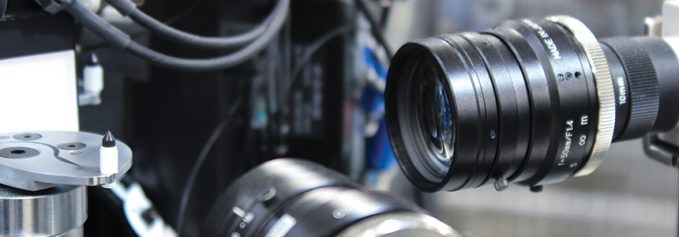
By Olivia Cahoon
Vision-based inspection systems detect quality flaws, protect variable data integrity, and track and trace documents to ensure the digital printing process is accurate and compliant. While all digitally printed applications benefit from the use of an inspection system, documents with sensitive data typically find the most value.
Before implementing or managing a vision-based inspection system, it’s important that print providers become accustomed to standardized procedures so the selected system runs efficiently with their digital press.
Above: Teledyne DALSA’s Linea ML CMOS camera captures RGB or RGB+NIR images in a single scan.
Defining the Role
Traditionally, print providers used human eye inspection to verify that sensitive documents were accurate in terms of quality, data, and style. As printing technology advanced, so did the need for inspection systems. This ultimately led to the creation of vision-based inspection systems.
Vision-based inspection systems are utilized in various printing environments to detect quality defects such as printing contrast, registration, image quality, color accuracy, and barcode grading, as well as to monitor variable data integrity like duplex matching, sequence control, duplicates, missing information, and database management, shares Kareen Pratlong-Vendryes, strategy, marketing, and communication director, Axode.
More recently and thanks to the development of real-time production supervision solutions, inspection systems now track and trace documents throughout the entire printing process from design to delivery. “Thanks to specific data management and tracking software, vision-based inspection systems track products through the complete production workflow and therefore improve overall productivity,” she comments.
Today’s vision-based inspection systems are designed to guarantee three measurements of quality—print quality, document quality, and workflow processes. According to Scott Peterson, product marketing manager, Tecnau, print quality is first and typically includes testing color matching, detecting jet-outs, and confirming barcode readability.
However, quality inspection solutions should go further to monitor the document’s overall quality. “Data integrity tests are one measure of overall document quality, with data validation, data matching, and perforation checks, among other tests,” shares Peterson. Workflow processes should also be confirmed, such as testing for duplicate documents within a job run and confirming proper sequencing.
To achieve satisfactory quality levels, vision-based inspection systems must be reliable and provide 100 percent accuracy. As a result, the systems consist of multiple parts including cameras, lenses, lighting, frame grabbers, and a computer system to process captured images. During the inspection process, Xing-Fei He, senior product manager, Teledyne DALSA, explains that sensors capture an image of the product as it passes through and the vision appliance inspects the image and communicates the result as a simple pass or fail.
“These systems are integrated in production lines to provide a constant stream of information to the operator that is easy to trace back to an individual product,” he explains.
Popular methods of vision-based inspection include flaw detection, verification, as well as identification. Other uses include positioning, which aligns tools for inspection. Measurement checks dimensional accuracy on parts against geometrical tolerance.
According to He, inspection systems are also capable of sorting materials and counting products to maximize efficiency. “Vision-based inspection systems are effective and play a vital part in quality control management for manufacturers.”
Speed & Detection
With the ability to detect print and quality defects, vision-based inspection systems bring a variety of benefits to digital print environments. Today’s systems are designed with the speed and camera technology needed to keep up with digital printing devices.
“With the high quantity of information to inspect on digitally printed content, machine vision inspection is the most efficient and accurate way to guarantee the highest quality possible,” shares He. This is achieved through high frame rate cameras with real-time processing capabilities and large view fields. At the same time, line scan cameras provide high resolutions and inspect 100 percent of the moving surface.
In addition to speed, vision-based inspection systems ensure costly mistakes are avoided by detecting problems immediately without wasting paper or printer resources. According to Peterson, the systems provide valuable insight to operations management—uncovering and eliminating problem and delay sources within the digital print environment. “The essence of vision-based inspection systems can be an important differentiator in print-for-pay operations seeking to win new customers.”
