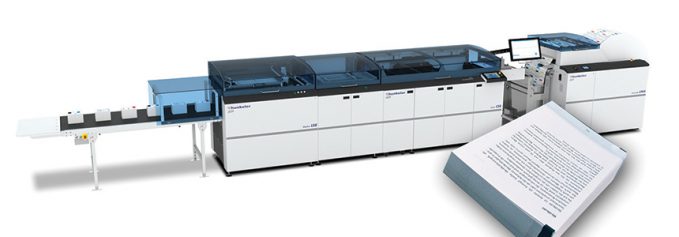
By Melissa Donovan
Post-press solutions are integral to the digital printing process. Varying configurations, including unwinders/rewinders, gluers/folders, inserters, binders, trimmers, and slitters are routinely required on the production floor—whether placed inline, near line, or offline. Trends in inkjet from personalization to achieving higher volumes are major influences on the newest generation of post-print equipment.
Above: The Standard Hunkeler Gen8 Roll-to-Stack system comes with the LS8-30 Long Stacker, which supports 4×5.5-inch postcards to 22.5×30-inch sheets at speeds of up to 300 stacks per hour.
Influencing Post Press
With a focus on post-press offerings for continuous and cutsheet configurations used in document processing, it’s apparent this equipment continues to advance in response to the need for increased productivity and efficiency across the print shop floor.
According to Don Dubuque, director of marketing, Standard Finishing, new post-press offerings are designed to accommodate the need for shorter runs and unique processing requirements. This means more automation, faster speeds, the ability to handle a wider range of paper weights and formats, and perform multiple finishing processes in a single line.
For continuous or roll-fed printers, solutions that offer multiple features are attractive. There are options available that can be configured to deliver straight or offset stacks, fully separated book blocks, or saddle-stitched books in one system, completed with dynamic perforating and integrated inspection to provide ultimate application flexibility, explains Dubuque.
“From a continuous configuration perspective, more customers are asking for a system that completely finishes a product in one line with reduced labor and increased speed. The focus is on eliminating additional steps that increase time and labor to complete a job yielding lower cost and higher margin,” adds Nick Gerovac, director of sales, VITS International.
For cutsheet print environments, Dubuque says multifunction systems with the ability to slit, gutter cut, edge trim, perforate, and crease all in one pass are attractive because one device handles what would have once taken multiple machines.
Reduction in labor requirements is an important topic that influences post-press solution trends in cutsheet. For example, if only one finishing device is installed near line to multiple cutsheet devices, only one person is required to operate that device, notes Andy Fetherman, VP of sales and technology, Muller Martini Corp.
“This equates to fewer people and labor hours to produce finished products. “This type of highly productive system is critical for the future of post-press processing, since the quality of cutsheet print is very high and demands a higher finishing quality,” continues Fetherman.
Increased media options influences post-print equipment used for both continuous and cutsheet configurations. “New finishing products must also accommodate the applications enabled by the increasing print quality available from the latest inkjet presses. Glossy coated papers required for many graphic arts and direct mail applications pose challenges to press and finishing manufacturers alike,” comments Scott Peterson, product marketing manager, Tecnau.
On a Line
Post-press solutions can be configured to run offline, near line, or inline with digital printing devices. There are advantages and disadvantages to every setup. Preferences vary depending on the print provider and its target market.
Offline finishing offers flexibility, allowing print providers to process a wider range of applications. “Another benefit to offline is the ability to optimize process speed to the media—light or heavy weight stocks might run through finishing with fewer hiccups at slower speeds, but run just fine under tension roll to roll on press,” explains Dubuque.
For digital book production, Fetherman believes near line is the new normal. “Although machines are disconnected physically, barcodes and other data are utilized to setup downstream processes like automatic machine makeready and validation of finished product content.”
Gerovac notes some disadvantages to the offline and near line processes.
“Users may need to go back to the press for damaged, lost pieces—adding an extra step to the process. Other drawbacks include storage for work in progress inventory, possibly more labor cost, additional scheduling, and perhaps more floor space.”
Print and finishing in one continuous process make inline options attractive. “Inline finishing solutions are better suited for a few dominant applications that are run the majority of the time. It requires less floor space and often saves on labor costs by reducing manual touch points,” notes Dubuque.
There are also combo-configurations. Fetherman provides an example using both near line and inline in the production of digitally manufactured perfect bound books. “In the first stage of production, one paper handling part is eliminated by producing inline in a roll-to-book block configuration. The preprinted rolls are processed directly into an inline folding and collating device. The second production stage consists of a near-line installation of a perfect binding line.”
