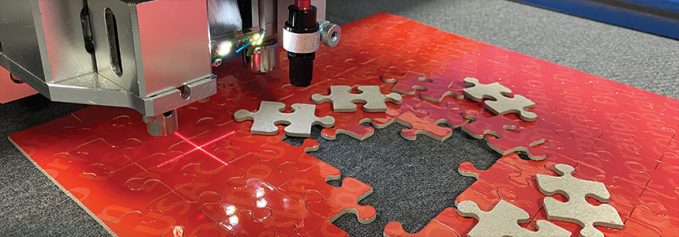
by Melissa Donovan
Digital prototyping and packaging environments differ by print provider and equipment lineups. For example, an all-digital operation not only means everything is printed digitally but also necessitates automated, digital finishing elements. A traditional folding carton or corrugated converter that may have added digital prototyping and packaging options to flexographic or offset printing might use die-cutting equipment due to a familiarity in the process.
Above: In July 2021, Duplo introduced the new DocuCutter DPC-600 digital die cutter, ideal for producing short-run packaging.
In any event, print providers look to cutters that match the productivity of other areas in their production lines, but don’t require a heavy investment in specialized labor to run. “This has led to cutting devices that are simple to operate and can handle multiple applications with minimal set-up time to be in demand,” offers Don Dubuque, director of marketing, Standard Finishing Systems. He sees a shift towards smaller cutting systems that tend to fit better into digital print environments and are less intimidating to new operators.
Both die and flatbed cutters are utilized for finishing digitally printed prototypes and packages. The ability to create intricate, unique shapes in addition to a host of other benefits makes them attractive. Each has advantages and disadvantages, which are largely based on the volume and type of work coming into the print shop.
Strengths and Weaknesses
There are strengths and weaknesses for both die and flatbed cutters. When comparing them in their use in digital prototyping and packaging environments, it’s important to address production speed, run length, material selection, costs, and design flexibility.
Die Cutting
Die cutters are ideal for large quantity, static jobs. For repeat packaging requests, the dies are economical since they can be re-used. While very productive, it does take time to source, manufacture, and ship dies to a print facility.
When it comes to die cutting, there are two different types—rotary and platen or flatbed. Comparing the two, Juan Kim, CEO, Valloy Incorporation, believes that a rotary die cutter with pinch-roller mechanisms is faster because “the driving force of moving paper forward and backward is easier than moving a whole cutting arm on a flatbed.” He points out that cutting on the table of a platen die-cut machine is more stable and accurate.
In addition to offering higher speeds, rotary die cutters provide higher tolerance and accuracy, with “the ability to perform multiple different shape cutting in the same processing cycle,” explains Kevin Chen, product manager, Duplo USA Corporation.
Platen or flatbed die cutters are particularly suited for packaging and prototyping. “They have the ability to utilize a sharp strip of metal called steel rule instead of an actual plate. This means they can process thicker material that is too thick to cut with a rotary press, especially thicknesses typically seen in the packaging and prototyping market,” continues Chen.
In the packaging industry, Simon Lewis, VP marketing, Highcon, believes there is room for both rotary and flatbed die cutters. “The savvy packaging converter knows well when to use each.”
Specifically, Caroline Bell, marketing coordinator, Elitron, believes the biggest strengths of die cutters are in the corrugated sheet segment, “as they are the most productive of all cutting systems.”
For example, Chris Van Pelt, president, Therm-O-Type Corporation, says that automatic die-cutting presses with steel rule dies can provide throughput speeds of up to 5,500 impressions per hour. This is all while producing consistent, high-quality scores while die cutting.
“Traditional die cutting is great for offering a fixed design for the production of multiple product. Once the die is made many pieces can be cut quickly. After the initial cost, this die can then be used continuously for multiple projects. Production-wise, a traditional die can cut more pieces quicker than a digital system, which only cuts one sheet at a time,” notes Terri Winstanley, product and marketing manager, Intec.
It’s also important to address tasks beyond cutting; as die cutters offer additional value-adds or upsells to a printed piece in the form of embellishments. “A rotary die cutter adds value with its ability to not only cut the product shape but apply embossing, debossing, kiss cuts, along with standard perforating and scoring processes to deliver complex finishes to the product,” adds Kevin Corwin, product manager, Insignia Die Cutters, Rollem USA.
Also, “a rotary die cutter has the ability to run inline with folding/gluing systems to further increase production output and deliver for instance cut, creased, or folding cartons or other products requiring the glue-and-fold processes,” he continues.
