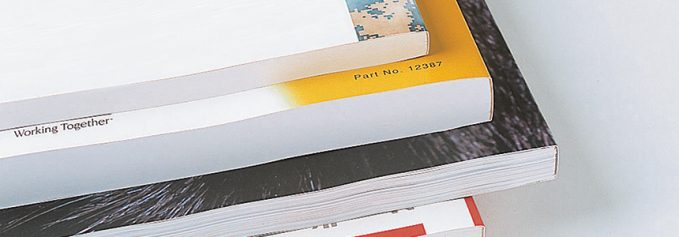
by Cassandra Balentine
Cutting solutions are essential to a modern print environment. The ability to offer diverse options for added value and appeal are increasingly easier to obtain for shorter volumes.
Above: Standard Horizon’s rotary die cutters perform a variety of functions either separately or in a single operation.
Unique cuts are achievable though a variety of manual and digital die cutting processes. This article focuses on rotary die cutters, specifically those well suited for digital print or hybrid printing environments.
Advantages and Limitations
Rotary die cutters tout several benefits for digital print providers compared with other manual cutting methods, including fast set up and easy job changeover, low makeready, and versatility.
Bob Flinn, director of business development, Standard Finishing Systems, suggests that rotary die cutters keep better pace with digital presses compared to legacy equipment and are much less difficult to staff because they don’t require high skill to operate. “Modern die cutting solutions are quick to set up, easy to learn, require minimal makeready and floor space, and are equally efficient on runs of all lengths.”
When comparing rotary die cutters and traditional platen steel rule dies, Kevin Chen, product manager, Duplo USA, notes several advantages to the former, including high accuracy and low cost, especially on high-volume orders; the ability to process sheets at a high rate of speed—offering greater efficiency for longer production runs; precision; and the ability to create custom designs for a variety of different products.
Next to digital alternatives, Flinn points out that rotary die cutters handle a range of substrates and operate at high speeds, even at scale. However, he suggests that laser cutters may have an advantage when it comes to variable patterns for security applications or one offs.
Chen says limitations of rotary die cutters include the turnaround time for typical dies, which take a minimum of two to three days processing time. Customers will need to order a library of dies for many applications that use a lot of space.
Returning to advantages, rotary die cutters are fairly easy to operate, checking off two benefits—labor and time. “The labor requirement can be a single person to run the entire system and there is no need to add subsequent offline steps to complete the work,” shares Lance Martin, VP marketing, MBO America & Komori America.
Many rotary die cutters also handle a range of feeding finishing functions including through-cutting, kiss-cutting, scoring/creasing, variable data, perforating, hole punching, and embossing.
“The combination of these efficiencies and capabilities with the advances in inkjet and digital print technologies has fueled a new market in short-run and specialty printing, social announcements, tags/hangers, packaging, and labeling,” comments Flinn.
Time savings is also presented when the die cut process also incorporates feeding, registration, cutting, and waste removal. “Many flatbed systems require nicks in the cut to hold the matrix and scrap in place so the sheet can be processed through the machine. This requires a secondary manual process to remove scrap, which can be lengthy,” admits Martin. Furthermore, the edges of the product must have nicks to hold that scrap in place. “The rotary die cut process needs none of that. The rotary die cut is ‘nick-less’ and excellent for high-quality work and elegant, smooth edges,” explains Martin.
Many rotary die cutters also transition between semi- and full-rotary mode. Semi-rotary mode covers the repeat length from the range of 30 to 80 percent of the cylinder perimeter so operators don’t have to change different cylinders according to various repeat length jobs. This eliminates the need for more tooling and also cuts speed. In semi-rotary mode, operators reach up to 60 meters per minute (mpm). “For digital or hybrid, print jobs are mostly short run, varied jobs with few labor requests, making rotary die cutters a good match,” offers Fei Hou, technical director, Bro-Tech.
Single-station rotary die cut systems are used for many types of products. “The dies are capable of not only cutting but include scoring, perforating, embossing, and texturing on the same die,” notes Martin. He recommends care be taken when designing the score and the cut lines because the manufacturing process requires a slight gap between the end of the score line and the beginning of the cut line. For work requiring score lines to mate to the cut line, two station systems are necessary.
These benefits are ideal for commercial print environments that need to support small print runs and variability.
One growth area that looks to rotary die cutting is labels and packaging. “Digital presses have significantly increased the demand for shorter runs of labels and packaging across all product sectors. “Customized wine and beer labels, cosmetics, and subscription services all account for increased demand of digitally printed and finished packaging and labels,” says Susan Corwin, marketing manger, Rollem International.
Direct mail also relies on these devices. “Personalized direct mail including local services marketing, financial products, mailers, and fundraising mail all benefit from customized finishing such as die cut shapes, cut outs, unique folds, and perforations,” adds Corwin.
On the Market
Here is a quick overview of some rotary die cutters on the market.