Inline vision systems on digital presses are utilized for many reasons, particularly with inkjet presses. Here, the system finds defects related to inkjet technology like nozzle streaks, color issues, and other special defects, says Michael Almagor, digital business unit director, AVT Ltd. “Inkjet technology is not mature yet and the press itself must have a tool to find the nozzles, color, and other typical defects—normally process defects.”
Defect detection in inline systems also help to reduce waste and overprints for the end user—catering to the digital printing model of short runs and print on demand technology. According to Almagor, defect detection capabilities are integral as every copy counts. “You must alert and find defects on time. With digital, you can immediately print the defected job again.”
Applications With High Stakes
Many applications require the use of an inspection system. Typically, any digitally printed product that involves color or variable data benefits from automated inspection. This includes commercial publications, direct mail, food packaging, newspapers, pharmaceuticals, transactional mail, tickets, and other applications with large quantities of information that is too time consuming to inspect manually.
Generally, three types of print application families are able to find the most use using vision-based inspection systems—print quality inspection, data integrity verification, and production/workflow tracking. “These applications are implemented in many working environments and markets,” comments Pratlong-Vendryes.
For example, inspection systems provide the ability to inspect and track applications like telephone invoices throughout the workflow while also offering rejection before postal tracking. Not only does this offer efficiency, but Pratlong-Vendryes says it saves large amounts of money in postal charges as well as delivery expenses. “In such a scope, a visual system is ideal and provides a very quick return on investment (ROI).”
“Vision inspection systems are designed for any and all applications where quality is an absolute necessity,” agrees Gary L. Parish, president, Complete Inspection Systems, Inc. The devices replace and provide more accurate inspections than operators. “These tasks are usually boring to an operator and the level of errors increase depending on their training and skill.”
This is especially true for operators inspecting large amounts of documents over long periods of time. In such instances, imprinting can occur—the operator sees the same inspection many times and the brain automatically fills in a copy of the document, whether accurate or defected.
For pharmaceuticals and medical device equipment, errors can be life threatening. “The laborious and tedious task of manually proofreading printed or digital files and verifying medical device kits for hours on end can cause an operator to become vulnerable to mental fatigue,” explains Parish. This results in missing or incorrect dosages and incorrect products packaged, which can trigger a recall and affect many lives, he cautions.
Implementation Challenges
While vision-based inspection systems enhance a company’s ability to detect printing deviations, there are still challenges to overcome. In some scenarios, press speeds surpass what the inspection system can handle. Operators should also be prepared to invest and deploy a new system.
Companies that do not have standardized procedures increase the difficulty in deployment. To avoid implementation challenges and truly realize the benefits of an automated inspection system, Parish suggests companies establish paradigms like proper file management. “Operator and administrator training, as well as setup of the automated system are equally important.”
Aside from training, one challenge of inspection systems involves print production speeds. “In the past 20 years alone, presses doubled their effective production speeds, straining the inspection system’s components immensely,” shares Amir Dekel, business unit manager print/VP, ISRA VISION.
In fact, in select applications presses must be slowed down to allow the inspection system to maintain the same speed. In the digital environment, this challenge increases significantly due to the growing use of variable data. While Dekel notes that most of today’s digital print applications are not running very quickly, he believes this is changing rapidly with advanced inkjet printing technology.
As an exception, he sees an emergence of digital printing in the carton pre-print market, which already demonstrates high speeds. “There is no doubt that these speeds will trickle down to the more traditional digital print applications and introduce the same challenge.”
Additional challenges may occur in digital print workflow data layers. At the moment, there is no clear standard for variable data structure and each manufacturer has its own arrangement. Although some prepress players partner with digital press manufacturers, Dekel admits it is not yet an industry-wide effort—creating a need to develop different interfaces for each press and straining inspection system manufacturer development teams.
Issues sometimes encompass production variety. Vision systems don’t have intuition and cannot automatically understand good from bad. They require programming to achieve the manufacturer’s goals. “Every process and product has its own unique challenges,” shares Dan Nadolny, director of machine vision engineering, EPIC Systems Group, LLC.
He says a good integrator’s true value is not the ability to wire a camera into the control system, but to understand manufacturing challenges, design a camera system that creates optimized images, and program reliable inspection algorithms that provide repeatable results. “The design of the vision system is the secret ingredient that makes the difference between just hanging a camera over your product and having a reliable automated inspection system.”
