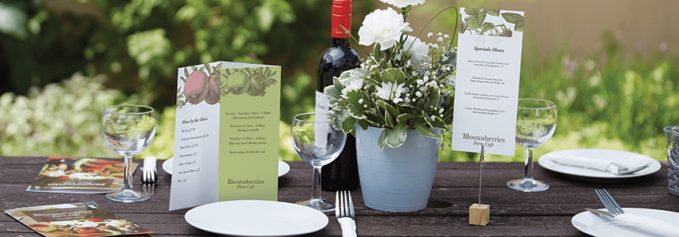
By Cassandra Balentine
An essential industry, many print service providers (PSPs) pushed through the first wave of COVID-19 with trepidation. As the reality of the pandemic set in, they persevered with new challenges.
Shown: Earlier this year, HP introduced a new wave of innovations for HP Indigo digital printing.
Digital print technologies, automated equipment, and workflow tools are essential for improving productivity, limiting waste, and reducing the need for skilled labor. While these trends were already happening prior to COVID-19, the pandemic has accelerated their importance. We’ve asked industry players to weigh in on these issues.
Supply Chain
Print providers are affected by supply chain and pricing issues, especially in regard to paper.
The media supply chain is very global in nature, employing base material production, coating, and converting in various countries and locales throughout the world. “The labor and COVID-19 issues being dealt with differently around the world impact the paper and media business. One way to navigate this crisis as a print provider is to work with your reseller to forecast your expected need for material,” suggests Reed Hecht, group product manager, Professional Imaging, Epson America, Inc.
Many paper mills reduced capacity leading to shortages and hence price rises. In addition, freight costs in general also increased. “I don’t see this ending soon so stock up,” advises Sal Sheikh, VP marketing, Large Format Solutions, Canon Solutions America.
“The paper market is weathering the same perfect storm as several other raw materials. Among many factors, delayed demand, logistics, and a rigid production process are putting a squeeze on paper,” states Dmitry Sevostyanov, CEO, Customer’s Canvas by Aurigma. He predicts the market will figure it out over time, but in the short term, this is a headache for printers. “As a risk management strategy for the interim, I see improving efficiency and better inventory tracking with incentives for buyers to print on paper stocks that have less volatility.”
Supply chain disruptions created by the pandemic in 2020 have carried well into 2021. “Global outbreaks continue to affect manufacturing, consumption, and the logistical movement of goods through critical gateways. When you combine this with the rise in raw material costs and the shortage of freight, companies—no matter the industry—are under pressure worldwide,” says Meredith L. Collins, customer marketing manager, Domtar. While this situation is expected to continue into 2022, there are things you can do to help mitigate the impact. “Plan ahead as much as you can and communicate your needs with your paper supplier early. Flexibility on the size and type of stock will also be beneficial, should your product of choice not be available,” she recommends.
“It’s safe to say we are in the midst of tectonic global shifts that will reverberate for a long time to come. The immediate shortages and price uncertainties will be with us for at least a year yet. Those nimble enough to manage through these times in partnership with the right suppliers will emerge stronger,” stresses Victor Gomez, director, Industrial Labels, Epson America, Inc.
As media supply rates continue to impact market pricing and availability, it is forcing print providers to utilize a wide range of paper types to meet their customers’ print deadlines. “For example, we see some print providers utilizing more super calendared, uncoated papers,” comments Robert Barbera, director marketing, production solutions, Canon U.S.A., Inc.
For labels, while many providers are enjoying a sustained boom in business, it is constrained by how well their suppliers can keep up with the increased demand. “Shortages and price increases are felt keenly by converters because label constructions marry lots of elements from specialized suppliers—e.g., substrate, ink, coatings, liners, laminates, presses, finishers—and must be coordinated to arrive on time, every time,” notes Gomez. “Unmet deadlines are costly or represent missed opportunities. Converters have seen delivery delays lengthen with some of their suppliers due to capacity constraints, scarce raw materials, or logistical problems. Supply disruptions cause converters to turn to trusted, reliable suppliers with contingencies and multiple plants, preferably vertically integrated so they depend on fewer third parties themselves.”
“We see customers navigating this differently depending on their size and the markets they serve,” shares Mary Ann Rowan, chief experience officer, Solimar Systems.
While some are choosing to purchase more paper and hold it, others don’t have that option and need to optimize their usage and processes to adjust the cost it takes to produce orders for customers.
Rowan points out that many providers don’t have control over the supply chain and pricing from their providers; the answer to navigating it then falls to creative solutions to drive efficiencies.