On the flip side, disadvantages of die cutting as a whole include the time it takes to produce a die. If an error occurs in template production, the time to redo it is costly. Dies also have to be made for every specific design, shares Winstanley.
The storage and upkeep of the dies is also a concern. “These must be carefully stored in order to be kept in pristine condition for re-use. Also, there is the cost aspect, as each new design requires the purchase of new dies; as well as the space required to store dies,” notes Bell.
Digital Flatbed Cutters
With the costs associated with creating multiple dies for a versioned print job, and considerable lead times, digital flatbed cutters are favored for shorter run packaging requests and especially prototypes.
“One of the main advantages digital cutting offers is just that—it’s digital. No need for physical die making, maintenance and storage, or management. There is versatility and the ability to easily switch from one job, processing method, or material to another with minimal—if any—changeover and setup times,” shares Beatrice Drury, marketing manager, Zund America, Inc.
Flexibility is a digital cutter’s greatest advantage. “The tooling can be personalized and many different types of materials can be cut and routed, thus adding to the overall product offering. Digital flatbed cutters are able to work with a range of different materials, better serve the customer’s needs, and the fragmented volumes requested for tailor-made product,” explains Bell.
Maureen Damato, partner account manager, Colex Finishing Solutions, agrees that the biggest advantage here is related to production tooling, which offers “unparalleled flexibility and creativity giving the user the full ability to customize any cut and any finish.”
“Digital cutters are great for prototyping where you require a one-off to test your design or a few for consideration purposes. These are also great in environments where smaller run lengths of finished product is required,” adds Winstanley. Benefits include less time to produce artwork, easy-to-adjust templates, minimal cost to create a template, and unlimited design opportunities.
While lack of space and a higher cost of ownership may have once prohibited shop owners from utilizing digital flatbed cutters, that is no longer true. “While businesses might historically have been required to house an array of equipment across the shop floor to handle a range of different materials, applications or finishes, technological advances means obstacles, such as a lack of space or prohibitive costs, are no longer issues. Today, many tasks can be handled with a single device. Robust, industrial devices that deliver reliability, consistency, and maximize productivity have addressed today’s key pain points,” attests Frank Adegeest, VP product strategy and business process, Kongsberg Precision Cutting Systems.
Digital flatbed cutters’ disadvantages are found in their less-than-cost-effective ability to cut one piece at a time, which hampers processing of larger, static volumes of packaging or prototypes. “A perceived weakness is the fact that under most circumstances, only one piece can be cut at a time. While dual-beam or dual-tool processes can potentially double the throughput, no workflow allows for cutting all pieces on a sheet at once,” explains Drury. “However, as is always the case in cutting speed and throughput comparisons, it is important to look at the entire production workflow—from design to finished product.”
Another drawback, according to Van Pelt, is slow throughput speed and increased labor cost related to excess scrap material. “I am not aware of any flatbed cutter that features inline waste stripping capabilities. So manual product collection and waste removal is another issue that increases labor cost and reduces throughput speed. Many current rotary and platen die-cutting machines feature inline waste stripping.”
“For any level of higher production output, the ability to weed the matrix and divert it to waste while delivering only the finished product to a single delivery table is a key advantage for die cutting,” adds Corwin.
Application Volume
Any and all types of packaging applications are performed on both die cutters and digital flatbed cutters. The volume of work dictates when either is used.
“In packaging, run lengths can reach a million sheets or more depending on the products,” shares Chris Raney, VP of postpress, Heidelberg USA Inc.
Whereas, Van Pelt says Therm-O-Type has customers who produce digitally printed packaging in quantities as low as 250 finished pieces. However, he admits this is a niche market and most packaging is produced in higher quantities.
However, Bell attests that these types of numbers are generalizations as “each individual company operates in a different way, both in terms of the finished product and working shifts.”
That being said, she cites that “job lots of up to 500 to 1,000 sheets can be processed on manual or automatic cutting tables, but if job lots are all in excess of 1,000 sheets it would be more productive to opt for a die cutting system.”
“Rotary die cutters fill a unique space in the market for shorter to mid runs of folding cartons, packaging inserts, carriers, and other products. The die cutter offers the printer the ability to fulfill a range of products all produced in house with high profit margins. The ability to die cut, crease, perforate, and add holes and other special finishes enhance folding cartons for beauty, pharmaceutical, and retail products,” explains Corwin.