Available Inspection Solutions
A variety of vision-based inspection systems are available to serve the digital print production space. Here we highlight a few.
Based on AVT Ltd’s Helios product line, AVT Helios D is an automatic 100 percent print inspection solution for labels and narrow web digital printing. It supports every stage in the digital production workflow starting with missing nozzle detection to print quality and process control. Available on any digital press, Helios D identifies defects as they occur, such as missing nozzles, spots, substrate damages, and color changes. It is also equipped with a built-in PrintFlow module for inline reporting to review job, order, and roll reports; edit; and export to digital files.
The Axode 180neo2 is a compact integrated vision-based inspection system. It handles up to 3,000 feet per minute (fpm) at 16x10x6 feet. Due to its in-house custom design, Axode’s systems offer real-time, vision-based inspection that provides performance, stability, and long life. Systems are compatible with all printers, finishing machines, and processes on the market.
Complete Inspection Systems, Inc. offers the AutoProof Pro-S Imaging Suite with a 50-inch maximum capability. It is an offline device featuring a modular base that allows companies to configure an ideal solution to their application while maintaining costs. The AutoProof Pro-S Imaging Suite is also pharmaceutical compliant on a global scale and proven to help quality assurance and control personnel to prevent costly recalls. Price is based on customer requirements.
EPIC vision systems are custom designed for each manufacturing client’s needs. Its devices are successfully used in a variety of digital printing applications including lot and data code, label print inspection, and inkjet four-color alignment verification. For label print inspection, EPIC vision systems monitor thermal transfer labels at five to ten parts per minute. The devices inspect client logos, specific government regulated information, gross defects, missing characters, and small imperfections.
ISRA VISION provides several inspection solutions well suited for digital printing environments such as the DigiSTAR for pharmaceutical digital applications and the PrintSTAR to accommodate Fhighly variable content. Both devices handle up to 110-inch wide documents with speeds up to 900 fpm and 100 micron resolution. Higher resolutions are also offered. ISRA VISION utilizes in-house developed and manufactured cameras, which are designed to meet high-speed requirements.
Standard Finishing features the Hunkeler WI8 Web Inspection System. The Hunkeler Control Platform represents a high-performance system for production monitoring and quality control. With the WI8 Web Inspection system, users check the quality and content of a print run, including colors, positions, contours, smearing, jet-outs, and data validation. The system checks quality and content by scanning the entire width of the paper web with a Contact Image Censor (CIS) scan bar to acquire high-resolution images of each page at full speed and comparing those imaging to the control sample. According to the company, printing quality and content errors are identified at an early stage, thereby triggering immediate action and reducing both downtimes and wasted paper. Compact CIS sensors can be mounted easily in specified inkjet presses and Hunkeler devices, and the sensors require no adjustment or mechanical calibration. The WI8 System can be integrated with Hunkeler’s CS8 Cutter, DP8 Dynamic Perforator, and WM8 Web Merger.
The Tecnau WebVision is available in two configurations—WebVision INspect for inline printing and WebVision EXpect for external. The vision-based inspection system handles high-volume transactional print, transactional documents, direct mail, and additional applications where print quality is critical. Depending on configuration, WebVision systems inspect documents up to 21 inches wide with a resolution of 360 dpi. Speeds reach up to 750 fpm.
Teledyne DALSA’s newest multiline CMOS camera, Linea ML, captures RGB or RGB+NIR images in a single scan using color or multispectral models. The Linea ML cameras deliver images at a maximum line rate of up to 300 kHz in 8K and 16K resolutions. When combined with the Xtium 2 CLHS series of high-performance frame grabbers, the new models address the industry’s most demanding applications with improved speeds and detectability.
Videk offers its DocuVision Pro Web Inspection System, an inline, full-page print quality and data integrity inspection system built for interoperability with today’s high-speed color inkjet printers in mind. The solution is designed to provide 100 percent inspection of every image at web speeds of up to 650 fpm, the device is optimized for applications where quality and accuracy of color documents are critical to success.
Ensuring Success
As digital print speeds continue to advance, vision-based inspection systems strive to keep up. These devices help ensure that print providers remain compliant when handling sensitive documents and that output quality is maintained. While manual procedures will always be an alternative to vision-based inspection systems, operators are limited and can’t provide the same efficiency as modern inspection systems.
Jul2019, DPS Magazine