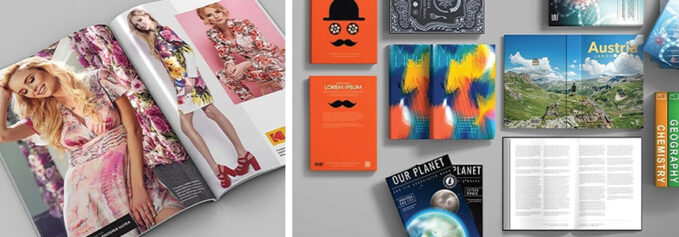
By Cassandra Balentine
There are many ways to classify production inkjet. For instance, you could go by configuration, cutsheet or sheet—versus web-fed; or by technology—continuous or drop on demand inkjet; or ink type—UV- or aqueous-based formulations.
Aqueous inks for high-speed production inkjet devices come in both dye- and pigment-based options.
Dye-based aqueous inks are water soluble and offer high saturation because the ink is absorbed into the fibers of the paper of porous and semi-porous substrates like uncoated paper. “This provides a higher color gamut,” points out Lucy Perez-Sierra, advisor, category marketing, Canon Solutions America.
However, she points out that dye-based aqueous inks have less durability, which means the ink will fade more easily if the printed application is exposed to sunlight.
In addition to light fastness, applications printed with dye inks are not water resistant.
Perez-Sierra says dye-based inks were the de facto standard in high-speed production inkjet initially, however the durability limitations of water and light fastness outweighed the advantages. “Dye inks were less expensive, but over time as pigment inks were introduced into the market and leveraged economies of scale the cost differential between the two types of inks became negligible.”
“Dye-based aqueous inks have a long history in the transaction print market. They are less durable and permanent than pigment-based inks yet more affordable, making them ideal for short shelf life, lower coverage monochrome text versus high-color graphic applications,” notes Jennifer Pennington, director, product management/OEM partnerships, Kodak.
Saba Lotfizadeh and Vladimir Jakubek, research and development chemists, HP Inc., share that dye-based aqueous inks are typically known for their vivid colors, but stress that this benefit is highly paper type and time dependent. “There are other benefits of dye-based inks including excellent system reliability and high scratch and rub resistance, due to high dye penetration into the paper substrate.”
They agree that dye-based aqueous inks have limitations in terms of print longevity, which shows up as limited lightfastness, humid fastness, and water fastness. “In addition, dye-based aqueous inks can have the appearance of low color saturation and gamut volume as a result of dye penetration into the paper substrate.”
On the other hand, pigment-based aqueous inks generally produce a larger color gamut than dye-based inks. “Kodak’s proprietary micro-milled pigment particles reduce light scattering, enabling higher optical densities and color purity, as well as a color gamut that is 35 percent larger than the gamut achievable by offset printing,” shares Pennington.
Pigment inks can also be more durable, generating better results for certain applications, such as packaging and labels. “Pigment-based inks are typically more light resistant, increasing the shelf life of the printed product. With Kodak’s proprietary milling process and skilled in-house material science team, the company offers customized formulations to deliver ideal color match and uphold brand integrity.”
Pigment-based aqueous inks are not soluble and consist of fine solid particles suspended in a carrier liquid, like water. Conversely, they have higher durability and color stability compared to dye-based aqueous inks, and are more resistant to fade when exposed to sunlight, therefore lasting longer. “Pigment inks are more smudge and water resistent,” offers Perez-Sierra. She adds that pigment black inks produce a truer solid black than dye ink.
Lotfizadeh and Jakubek agree, adding that pigment-based aqueous inks offer high print longevity in terms of lightfastness, water fastness, and humid fastness, while also demonstrating high-color saturation, gamut volume, and ink efficiency.
“The limitations of pigment-based inks can include lower ink shelf life due ink stability and pigment settling and less scratch and rub resistance on coated media,” they note.
In general, water-based inks have minimal impact to the environment, have little to no odor, and are safe for human health in production environments, which makes them ideal for high-volume print applications, comment Lotfizadeh and Jakubek.
The emphasis on environmental impact is increasingly important. “Water-based ink systems have reduced environmental impact as compared to other technology alternatives,” state Lotfizadeh and Jakubek. “They are typically more than 80 percent water in contrast to UV- and oil-based flexographic systems, which contain no water.
Also, water-based inks don’t have the same health and safety challenges as UV systems do with regards to their monomer content.”
Application Considerations
The use of aqueous/water-based inks in production inkjet systems are popular for a range of applications, including general commercial print, direct mail, publishing, and transactional applications, as well as corrugate and folding carton packaging applications.
One primary considerations for identifying which application segments water/aqueous-based inks in production inkjet systems target is substrates specific.
