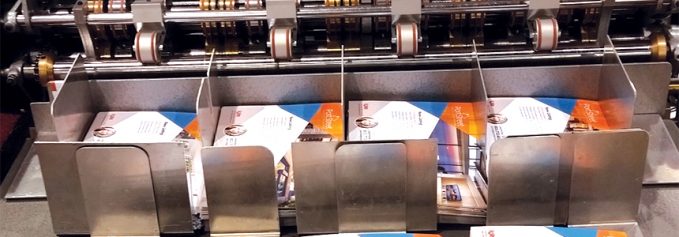
By Cassandra Balentine
Each print operation has its own unique set of needs. A versatile cutting device is a key piece of machinery for all. Attractive features for cutters include speed, accuracy, and ease of operation. Basic cutting needs range from a single straight cut to slitting, scoring, perforating, and trimming.
Above: New features of the Rollem Jetstream include AutoScan for perfect cut registration accuracy and the AutoCollation function for gathering finished cards into sets.
Digital Cutting Needs
In digital print environments, versatility is critical and automation helps streamline production.
“Print providers need products that allow them to compete in today’s short-run digital space,” says Bob Flinn, director, business development, Standard Finishing Systems.
Digital printers are looking for cutters that will turn their prints into higher margin products, agrees Dan Charwath, product manager, paper handling, GBC, an ACCO Brands Company. “In doing so, they need specific features that will allow for minimal waste and clean cuts.”
Angelo Chapa, postpress product manager, Heidelberg points out that in today’s digital print environments, customers want a cutter that integrates workflow with components linked up right through to finishing. “Customers are looking for a cutter that is software compatible to take files from either a print engine or prepress department and create cutting programs that are sent directly to the cutter ready to be processed. Once the program is in memory, it can be recalled within seconds, either by searching by name or simply suing a barcode reader to make it that much more efficient for repeat work,” he explains.
Cutting and finishing solutions have adapted to digital and inkjet press outputs. As digital press speeds continue to increase and digital sheet size grows, finishing devices are designed to keep up. “Generally, products would be imposed in multiple ups on the sheet so the ability to handle that sheet size and perform not just cutting but bi-directional bleed slitting, scoring, and perforating on over 30-inch wide cutters delivers cost savings and finished products in one step,” shares Susan Corwin, marketing manager, Rollem International.
Digital print environments foster shorter run lengths and a higher number of jobs processed per shift. “This means there is an increase in the variety of cutting plans. This creates a bottleneck when it comes to post-sheet processing due to the amount of program setup required on traditional cutters. Digital print providers need more versatile cutting solutions with quick set up and job memory storage to keep up with the number of jobs processed per shift. In addition, there is a shift towards smaller cutting systems that fit better into the digital print environment, are less intimidating to new operators, and capable of handling the smaller parent sheet sizes common to digital print,” shares Flinn.
In the fast-paced, quick turnaround digital environment, efficiency and automation are the two elements that most affect a shop’s workflow, believes Max Allen, dealer manager, Canada & U.S. Midwest, Graphic Whizard. “It’s all about taking a 12×18- or 13×19-inch sheet size and getting it down to finished size with as little cost as possible,” he shares.
“The digital world requires the processing of jobs at unheard of speeds,” says Larry Hollingsworth, sales manager, Perfecta USA Eastern Region. “The machines must keep up with the faster work pace,” he offers.
Sean Solomon, regional sales manager/VP of dealer sales, Colter & Peterson, says digital print environments typically look for an easy to use and reliable paper cutter that has a small footprint, but is heavy duty to the point where it will last for many years with the proper maintenance.
Allen points out that skilled labor is a scarce commodity and growing digital print shops must ensure they have operators to fill the gaps left by retiring workers. “One way to fill in the gap is to increase the ease of use of equipment to open up the prospective labor pool to younger and less expensive employees. By investing in more automation and less labor intensive equipment, digital print shops continue to grow exponentially without adding additional cost that ultimately increases margin.”
Guillotine and Multi-Function Cutters
Two popular cutters found in digital printing environments include guillotine and multi-function. Guillotine cutters are used for high-volume products to cut thick stacks of paper. With guillotine cutters, stacks of paper are clamped and a blade is brought down to create a straight cut. These can be manual or automated.
