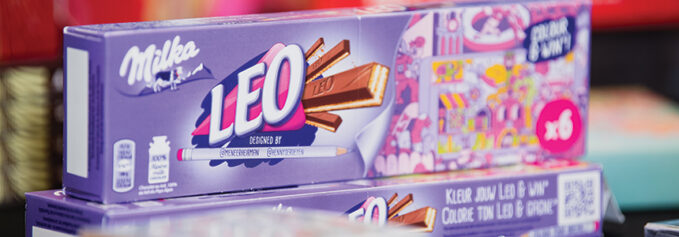
by Cassandra Balentine
When it comes to digitally printed folding cartons, a variety of technologies come together to make the final product. For printing, inkjet and electrophotographic processes are utilized. Digital technologies thrive for sample work, short production runs, and high-value packaging that incorporate features like personalization. From there, finishing solutions shine, offering die cutting, embellishment, and more.
Above: Examples of folding cartons printed by HP. The HP Indigo 35K Digital Press is a second-generation press based on eight years of experience to serve the growing digital folding carton market. Image provided by HP.
Complimentary to Offset
Lance Martin, VP, marketing, MBO America & Komori America, feels that digital printing processes are most valuable when paired properly with offset. “The nature of the digital print process has a couple things that allow on-boarding and development of new customers in the folding carton space.
For example, the Komori IS29s, a UV-based inkjet press, has a wide color gamut, a high degree of repeatability, the elimination of plates, and reduced makeready waste.
“The first sheet from the press is good, meaning testing for new customers is a completely different model because the real product can be printed on the actual production sheet from the actual production device,” he states.
As the customer’s needs grow, Martin points out that the same production process can competitively run their needed production typically up through a few thousand sheets. If the volume grows and versioning becomes high, then the inkjet process could remain the process of choice. “If the volume gets higher still, the producer can choose to stay with digital or move the job to offset where the larger volumes could be produced more economically,” he shares.
Overall, Martin doesn’t view inkjet as a standalone process for folding carton production, but more of a complimentary process to traditional methods.
An example of a segment that utilizes the benefits of inkjet printing is cannabis. “New products are brought to market requiring on boarding and development, easily done in an inkjet environment. Some of these products tend to be more regionally impactful, keeping volumes down and allowing inkjet production to be very competitive,” he notes.
Nanography
Folding carton printing requires the ability to handle the substrate at various weights and thicknesses, fidelity in color reproduction, as well as the ability to hit spot colors that are outside of the CMYK space.
In addition to UV inkjet, another printing concept ideal for folding cartons is nanography technology, which hits all of the above requirements and more.
Amir Shalev, market development director, Landa, points out that Landa’s presses offer full compatibility to mainstream folding carton production thanks to B1 print sheet size and ability to work on any paper and board without pre-treatment—including recycled and uncoated materials.
“Integration to inline finishing at B1/41 inches is critical for converters looking to expand beyond very short prototype runs,” he stresses.
“We are seeing folding carton production across the board in our customer base. We have mainstream converters from the largest global packaging companies who use our presses exclusively for folding carton production,” comments Shalev. “We also find that commercial printers are using the presses’ versatility to expand into folding cartons as a growth area quite successfully.”
Many folding carton trends are apparent, according to Shalev, including reshoring and destocking.
For pharmaceutical, personalized medication and SKU proliferation combined with spot color usage creates a high push for efficient production of packaging and an explicit need for flexible production.
Small- and medium- sized brands in the food and beverage market as well as the personal care segment look to digital technologies to create a variety of offerings for their client base. “They believe in experimenting with the market through quick interactions in social media and subsequent product releases. Our solutions are well suited to take their multiple versions from market testing and into full production,” says Shalev.
In terms of future features, Shalev adds that variable data printing is an exceptional capability that is still not widely used, but holds promise for adding with things like security features and unique consumer engagement and tracking.
High-Value Boxes
Electrophotography—specifically liquid electrophotography (LEP) as offered by HP—is well known for its capabilities in digital folding carton production.
The HP Indigo 35K Digital Press is a second-generation press based on eight years of experience to serve the growing digital folding carton market. “HP Indigo’s LEP technology delivers the highest print quality in digital folding cartons. It offers an offset look and feel on a digital press and the most advanced color management system on the market,” says Shahar Lev-Ari, product marketing manager, HP.