Unfortunately, Bill Papp, product manager, Document Data Solutions, doesn’t expect to see any meaningful improvements in the supply chain until 2023.
Collins adds that going into 2022 there will still be challenges within the global supply chain that will impact everyone. “It’s important that we continue to plan ahead of projects as much as we are able, to ensure that the materials needed for those projects are available,” she suggests.
“From a software viewpoint, this is where we believe watching your workflow and understanding from the time work comes into your print and digital production factory to the time it is delivered where you can optimize is so important. By reducing mistakes and manual processes we have seen customers take six figures out of their costs. And that doesn’t have to be one time, it can be a consistent reduction while also opening the door to more throughput and business growth opportunities,” adds Rowan.
Labor Shortages
Another challenge is access to skilled workers. PSPs are forced to operate with fewer or less experienced employees.
Collins points to a phenomenon called “the great resignation” happening, which is resulting in mid-career workers leaving companies in search of different opportunities. “It’s important to retain those employees as they have the experience and knowledge needed to mentor and train new employees. It’s a good practice to look at your retention plan to ensure that you are providing incentives for employees to remain at your company.”
Attracting and retaining skilled workers is one of the biggest challenges printing industries are dealing with. “Some print providers decided to shut down their offset press operations when their lead press operator retired,” says Barbera.
Even before the pandemic, the printing industry was undergoing a generational shift with difficulties finding replacements for retiring older pressmen. “I remember a conversation with a label converting business owner in 2015 who told me, ‘kids nowadays don’t want to spend five years in apprenticeship learning how to make a flexographic press hum.’ But she went on to add that young workers were happy to work with digital presses, which were much more familiar to them,” recalls Gomez. “Plus, training was much easier and shorter. That trend has only accelerated under the current crunch.”
“While some printers retained employees through the pandemic, others were forced to reduce their workforce,” admits Collins. “Once jobs began to resume and printers looked to re-hire, it quickly became apparent that there was—and still is—a shortage of workers. This has motivated companies to continuously figure out how to do the work with fewer people. This includes looking at processes to figure out how to eliminate non-value added work and investing in systems that would help automate tasks.”
Digital printing solutions have a shorter learning curve so it is easier to train and on-board new operators. “We need to continue bringing new levels of automation and user interfaces that allow operators of all skills to increase their productivity and print quality,” says Barbera.
Lance Martin, VP marketing, Komori America & MBO America, agrees, adding that digital presses provide an appealing environment for a younger workforce, as there seems to be a move away from factory labor jobs.
Traditional offset press systems are similar in that computer-controlled systems with integrated artificial intelligence (AI) run the press, allowing less experienced operators to achieve great results. It is interesting to note that the use of these new systems requires a new management model to instill methods and processes that take advantage of the automation.”
Papp points out that hybrid inkjet solutions are able to print inline with an offset press adding variable data to fixed print in one process thus eliminating multiple touch points seen with a multi-pass—offset print the shell, then personalize on a separate inkjet or toner box—operation.
“Web to print and other automation technologies address the worker shortage by increasing efficiency,” says Sevostyanov. However, it’s one thing to discuss automation in the context of reducing costs. “When you can hardly find any workers to receive and fulfill the orders, it becomes a matter of existence in the market.”
Companies are also focusing on software automation and equipment to support workflows that require less worker interaction, which Hecht says was a trend in years leading up to COVID-19. “This is driving investment in new and upgraded hardware, software, and complimentary workflows and will help companies still meet their customers’ needs with fewer workers.”
“The way forward with skilled workers and labor challenges is the adoption of technology where it is beneficial and positive to the operation of the business,” notes Rowan. Automation, quick implementation, do it yourself day-to-day management, and superior support are required from the vendor community. The important part of looking at this from an organizational perspective is that many things can be accomplished with technology, which makes it possible to navigate these challenging times with the availability of workers. “Since we are not discussing job replacement, it also creates the possibility to implement these solutions within an organization less resistant to change. The key is to make sure you have a good relationship with your providers, a good understanding of your current state and the path to your desired state of operation. Forward-looking vendors are keeping their finger on the pulse of their key markets and seeking to deliver solutions that will help their customers and potential customers meet their objectives.”
Haim Levit, VP/GM, HP Indigo, also sees a greater shift towards automation. “Considering the labor shortages, our industry is experiencing, as well as the drive towards agile supply chains, the rise of ecommerce, and the increase in short runs to levels not seen before, there is no doubt this will be a long-term trend.”
