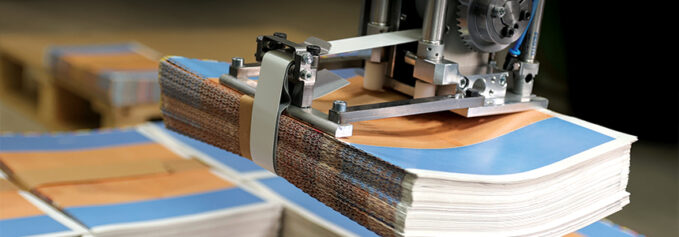
by Cassandra Balentine
Automation is increasingly essential to print providers. This is especially true for digital or hybrid print environments looking to reduce human errors and touchpoints in order to remain profitable on high volumes of complex, short-run jobs. Automation happens everywhere from order entry to machine-level automation, material handling, and everything in between.
Above: Palamides’ Automated Delivery solutions are designed to seamlessly integrate with digital printing presses and postpress equipment, allowing for efficient handling of printed materials and reducing the need for manual intervention. See page 22.
While the benefits of automation are obvious from job to job when running longer offset prints, it is even more dramatic when processing digitally printed products in run lengths as low as book-of-one. “Automated digital workflows in the bindery enable efficient planning and tracking of all jobs as they move through the shop with access to real-time and historical data to monitor and improve efficiency as well as error alerts and maintenance notifications to maximize the up-time of equipment,” shares Bob Flinn, director of business development, Standard Finishing Systems.
Aiming for Automation
Binderies adopt automation for many reasons. For those that handle digital or a hybrid of digital and offset work, the push for automation addresses the need to streamline production processes, reduce manual labor, and increase efficiency. “In digital/hybrid print environments where shorter print runs and variable data printing are common, automation helps manage the diverse range of print jobs more effectively. It allows for seamless integration of finishing processes with the printing workflow, ensuring faster turnaround times and consistent quality,” shares Stefano Palamides, managing director, palamides GmbH.
The personalization of printed products for greater effectiveness and the need for equipment solutions that have a higher level of productivity to counter the labor shortages in the graphic arts also drive demand for automation, says Andy Fetherman, president/CEO, Muller Martini Corp.
Changing industry conditions are the primary impetus for automation. “Today’s digital, web to print (W2P), variable data, and highly personalized applications require a higher level of tracking from prepress through shipping as well as a high number of machine setups per shift. Additionally, skilled operators are aging out of the industry and there is a shortage of new operators willing or able to train on non-automated, legacy equipment. With automated binding equipment, setup is completed in many cases with the press of a button.
This lowers the barrier of entry for new operators while allowing for more machine setups per shift, resulting in more jobs processed per day,” offers Flinn.
Automation in binding within digital/hybrid print environments responds to the need to enhance operational efficiency, reduce costs, and meet the increasing demand for personalized and short-run print jobs. “In these settings, where the volume and variety of print jobs can fluctuate significantly, automation allows for quicker setup times, minimal manual intervention, and more consistent quality,” comments Dmitry Sevostyanov, CEO, Customer’s Canvas.
Further, as customer expectations for shorter turnaround times and customization options continue to grow, automation within binding processes ensures that print service providers (PSPs) can remain competitive and responsive to market needs. “This shift not only streamlines production but also enables a more agile production environment capable of adapting to the rapid changes in print demand and specifications,” adds Sevostyanov.
Stefano Formentini, VP, sales and marketing, Meccanotecnica; and Manrico Caglioni, president, Book Automation, Inc. – part of the Meccanotecnica Group, feel that in today’s fragmented world, entertainment platforms and tools continuously introduce fresh ways for content distribution. “Consequently, we observe a dual effect—a noticeable decline in book volume per title juxtaposed with a surge in the number of new titles published annually. This phenomenon, coupled with advancements in printing technology such as the development of digital presses, is fostering the emergence of innovative business models tailored to efficiently manage book production, particularly in short and ultra-short print runs.”
They feel the evolution of new business models necessitates a paradigm shift in book manufacturing practices. “Enhanced workflow management and heightened automation are imperative to effectively handle the numerous, different jobs that printers and binders produce on a daily basis. With this in mind, streamlined processes and increased automation are essential for optimizing efficiency and meeting evolving market demands,” comment Formentini and Caglioni.
Aarona Tesch, product marketing manager, ACCO Brands/GBC, admits that bindery has typically been a bottleneck in production print, especially as digital and offset presses increase in throughput capacity. “By implementing these automation technologies, PSPs can improve efficiency, reduce labor costs, minimize errors, and enhance the overall quality of printed materials in digital print or hybrid digital/offset print environments.”
Barriers of Automation
While automation is the holy grail, its implementation is fraught with adoption barriers, such as the initial investment cost, compatibility with existing workflows, and implementation concerns. These should continue to decline with continued advancements by finishing vendors and integration partners.
Cost is one of the biggest barriers. “Most printers today stay in touch with the changes in technology and know that automation is a must. However, not many are able to convert all of their legacy, manual binding systems to automated ones at once without staring down a significant upfront cost. As a result, automation is adopted in stages. But, it is being adopted,” stresses Flinn.
“The upfront costs associated with implementing automated systems, including purchasing new machinery and software, can be prohibitive for some businesses, particularly smaller ones,” share Formentini and Caglioni.