When it comes to setup popularity—offline, near line, or inline, Gerovac says in his experience 60 percent of digital customers request offline or near line and 40 percent choose inline. “It really comes down to the individual requirements of the customer and to some degree their comfort level with a given approach.”
“There is no one-size-fits-all answer—each organization has to determine what makes the most sense for them, with the help of the finishing vendor,” agrees Peterson.
Maintaining Integrity
Digital printing’s ability to harness variable data and accurately personalize or customize documents in cost-effective, short runs is what makes it attractive to print buyers. Post-press offerings that run in tandem must be able to handle variability accurately and reliably.
For Fetherman, the introduction of personalization and its continued growth creates the need for file to finished product workflows versus file to print workflows. “File to print workflows do a good job getting print on paper, but they don’t manage the critical finishing processes after printing,” he explains.
“Personalization drives the need for integrity,” stresses Dubuque. Something always top of mind in transactional printing—HIPAA and other compliance standards require audit trails and other safeguards—the same can now be said for marketing. “Brands that are spending money for data-driven campaigns want assurance that the correct information was sent to the right recipient.”
Finishing vendors address the need for integrity with inspection systems integrated into their solutions that track and inspect products. “Systems can complete audit trails of package assembly for the production of documents with variable information—whether sensitive or non-sensitive. They can also check for book completeness, page sequence, missing or duplicate pages, and cover matching,” explains Dubuque.
“End-to-end workflows allow for book-of-one validation throughout the entire production process to ensure that highly personalized books are produced with every page of every book properly finished,” adds Fetherman.
Reaching Higher Volumes
Inkjet printing is making strides in the high-volume market. Similar to personalization, post-press offerings must address this trend. In most cases this means the finishing device should be equipped to match or exceed these volumes on the backend of the process.
Physically, post-press equipment needs to be robust enough to function at longer runs and higher speeds, comments Gerovac. “Having finishing equipment that is reliable and does not need a lot of maintenance is critical to being able to be more efficient on longer runs.”
Print providers have their own set of requirements when it comes to high volume. “As inkjet climbs into the high-volume space, customers have greater need for industrial solutions that can handle multi-shift volumes. At the same time, commercial shops need the flexibility to handle various jobs and media. This poses a real finishing challenge,” notes Dubuque.
In response, more industrial-focused, modular systems are being launched like Standard Hunkeler’s Generation 8 (Gen8) modules for continuous feed printing. Each system handles coated and uncoated stock from 27 lb. text to 110 lb. cover. The Hunkeler Gen8 Roll-to-Roll solution handles web widths of up 22.5 inches, roll weight up to 1,980 lbs., and speeds of up to 830 feet per minute (fpm)—with the option to add slitting and edge trimming. The Hunkeler Gen8 Roll-to-Stack system comes with the LS8-30 Long Stacker, which supports 4×5.5-inch postcards to 22.5×30-inch sheets at speeds of up to 300 stacks per hour.
“Higher volumes create a need for more productive finishing solutions. When a printer has the capability to produce up to 1.5 billion pages a year with a single high-speed inkjet device, not only must they be able to seamlessly handle all the workflow challenges through to the finished product, but they also need to handle the high finishing volumes with a single device whenever possible in order to achieve optimum efficiencies,” explains Fetherman.
He believes all near line and inline workflows have been altered because of these higher speeds and volumes. For example, Muller Martini’s inline SigmaLine Book Manufacturing System, which enables inline book block production for perfect bound and hardcover books, runs at up to 1,000 fpm.
For every increased increment of speed, each minute of press time takes on higher value. Post-press solutions need to take this into account by helping decrease downtime. “Splicing unwinders and rewinders are now available to virtually eliminate downtime for roll changes—for heavier papers, which equate to shorter roll lengths. A productivity gain of over 40 percent is possible through the addition of a splicing unwinder,” states Peterson.
Tecnau’s Roll 40 consists of the Zero Speed Splicing Unwinder u40 and Splicing Rewinder r40. Dual unwinder and rewinder modules are set at floor level. The Roll 40 permits mixing of paper quality, paper grade, and web width between rolls.
The Finishing of Today
To address the ever-changing needs of the print provider—namely speed, reduced manual labor, and higher volumes—the next generation of post-processing solutions are modular, scalable, and/or multifunctional. This equipment is run near line, offline, or inline, depending on what the best scenario is for the print provider.
Whether the application is transactional, marketing, or a book—inspection systems are important players in the post-process, especially as personalization requests heighten. Finishing equipment must also maintain some level of integrity. This is done by tracking and inspecting finished documents to ensure a document or mailing isn’t delivered to the incorrect recipient. dps
Oct2020, DPS Magazine