The HP Indigo 35K Digital Press is a full folding carton production line—equipped with an inline priming unit and utilizes the Tresu iCoat II to create an efficient handoff between processes.
The inline priming unit gives converters the flexibility to choose virtually any off-the-shelf special media, such as metalized, blackboard, or uncoated Kraft, which are trendy options especially in healthcare and cosmetics.
With HP Indigo’s LEP technology, Lev-Ari says converters reach color faster, with minimal makeready waste. “This is especially valuable for jobs where media costs upwards of $1 to $2 per page.”
He says HP Indigo customers use the digital folding carton presses primarily for high-value boxes common in personal care and healthcare, where high standards of print, many SKUs, and premium/limited-edition items are in demand.
Lev-Air also see customers who leverage the value of personalization to a variety of products, such as cups with variable data publishing, trading cards with full control of randomization, and gift cards on cardboard or synthetics.
Feature sets that matter for digital print include very short makeready and automation. “Especially today, where the time from order to box decreases drastically, there is substantial value in a press that can support multi SKU orders, zero inventory, and just-in-time production. It allows our customers to be very competitive, even with one-day turnovers,” says Lev-Ari.
Toner-Based Production
Across the board, trends towards more sustainable options—less plastic—are all the rage.
Therefore, Danny Mertens, corporate communication manager, Xeikon, is seeing large growth in the use of paper-based materials and mono-material solutions that are easier to recycle.
“To this end, Xeikon introduced TITON toner, a new technology specifically designed for paper-based flexible packaging. TITON offers a unique combination of highly resistant, food compliant, and recyclable digital print that no other technology can match. It provides converters with a more sustainable way forward in digital flexible packaging production,” says Mertens.
In addition to excellent materials handling and 1,200 dpi resolution printing, Xeikon presses use toner technology that stands out from the competition due to its guaranteed food safety, which meets FDA regulations. “This makes it suitable for cups for hot and cold drinks, ice cream, popcorn, candy, and other snacks. With short production and fast delivery times of low minimum order quantities, personalized or branded cups become a possibility even for small brands, cinemas, theaters, shops, or local events.”
In fact, a very successful application is digitally printed paper cups. “Paper cups is a fully developed solution that is offered in cooperation with Xeikon’s network of Aura Partners covering all print media, software, consumables, and equipment,” adds Mertens.
Folding Carton Finishing
A die cutter is one of the most important pieces of finishing equipment for those looking to add folding carton packaging. We dedicate an entire article to die cutting in October, but here we present some specific information as it pertains to digital folding carton production.
Juan Kim, CEO, Valloy Incorporation, points out that only five percent of the market has migrated to digital in packaging, a number quite low when compared to segments like signage and commercial print. “However skillful operators for analog printing and cutting are getting older and younger people do not want to learn those analog machines, so there’s no other way to move to digital solutions. Production costs are higher at the moment.”
Automation is the way of the future in finishing, and Valloy’s new DuoBlade FX features full automation and offers a special PERFECT CUT algorithm. “It is tracing the exact path of cutting for dragging knives by true simulation, not just simple offset compensation like others.”
The machine has two actuating heads, which means operators can put the same tools or different tools for each. “If you put cut knife tools for both heads, production time can be doubled for kiss cutting or full cutting. If you put different tools for each, you can do kiss cut and full cut at the same time.”
Kim points to pharmaceutical products as one of the prime industries moving to digitally produced packages now. To meet their rapidly varying amount and contents of the package, variable data is key.
The MBO Group, which is part of Komori, provides a die-cutting solution that Martin says offers makeready, productivity, and waste characteristics that match the digital print market. The BSR550 fits the most common B2 sheet size and uses low-cost flexible magnetic plates to die cut, score, perforate, emboss, and texture the sheet in one pass. Makereadies are made in only a few minutes with no die test striking and shimming is required.
“Furthermore, internal and matrix scrap is stripped away automatically so it is ready for folding and gluing or any other final finishing step. The stripping process is nickless, which creates a very clean edge fitting the insert, point of purchase, and blister pack market well. For folding carton work, digitally printed sheets can be loaded into the die cutter feeder and in a single pass can be die cut, scored, perforated, textured, and blanked, ready to be finished,” says Martin.