Integration complexities are another challenge. “Integrating automation technologies into existing workflows can be complex and time consuming,” add Formentini and Caglioni.
Automation solutions typically cannot be retrofit on existing equipment, so companies typically have to invest in these newly automated solutions. “While the return on investment is often very good, one must also look at updating their prepress workflow to drive these highly automated products,” says Fetherman.
Workflow considerations also come into play. “Transitioning to automated processes requires thorough reevaluation and optimization of existing workflows. This can be challenging, as it may disrupt established practices and necessitate significant changes to maximize efficiency,” say Formentini and Caglioni.
“Adopting automation tools for prepress tasks such as setting up product catalogs, providing automated online quoting, and facilitating digital previews and approvals presents significant challenges. Creating detailed, user-friendly product catalogs is technologically demanding, given the need to accurately represent a variety of print options. Similarly, developing automated quoting systems that can instantly calculate printing costs with accuracy involves sophisticated algorithms. Offering precise digital previews and efficient online approval processes requires advanced digital representation and customer feedback mechanisms. Overcoming these obstacles is crucial for the effective use of W2P automation, which aims to streamline operations and improve customer experience,” comments Sevostyanov.
Printers may also face resistance from employees who fear job displacement or lack the necessary skills to operate automated systems, offers Palamides.
It may be a challenge to find automation solutions that accommodate the variety of substrates and finishing requirements in digital print environments, suggests Palamides.
Al Scolari, president, APS Imaging Solutions, Inc., also sees the challenge in supporting the many different substrates printed on today, as well as the speeds. “These issues are being addressed with new equipment,” he states.
Tesch summarizes that while automation offers numerous benefits in improving efficiency and streamlining processes in bindery operations, several challenges hinder its adoption—initial investment cost, integration complexity, training and skills gap, workflow disruption, customization, and flexibility.
Evolving Role
The next major focus for bindery automation is in back-end automation solutions. “This will consist of using co-bots, automated guided vehicles, and other robotic devices to provide more efficient paper and finished product processing with minimal labor requirements,” says Fetherman.
Formentini and Caglioni feel that the significance of automation in the bindery sector is poised to grow exponentially. “It is becoming an increasingly strategic and critical factor for both printers and binders, with its proper adoption serving as a defining factor in their success. Embracing automation effectively will not only enhance operational efficiency but also play a pivotal role in shaping the competitiveness and longevity of businesses in the printing and binding industry.”
In the next five years, Palamides sees the role of automation in finishing, particularly in digital print environments, continuing to evolve and expand. “As printers increasingly perceive themselves as manufacturing companies and embrace Industry 4.0 principles, automation will become more integral to their operations. We anticipate further advancements in robotics, AI-driven technologies, and Internet of Things-enabled devices that allow for even greater automation and connectivity in finishing processes. This will lead to increased efficiency, productivity, and quality in digital print production, driving the industry forward into a new era of smart manufacturing.”
Flinn says robotics is an area where we expect the most innovation and growth, comparatively. “Already, we’ve seen many manufacturers like Horizon showcase robot prototypes on show floors to demonstrate automation in material handling. While we may not see anything like a widespread adoption of these new technologies in five years, I think we’ll see robotics operating on the production floors of more early adopters.”
In the next few years, Tesch expects automation in bindery, particularly in digital print environments, to continue to evolve and expand in several key areas including integration and connectivity, artificial intelligence (AI), enhanced personalization and customization, and on demand and short-run production. “Flexible automation systems will facilitate quick job changeovers, minimize set up times, and enable cost-effective production of small batch sizes without sacrificing quality or efficiency. Further, Smart manufacturing and Industry 4.0 will—with cloud-based applications—optimize efficiency and agility in bindery operations,” says Tesch.
From a prepress perspective, Sevostyanov says finishing automation is becoming more critical in digital print environments. “We’ll see smarter, automated systems that prepare files for printing with less manual work, using AI to fix common issues before printing begins. Online customization tools will also get better, making it easier for customers to design and visualize complex products, including binding details.”
The connection between prepress and bindery will tighten, with automated setups for binding based on the digital prepress data. “This means less guesswork and more precision in meeting customer specifications. Additionally, the approval process between clients and printers will streamline, thanks to automation handling revisions and feedback more efficiently,” says Sevostyanov.
Further, as the printing industry focuses more on sustainability, Sevostyanov feels that automation will help reduce waste and optimize the use of materials and energy. “In essence, automation will make prepress and bindery faster, more accurate, and less wasteful, truly changing how digital printing jobs are prepared and executed,” he predicts.
Greater Automation
Automation brings many specific benefits to finishing operations in digital or hybrid production environments.
Greater automation allows finishing operations increased productivity, improved quality control, and reduced errors. “Automation streamlines the production process by eliminating manual intervention, minimizing the risk of human error, and ensuring consistency in the finished products. In digital print environments, where jobs often have tight deadlines and high variability, automation helps meet customer demands more efficiently while maintaining profitability,” adds Palamides.
“Driven by shorter run lengths, skilled labor shortages, advances in machine-level automation, and more robust digital workflow systems, there is no doubt that bindery automation will continue to spread in digital, offset, and hybrid printing plants in the next five years and beyond,” concludes Flinn.
For more on the topic of finishing automation, visit dpsmagazine.com for additional web-exclusive content as well as a webinar.
May2024, DPS Magazine