B&R Moll Inc. offers the FlexCut Digital Registering Rotary Die Cutter. The gripper, less digital print-to-cut registration and lead edge cut registration is a large compliment to the hybrid print, digital/offset print environment. The FlexCut 760 can handle a B2 sheet from 8 to 24 pt. Also, it comes in a smaller 20×20-inch format. Both machines feature a single magnetic cylinder with an anvil cylinder for cutting, kiss cutting, and perforating, where the dual magnetic cylinder machine also can handle creasing/scoring.
The Bro-Tech CDF series is developed and designed for the converting and finishing industries in label production and manufacturing. Now available for a web width of 330 milimeter (mm), 420 mm with compact design, the machine supports semi-rotary at 60 mpm to a maximum full rotary speed of 120 mpm. A small footprint with short web path minimizes waste but is highly accurate in terms of precision for cutting and precise registration and wide substrate thickness range from 35 to 280 microns.
Duplo offers a rotary die cutting system, manual rotary die cutter, as well as a digital die cutting system. The UD-310 rotary die cutter delivers packaging and print marketing applications in distinctive shapes and sizes. Processing up to 4,000 sheets per hour, the UD-310 utilizes a magnetic cylinder and interchangeable flexible dies that affix to it to handle paper, laminates, adhesives, and synthetic stocks up to 400 gsm.
Grafotronic offers a range of die cutting machines. Among its products is THE ONE, a single anvil system, which can be set up within just 30 centimeters and is developed to handle even the shortest runs in an effective way. It offers a tolerance of +/- 0.1 mm.
MBO represents the Bograma Rotary Diecutter Systems. Its portfolio includes BSR 550 Basic, a rotary die cutter for most commercial print shops and small converters. This machine includes the feeder, registration system, die cutting station, scrap removal station, and standard shingle style delivery.
MBO also offers the BSR 550 Servo, a rotary die cutter for commercial or packaging printers. The system has an open architecture that allows a variety of feeders, including pile, pallet, and web fed. It delivers additional functions such as inline folder gluers, card affixing, and tip-ons.
Also, the BSR Folding Carton Production System targets the folding carton market. This Bograma includes a two-station cutting and scoring system, which eliminates the issues of the score and cut line on a magnetic die plate. This machine further incorporates an inline folder gluer, pressing station, and stacking delivery specifically designed for the folding carton market. All BSR die cutters are B2 size. BSR rotary die cutters are popular in digital print environments where a high-value printed product requires a single-step finishing process. Martin says this is commonly thought of as a two-step process print to finish.
Rollem offers its Insignia line of rotary die cutting systems, which according to the company, can be changed over in as little as five minutes allowing for ultra-short run work to be processed with minimal operator training. Utilizing flexible die tools, Insignia can die cut and kiss cut simultaneously for label production or die cut and crease for carton work—all without the machine operator performing any traditional makeready and wasting valuable material.
Insignia models operate at speeds of up to 5,000 sheets per hour (sph) and handle stocks up to 24 pt. thicknesses—or 30 pt. thickness in the case of the InsigniaX3. The Series is offered in four model sizes to match press output.
Standard Horizon’s rotary die cutters are capable of performing a variety of functions either separately or in a single operation. For example, pocket folders can be die cut, creased, embossed, and stripped of waste in one-pass. Multiple label sheets can be cut from a larger sheet while kiss-cutting labels. Packaging and hanging applications can have small to large cut outs of nearly any shape blown or punched out prior to delivery and stacking. The RD-N4055 is the latest addition to Standard Horizon’s line of die cutters. The RD-N4055 combines a high-capacity feeder, a single- or dual-magnetic cylinder die cutter, and a specially designed separator and optional card stacker into a versatile system.
The RD-3346 and RD-N4055 die cutters are targeted towards the A3+ printing range. The RD-3346 will accommodate 13×18.11-inch sheets and up to 14 pt. substrate thickness. The RD-N4055 supports sheet sizes up to 21.65×15.74 inches and finished cut pieces as small as 3.15×1.969 inches. However, it is capable of processing a 16-inch wide sheet for standard pocket fold applications and will process 0.5 mm or 20 pt substrates. At feed speeds of up to 6,000 sph and a high load capacity, the RD-N4055 is equally efficient for short, on-demand runs and high-volume applications with minimal waste.
THERM-O-TYPE’s RDC-Flex rotary die cutter is specifically designed for digital printing plants that require high-quality output, automated stripping, and very fast format changeover. The combination of large die cut area, throughput speed, quick set up, automated stripping, and ease of operation make the RDC-Flex rotary die cutter with flexible steel rule rotary cutting dies an important production machine in any digital printing plant.
Cutting Corners Effectively
Rotary die cutters are able to offer reduced makeready and turnaround times compared with some alternative, manual cutting methods. While not digital technologies, the latest entries into the market target digital and hybrid print environments.
Oct2022, DPS Magazine