The new market wants a fast turnaround on orders with low waste and consumables, contributing to a lower carbon footprint. “Because it is B2-sheet size, many common products in the pharmaceutical, medical device, cosmetic, and electronics markets fit multiple-up on the sheet. Most products in this segment use 18 pt stock or less, which also fits the BSR 550 well, and covering about 85 percent or more of the market. And with the larger sheet size and up to 12,000 sheets per hour (sph) speed capability, the die cutter can follow the customer into longer runs as they grow. This system really is agnostic to the print process of the sheet and it works as well for analog technology as it does for digital technology,” he offers.
Rollem International also offers a die cutter. Corwin points out that folding carton work is ideal for its Insignia line, which has been adopted by many printers, specifically for the purpose of moving into packaging and gaining access to that high-value market. “With the ability to perform not only creasing, but perforating, folding, and gluing, carton work is handled with ease on the Insignia.”
The Insignia Series of die cutters are production-geared machines that handle both shorter runs and larger quantity output up to hundreds of thousands, depending on the job. Insignia will die cut, kiss cut, crease, perforate, and emboss a virtually unlimited number of products. The folder/gluer unit operates either inline or near-line with Insignia to provide uninterrupted finishing—flat sheet in, finished, creased, cut products are produced, all in one pass, with one operator.
“The Insignia’s setup and changeover time is quicker than competitors, the register is perfectly repetitive forever with zero maintenance or potential to fail; others are reliant on electronic components which over time will not hold true,” states Corwin.
She also feels the need for skilled operators differentates analog and digital folding carton finishing. “Most analog technologies such as windmills or platen die cutters require a seasoned operator with knowledge of handling the heavy iron machines. A digital die cutter as such does not require a high skill level to operate the unit. Some experience with machinery is a plus, but most operators can be trained within a few days. Most skilled operators are aging out of the industry with no replacements in sight,” says Corwin.
She points to job changeovers and makeready timeframes as another important differentiator of modern die cutters. “Utilizing either single or sets of male/female flexible dies, these dies are relatively easy to adhere and remove from the magnetic cylinders. A 20 to 30 minute set-up on the Insignia rotary die cutter eliminates down time and increases production.”
Tooling is another consideration. “Creating flexible dies for a rotary die cutter involves prepress Adobe InDesign knowledge with just a slight learning curve required. The artwork is sent out to one of many die makers who can turn the dies around within a few business days. The entire process is much faster than producing steel-rule dies.”
The sustainability factor is more prevalent today with movement trending away from plastic packaging. “The demand for paper-based cartons across all segments continues to increase even in the food category with the development of safety tested coated cartons,” offers Corwin.
Eye On Automation
Getting a high-quality print is only half of the battle when it comes to folding cartons. Automation plays an essential role.
For digitally printed folding cartons, Sauter says short runs need automation. “This is the credo for KAMA’s finishing solutions and the guideline for further development. Having focused on short-run finishing solutions as a machine manufacturer for well over a century, we have experience on a large scale and are also well ahead in the field of automation for finishing digital prints.”
Sauter sees two distinct differences when comparing digitally printed folding cartons with analog. The first is maintaining accurate registration from print to cut to ensure customer satisfaction and brand integrity. “KAMA’s AutoRegister AR3 on the ProCut 76 Foil ensures the highest precision of 0.1 mm for digitally print sheets and is capable of aligning even twisted sheets precisely with its skew adjust function. That is how we can apply hot foil stamping and tactile effects in high-end quality on digital prints.”
The second is the importance of quality control in digital printing because every sheet and every blank can be different. “The KAMA workflow solves the challenge with inspection and ejection of defects in the FlexFold 52i folder gluer with different inspection levels depending on the type of folding carton—highest level for pharmaceutical packaging.”
KAMA offers a complete finishing workflow for short-run folding cartons after printing—from die cutting, creasing, stripping, and blanking—all on the ProCut 76 Foil Packaging Edition as well as folding and gluing on the automatic FlexFold 52i folder gluer with the shortest changeover times.
Folding Carton
Advancements in digital printing technologies as well as the finishing equipment designed to support them in the area of folding carton production is sure to make an impact in this space over the next few years. The demand for high-value, short-run solutions is ideal for testing new products and markets, onshoring and destocking, and often support environmental initiatives.
“Digital print offers brands the flexibility to react quickly to the market with highly customized jobs printed just-in-time with multiple SKUs on standout, specialized media, with brand protection,” concludes Lev-Ari.
For more on digital folding carton production, check out our webinar on the topic, dpsmagazine.com/webinars.
Sep2023, DPS Magazine