC GA Oxygen Barrier Coating, which enables mono-polyethylene or mono-polypropylene packaging for oxygen-sensitive foods such as nuts or fresh pasta as it protects the contents from oxygen.
Moreover, hubergroup’s HYDRO-X Water Barrier Coating and ACRYLAC MGA 9003 coatings make the paper water and grease resistant. Thereby eliminating the need for a PE film lamination as water or grease barrier. Paper packaging with the barrier coating can be recycled in the already well-established paper recycling system and is, thus, an environmentally friendly packaging solution.
“These barrier coatings were developed for the packaging of moisture-sensitive food such as sugar or dry pet food and for applications from the non-food sector such as cement packaging. Moreover, they are applicable for packaging greasy foods,” notes Hancke.
Hubergroup’s coatings are water-based and contain synthetic, organic binders.
As sustainability initiatives roll out across the globe, brands and converters seek out paradigm-shifting technologies that facilitate improved end-of-life solutions for flexible packaging structures—including both fiber- and film-based substrates.
Michelman, in conjunction with partners BOBST and UPM, developed new coating technologies in total packaging solutions designed to match the high barrier performance of today’s multi-material laminations.
The next generation of multifunctional oxygen primers that Michelman created are designed to provide enhanced barrier properties at low coat weight while simultaneously enabling metallization of core substrates. This innovation, which is developed in collaboration with BOBST and other partners, results in two sustainable packaging solutions, oneBARRIER PrimeCycle, a full PE mono-material barrier alternative to non-recyclable metallized film; and oneBARRIER FibreCycle, is a paper-based packaging solution designed to replace high barrier film packaging, according to a recent Michelman press release.
Flexible Packaging Banner
Both barrier coatings and papers are essential to flexible packaging applications today. With growing demand for sustainable solutions, these options continue to evolve.
May2023, DPS Magazine