Highcon customers, according to Lewis, “leave ultra-short runs to the CAD tables and long runs to the analog die cutter, leveraging the Highcon digital converting solution for the short to medium runs. This is particularly valuable today with the market demanding rapid delivery time, online ordering, the growing number of shorter runs, and highly differentiated and customized packaging.”
The types of packaging produced using die cutters include corrugated boxes, foam boards, chip boards, and card stock materials, shares Chen.
Folding carton/paperboard to corrugated and honeycomb materials and even different types of packaging foam for complete packaging systems are often finished using digital flatbeds, says Drury.
Over or Under
Those on the fence about whether a die cutter or digital flatbed cutter might be preferred in their space, the technologies’ strengths and weaknesses really come into play. If you are looking to produce shorter runs or prototypes, a digital flatbed cutter is well suited for a packaging facility’s operation. However, if long, static, repeatable runs are the norm, a die cutter is better.
Raney argues that any print provider looking to create package-type structures requires prototypes and would simultaneously need a finishing device to handle them, which in this case might be a digital flatbed cutting table. “It’s all about the run length. Any print provider that wants to create packaging-type structures will need a way to create prototypes. If they want to do it in house, then they will need a cutting table. However, a cutting table is really only suitable for run lengths up to about 100 pieces, otherwise it will be too slow.”
“The decision to opt for one technology over the other depends very much on the type of production and what the systems will be used for. If the print provider does a lot of small- to medium-sized production jobs, then a cutting table is the most productive system. This would also be the case if the printer does lots of bespoke designs. Cutting tables are also ideal for prototyping. If, however the printer does lots of high-quantity, standard production, with little or no prototyping, a die cutter would be the most suitable system,” advises Bell.
Automated digital finishing devices are essential “in any of the scenarios described above, where the kind of flexibility only digital processes offer is key—either for quickly and easily producing prototypes or, especially paired with high-volume digital printing, in web-to-pack, or other applications that necessitate cutting large amounts of shorter runs or even one-offs,” shares Drury.
Adegeest believes that ecommerce brands are experiencing increased demand for shorter runs, which is a result of further demand for more personalized packaging, and as many countries of the world begin re-opening to consumers—a returning demand for more regional and localized in-store marketing campaigns. For any packaging provider working in this segment, it’s imperative to utilize a digital flatbed cutter.
Speed is also a consideration. ”Die cutters are much faster, with the capability to process different shapes and thickness all in one pass. If speed is in consideration, a rotary die cutter will be significantly faster compared to a cutting table,” says Chen.
Van Pelt notes that tooling is required and set up time is longer, with a die cutter, but throughput speed is dramatically faster.
Beyond volume and speed, substrates and materials are also a factor when determining the cutting process. It is about choosing the right equipment for the job in hand,” recommends Winstanley.
Dubuque sees features like setup and workflow automation and job memory storage in demand on cutting solutions. “These features help reduce the turnaround times on short runs, manage variable data output with minimal waste, and make operations more efficient.”
Money, Money, Money
Deciding to invest in either a die cutter or digital flatbed cutter for prototyping or packaging requires consideration for your company’s capital expenditure (CAPEX). A larger price tag can be daunting, but a ROI is usually quickly obtained when the right system is implemented.
When it comes to digital flatbeds, “as always, the level of CAPEX depends very much on the cutter configuration, size, and level of automation, but starting price for a Zünd system is typically around $100K,” shares Drury.
“CAPEX would vary depending on size and capability of the cutting table purchased, amount of cutting heads, and knife holding positions. A small tabletop version can be as low as $2K to $3K all the way up to large format tables that are over $100K,” comments Corwin.
For die cut options, “the CAPEX for a rotary or platen die cutter would also vary drastically; there are not as many used rotary die cutting systems available as there are platen machines; a oldest used platen die cutting system depending on size could be purchased for around $10K and could go up into the hundreds of thousands for a large used system,” adds Corwin.
It is important to note that a die cutter will require regular maintenance and upkeep to ensure it lasts and these costs could reach annually anywhere from $15K to $20K, says Raney.
Cutting Out to Fit In
Depending on the volume and type of work passing through your print operation, die cutters or digital flatbed cutters are an option. For those looking at shorter runs, higher variability in project types, and even prototyping, digital is a fit. In more static workloads with minimal change in cut templates, a die cutter—rotary or platen—may be a better decision.
It is important that package printers and/or folding carton and corrugated converters should know precisely what they require out of a cutter before making the leap, but in either case the device is able to create unique shapes, which is a necessary skill in today’s packaging market.
Oct2021, DPS Magazine