In a digital environment, a guillotine paper cutter is a must to convert printed sheets into a printed product. When cutting simple jobs, butting on a guillotine cutter is the fastest and most efficient way to operate. “There are minimal stock limitations in terms of size and paper weight so it is a versatile and necessary tool as every digital printer doing predictable and repetitive tasks requiring an operator drive the cost of producing these jobs up. By automating these jobs, digital print environments can eliminate over 90 percent of the labor cost in some cases, and utilize operators that are not skilled laborers,” shares Allen.
Joe Bondonna, product manager, Spiral Binding, points out that depending on the shop and its volumes, a cutter can be manual, electric, or hydraulic powered. Additionally, cutter sizes vary based on the sheet size it needs to support.
Although cutting equipment has not changed much, the introduction of software both at the cutter and in prepress to set up cutting jobs to make cutting operations simpler is a trend. “This allows for cutting equipment to be run by staff with less training required,” explains Bondonna.
Multi-function or multi-purpose cutters are also available, used by print providers to perform a variety of functions, like trimming, perforating, slitting, scoring, and even creasing and folding.
“Multi-use cutters are great for routine projects like business cards. They are efficient in both time and training since you only need to use and be trained on one machine,” shares Charwath. However, they tend to be expensive and standalone devices generally offer a stronger cut.
Multi-use cutters provide the finishing required to complete a job in one operation, says Dean Askin, regional manager, EMT International. Additionally, they enable a shorter footprint for companies with limited floor space.
Depending on the specific shop and its requirements, different cutting methods provide varying benefits. Flinn points out that in many cases, both guillotine and multi-function slitter/cutter/creasing solutions may sit side by side. “For shops that want to run a lot of short-run applications—from photobooks to direct mail pieces and business cards—that also require additional processing such as creasing and perforation, a multi-use cutter offers more benefits while reducing footprint, processing steps, and operating costs. For shops or jobs with longer production runs that only require cutting, a single-purpose tool may be a better fit.”
Corwin agrees, pointing out that multi-function cutters enable the ability to perform multiple processes in one pass, which offers substantial benefits including reduced labor costs by utilizing just one operator for various processes, increased turnaround time, and greater job control to reduce bindery bottlenecks.
Key Features
A cutter should handle existing applications as well as support growth into new markets. Important considerations include configuration, footprint, the vendor and its training and support reputation, ease of use, and return on investment (ROI).
When looking into a new cutter, Flinn suggests asking yourself key questions, like whether or not you plan to use barcodes to track and setup for jobs in the bindery, or if JDF will be implemented through the operation for setup, tracking, and reporting. “One specific solution may be a good fit now, but if the shop plans to expand the variety and number of jobs it takes on in the near future, providers run the risk of buying a piece of equipment that will be overwhelmed or obsolete in a few years.”
Allen points out that any decision about investing in new finishing solutions should start from the inside out. “Printers need to evaluate bottlenecks and establish the cost of using current equipment. A good way to do this is to start tracking the amount of time spent on current finishing equipment and the cost of errors and labor.”
Consider the ROI on equipment to determine if the capital expense is justified. “Although the equipment needs to fit into a budget for current applications, can the equipment add value to the shop with new jobs being added, allowing for an increase in revenue stream?” asks Bondonna.
Corwin says the run lengths and the amount of job changeovers would be key considerations regarding the best type of cutting solution. “Many presses require UV coating after printing so the cutter must be capable of precise cuts as is the case with toner-based ink.”
The type of digital imaging and embellishments are also important. “Raised UV and textured UV patterns can be difficult to cut. If the device applies heavy pressure, the specialty finish can disintegrate so this should be addressed,” says Corwin.
Choosing a vendor is an important factor, including the support after implementation. “No matter what product you buy, you should always consider how and where your technical support, service, and parts are coming from. We have heard many horror stories from small format and digital printers who buy the least expensive machine only to learn that the machine doesn’t work when it is delivered and there is no support with parts or service available in their area or even in the U.S.,” warns Solomon.