Because labor cost and availability has been a growing problem for many years and the events of 2020 have only accelerated the affect and exacerbated the problem, Martin says the current state is a robust movement to autonomous systems and what Komori calls connected automation, using less labor.
Sevostyanov highlights a related issue that he feels may fly under the radar. “Printers are increasingly losing skilled developers that can handle the automation process to companies like Amazon and other giants. It’s nearly impossible for printers to match these job offers from major corporations, which creates a fundamental barrier to adopting automation.”
Future Insight
More of the same is expected into the new year. PSPs should continue to pay attention to trends, supply chains, and invest in automation when possible.
“The economy should further improve and lead times on products will reduce as shipping companies catch up on their back log,” shares Sheikh.
Vendors that support the industry are watching the demands, and continue to innovate to help support their production print customers. “This innovation also goes beyond the product solution and includes advancements in business tools to help optimize production and advancements in predictive and remote service technologies to help them maximize their up-time,” says Barbera.
Hecht agrees, noting that Epson is looking to bring to market new products over the coming months and years that will increase opportunities for customers and help PSPs harness the potential growth of their legacy markets and expand into new markets.
Sevostyanov feels that externalities will likely remain unpredictable, so printers’ only leverage is to optimize their internal process. “Providers will continue to focus on software and view investing in new machinery as too risky in the current environment. They will pursue new sales channels and carry on improving customer service. Recent surveys suggest that more than 50 percent of printers are going to invest in software in the coming months. We will definitely see some inspiring software projects from printers in 2022.”
Hecht says another industry disrupter is software that connects us together and enables us to work from wherever we are. “An example of that is the Epson Cloud Solution PORT that enables customers to remotely monitor Epson hardware, including the ability for remote support from Epson or user self-repair. This Epson Cloud Solution PORT platform is one that Epson will expand over time and allows managers and business owners working remotely to have a better handle on their business as it changes.”
“The pandemic has taught many of our customers to invest in products—hardware, ink, media, software—that are technically solid, reliable, and allow for versatile output applications as market changes could dictate volumes quite quickly,” says Hecht.
Martin believes that the drive for automation, shorter runs, less waste, and full process controls will dominate the print industry in all the sectors Komori touches—commercial print, packaging, digital and conventional, security, currency, and printed electronics. “It follows the discussion path of Industry 4.0, or the fourth industrial revolution, integrating the power of computers, digital data, AI and electronic communication with and throughout manufacturing. There is really no reason for this drive to moderate. The motivating factors, such as smaller labor pools, competitive technologies, rising costs, shorter turn times, and the need for additional value, are not going to revert.”
Levit says security and brand protection is an ongoing concern. “The need for anti-counterfeiting and other brand protection solutions is on the rise, and this is an excellent high-martin opportunity for print providers. Analog technology is limited in its ability to handle these threats.” Solutions like digital security inks, substrates, and origination software are the new frontier in this field. “I see huge potential growth with digital print solutions for governments, authorities, finance, and other institutions that deal with secure documents, as well as with brands that need to confront counterfeiting issues, particularly in the nutraceuticals, cosmetics, and food and beverage industries.”
Gomez points out that the shift in consumer behavior that has been supporting shorter runs—and digital printing along with it—is unlikely to reverse.
When it comes to trade shows and other in-person networking and educational events, the jury is still out.
“If the pandemic has taught us anything, it’s to not make predictions,” notes Gomez. “But as vaccinations advance, we can expect more in-person events to return in earnest. Whatever can be done virtually and remotely will still be done, but travel budgets won’t disappear entirely.”
“It will be interesting to see what trade shows and conferences look like next year. We’ve had almost two years to build a better mousetrap when it comes to hybrid engagement with our customers. I can’t wait to see how companies have adapted,” adds Collins.
Overall, Rowan expects to see more of the same in 2022. “Likely, we will see volumes continue to increase, but what is unclear is whether people will return to the same activities as 2019. 2022 will be a year where we continue to make moves as a print industry to make each and every process the most efficient possible while trying to empower those in the production chain to make decisions, and manage and answer business and customer experience requirements no matter where they are located.”
Accelerating Change
The pandemic has brought real challenges to the print industry. Tools like ecommerce and automation help to ease the burden of some, but issues like supply chain shortages and access to skilled labor will be around for the foreseeable future.
In particular, the label industry has been very resilient, and actually grown, through these challenges. “It’s clear that the best is yet to come,” concludes Gomez.
Nov2021, DPS Magazine