“The evolution of water/aqueous-based inks working in conjunction with primers or the formulation of inks has enabled production inkjet systems the ability to run on offset coated substrates in particular, glossy paper. This has allowed for more offset transfer,” offers Perez-Sierra.
As such, she says market segments that are now open because of improvements with aqueous-based inks in production inkjet systems include publishing, transactional/financial, business communications, direct mail, and commercial print applications like ballots, catalogs, magalogs, magazines, brochures, marketing collateral, posters, calendars, product inserts, and more.
“Water-based inks can be designed for use in food packaging applications. However, because of the water content, these inks require sufficient drying to make prints durable. This can lead to some limitation in overall production speeds for applications with very heavy ink coverage,” share Lotfizadeh and Jakubek.
Aqueous-based inks are also suitable for printing other industrial applications like signage and graphics, wide format technical applications such as CAD, labels, and textiles, they add.
“The most appealing applications for dye-based inks are those with a relatively short shelf life, low coverage, and limited graphics or color,” says Pennington. “Printers that focus on transactional documents like bills and statements are the most frequent users of dye inks. Some high-volume, yet low coverage direct mail or publishing applications also fit that mold.”
She adds that imprinting systems for addressing or coding often use dye-based inks, but pigment-based inks may also be available.
Pigment-based inks generally produce a larger color gamut than dye inks yielding a better fit for more high ink coverage applications, such as photobooks, color books, magazines, catalogs, and some direct mail. “Pigment inks are also more durable, especially with pre- and post-coats, which are then well-suited for packaging and label applications,” explains Pennington.
Speed, Volume, and Costs
When comparing water-based inks to alternative options, it largely depends on the technology where it is utilized.
Lotfizadeh and Jakubek explain that water-based inks designed for digital inkjet enable transfer of work from analog to digital through “print of one” customization and personalization and fast turnaround times. This is possible with the elimination of analog makeready processes that take time and create considerable waste.
“Many analog-based ink systems including solvent, oil, and UV inks encounter regulatory challenges and worker safety issues, which make them difficult to use across the global print production environment,” explain Lotfizadeh and Jakubek.
When compared to UV, they point out that UV curing can also be energy intensive to fully cure inks, whereas water-based inks can have some limitations with respect to durability as compared to UV-curable inks, “but performance is often very acceptable for the targeted applications.”
“The biggest difference in pigment-based aqueous inks is evident in the technology in which the inks are used. When used in Kodak continuous inkjet systems, such as the PROSPER Presses, there are no limitations. The inks deliver offset-quality print results at production speeds of up to 410 meters per minute or 1,345 feet per minute.
Kodak’s proprietary inks increase sustainability through productivity and water-based chemistries thereby reducing the carbon footprint. In contrast, drop-on-demand inkjet technology requires greater amounts of humectants to keep the printheads from drying out thus reducing the life of the printhead,” offers Pennington.
When looking at cost, it is more than the price of the ink. Pennington stresses the importance of considering the total cost of production. “Total production costs will vary between inkjet devices and analog technologies. When comparing analog technology to inkjet, one must consider plate costs, processing, makeready on the press, and paper waste, where Kodak inkjet offers less makeready time, higher productivity, and reduced waste. Inkjet is typically less expensive for shorter run lengths and variable print jobs.”
Lotfizadeh and Jakubek feel that water-based inks provide a competitive total cost per page and total cost of ownership.
Substrate Compatibility
With the focus on paper supply chains, media flexibility is an important consideration for print providers.
Pennington says a large variety of substrates are compatible with water-based inks and in most cases, primers are used to achieve the best results. “Kodak has optimized its pre-coat and ink formulations to print at the highest speeds on substrates ranging from newsprint to films and plastics. The company continues to invest in material and chemical sciences to advance pigment-based inks. Optional post-coating may be required for extra durability, specifically in the packaging market.”
HP’s PageWide presses such as the Advantage 2200 and the T250 HD use digitally applied HP Optimizer to maximize the system performance and boost print quality, gamut volume, and media breadth. “HP Optimizer is jetted alongside other colors and is typically required for printing directly onto both offset uncoated and coated media.
This expands the media versatility and compatibility. However, no HP Optimizer is required for inkjet treated media or HP ColorPRO paper technology,” say Lotfizadeh and Jakubek.
Settling on Ink Sets
When it comes to ink sets in high-speed inkjet printing, dye- and pigment-based inks are water-based solutions. Manufacturers continue to develop their ink sets for increased vibrancy, media compatibility, and dry time.
Water/aqueous-based inks are utlized for many applications. However, these tried and true inks tend to thrive in areas like transactional, books, direct mail, and general commercial printing with specific advantages and limitations when it comes to dye- versus pigment-based solutions. dps
Jul2023, DPS Magazine