It is critical for print providers to do their research when adding and replacing machines. “The wrong decision can greatly influence whether they are successful in today’s market. Too often they are taken in by price and purchase a machine that will not do the job they bought it for. Thus, they are slower or the job can’t be completed on that machine. Quality is rarely cheap,” stresses Hollingsworth.
On the Market
Several manufacturers and distributors feature cutting solutions ideal for digital printing environments.
Colter & Peterson provides the PRISM P80 and P92 paper cutters, which feature a compact design. Additionally, Colter & Peterson’s Microcut PLUS 12-inch color touchscreen computers come standard to these models.
Duplo USA offers guillotine cutters and slitters/cutters/creasers. The 800 PRO Hydraulic Cutter its widest guillotine cutter, featuring a maximum cutting width of 31.4 inches and a maximum stack height of four inches. The DC-746 Slitter/Cutter/Creaser is an all-in-one digital color finisher featuring a standard PC controller software and CCD scanner. It features an optional rotary tool and cross perforating modules.
EMT International offers the RFX Dual Head Cutter and Stacker, which features straight cut or chip cut sheeting, full-bleed capability, and slit/merge functions. It also offers the Chameleon Bundled Solution, which is a multi-use finishing solution.
GBC’s ProCut 17P is an automatic cutter with a maximum width of 17 inches. It features a LED light for precise cutting and multiple safety features. It is equipped with full programmability of up to 80 programs and 99 steps.
Graphic Whizard offers a line of electric and hydraulic paper cutters featuring programmable back gauges and color touch screen programming. The company also offers a line of automated multi-function machines in its slitter/cutter/creaser lineup. A popular machine in the series is the PT 335SCC Multi.
Heidelberg offers the Polar D Model hydraulic-driven cutters. For digital print environments, the Polar D 56, D 66, D80, and the D115 are available. Additionally, Polar N 78 and Polar N 92 models are gear-driven machines well suited for digital customers running three shift operations. These Polar cutter models support all digital environments with integration and networking for Compucut software.
MBM’s Triumph line includes the 7260, a 28-inch programmable cutter featuring a hydraulic clamp, power back gauge, seven-inch touch pad control module, and infrared safety light beams. It supports VRCut by Lytrod Software.
Additionally, MBM offers its Aerocut systems, which are all-in-one finishing devices compatible with the company’s Intellicut software.
Perfecta USA offers the Perfecta 80 TS, a gear-driven, high-speed cutter for digital or conventional workflows. Featuring touch screen operation and a heavy-duty design, the solution performs simple or complex cutting jobs of paper, board, plastic, or other sheeted materials.
Rollem’s Jetstream finishing solutions are designed for slitting digitally printed products. Sheets are edge trimmed, slit, scored, perforated, and cut in one, fully automatic system. Rollem also offers its Advantage slit/score/perforation model for lower to mid-volume print runs.
Spiral offers a more traditional, guillotine cutter is the Triumph VR-CUT and the AeroCut line of automated cutter, slitter, and creaser systems.
Standard Finishing Systems offers the Standard Horizon SmartSlitter—SMSL-100, the Standard Horizon SmartStacker, and the APC-610 Digital Paper Cutter to digital print environments. The SmartSlitter performs a variety of functions including bleed trimming, cross cutting, perforation, and slitting as standard or optional features, as well as skip perforation, kiss-slitting, partial perforation, and digital output-friendly creasing in both direction of feed and across the entire sheet. The SmartStacker converts B2 size sheets into up to 28 individual cut sheets with intelligent accumulation, stacking, and end-to-end JDF control. The APC-610 Automated Programmable Paper Cutter features a maximum cutting width of 24 inches and a cutting height of 3.9 inches.
Therm-O-Type provides its Zip line of multi-function digital finishing systems. The portfolio includes the Zip-TS2L Digital Finisher, which features cutter/slitter/creaser functions.
Cutting Potential
A versatile multi-function cutter allows digital print providers to handle a variety of applications. A sturdy guillotine cutter is a sound investment. Automation in either of these machines streamlines operations. Ease of use is especially important as industry changes mean less skilled operators are tasked with more frequent and complex finishing. dps
Sep2019, DPS Magazine