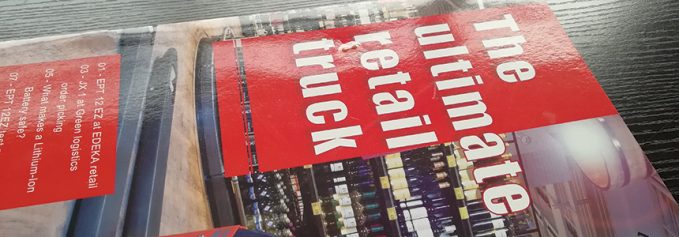
By Olivia Cahoon
Laminators are often utilized during the finishing process to protect and preserve a variety of digitally printed graphics. Depending on the digital printing technology—inkjet or toner—hot and cold lamination is available in a variety of configurations like roll, pouch, heat shoe, and liquid devices.
In addition to the presence of laminators in printing environments, they are popular for a variety of inter-office organizations. Depending on your specific business requirements, a range of products are on the market for lamination needs.
Above:Single-side OPP roll film lamination applied with Sunfung Technology’s Hydraulic Laminator
Protecting Surfaces
Digitally printed output is laminated for special effects, added durability, and enhanced quality. Lamination is utilized to complement high-quality applications.
For example, digitally printed work is often embellished to stand out from the competition. “The visual and feel of lamination—glossy, soft touch, matte—helps to create a distinctive product that customers can use to signify their brand and print shops can use to differentiate themselves,” shares Max Allen, dealer manager, Graphic Whizard.
Lamination not only provides printed pieces with added visual and tactile effects, but it also increases the product’s lifespan. “Whether it is an ID badge that needs to last indefinitely or a business card that needs to survive a pocket full of change, lamination helps to ensure that piece continues to look just as good as when it was first produced,” offers Allen.
Lamination acts as a protective surface to guard prints against scratches, smudging, and fingerprints. It also offers the ability to frequently clean printed products using regular soap and water while withstanding harsh chemical cleaners used in hospitals or bathrooms, adds Brian Biegel, marketing communications specialist, D&K Group, Inc.
In addition to added durability, laminated products offer rigidity and thickness. “Lamination provides a durable way to protect and enhance almost any type of printed material,” agrees Joe Bondonna, product manager, Spiral Binding Company, Inc. “Materials that are laminated just look better,” he comments.
A variety of wide format applications are commonly laminated, including both indoor and outdoor signage, posters, retail displays, trade show graphics, vehicle wraps, and wall displays. “The list is endless as to what you can laminate. If you want to preserve or protect, think lamination,” shares Bondonna.
Commercial applications like catalogs, brochures, menus, and mail also benefit from lamination.
Laminator Types
A variety of laminator types are on the market, including pouch, roll, and heat shoe configurations. Devices are available with cold and heat options in a number of sizes. For this reason, it’s important to consider which type is best suited for the specific printing technology used, intended applications, and environment.
Hot & Cold
Today’s laminators are designed for use with both hot and cold laminating films. Determining which method is best depends on the print provider’s applications and media.
Cold lamination is typically found in print shops that predominantly use vinyl-based media and adhesive stocks for exterior applications like banners, vehicle wraps, and window graphics. Cold laminators are easier to operate and safer to use than hot lamination because they do not require electricity and the user controls the speed. “The moment that you are ready to laminate, the machine is as well,” shares Kevin Chen, product manager, Duplo USA.
Hot lamination is typically less expensive than cold lamination and the items are more durable. Films for hot lamination are processed in two layers—adhesive reside and polyester. The material is placed between the layers, which is then placed in the machine that melts the adhesive onto the sheets, says Chen.
The biggest disadvantage of using hot lamination is that it cannot be used for heat-sensitive materials or inkjet inks. “If you are using this technique on inkjet paper, the ink in the paper may melt,” explains Chen. It’s also a more time-consuming process than cold lamination as the machine must heat before laminating.
Roll Laminators
Roll laminators accommodate documents with both large and small widths spanning up to 81 inches wide. Available in hot and cold variations, the devices require corresponding hot or cold film to laminate. Most roll laminators with a 27-inch print width or under are thermal and documents are typically hand-fed into the machine, says Dan Charwath, product marketing manager, narrow format lamination, GBC/ACCO.
Wide format roll laminators offer advanced features compared to narrow format devices, but also require training. “Wide format roll laminators are great for large applications such as outdoor signage and point of purchase graphics,” shares Charwath. Wide format devices provide a variety of heat assist configurations and typically have mounting capabilities.
Roll laminators are available with manual and automated options. After manual feeding, laminated prints are hand trimmed or finished with an automatic cutter. Fully automated roller laminator systems are also available where prints are automatically picked up, transported through the laminator, and cut on the backend, says Biegel. Commercial laminators with feeders are typically cost effective for large volume jobs, such as direct mail postcards.
Several materials are compatible with a roll device, including acrylic, metal, rigid substrates, and films such as nylon, polyester, and vinyl. “It’s also possible to use textured or specialty laminating films that are sometimes ten mil or thicker,” adds Biegel. Print providers that often handle rigid substrates, such as foam board or flatbed-printed boards, typically use roll laminators.
The devices are most often seen in print shops for media and size versatility as well as the ability to run single- or double-sided films. “This minimizes waste and increases throughput which transfers to labor savings,” comments Allen. However, he notes that they are generally more expensive and can be labor intensive in high volumes to get the laminated piece to a finished product.
Pouch Laminators
Most pouch laminators have a maximum width of 41 inches with desktop sizes also available. Pouch devices are typically the smallest and most inexpensive option for digital printing. However, it’s only compatible with laminating pouches specifically designed for the machine type. “A printed image is manually placed inside of a laminating pouch that is then processed through the machine,” explains Biegel.
Pouch laminators are common for menu and letter-sized documents or small runs that may require two-sided lamination. Pouches are available with round corners for applications like business cards, ID cards, luggage tags, and menus. Most pouch devices are thermal, although many also include a cold setting and are available in nine- and 18-inch width configurations, says Charwath.
Pouch laminators are easy to use, compact, and cost effective for occasional lamination. However, Charwath believes loading a document into the pouch and aligning it can be time consuming. “Pouch laminators can also be limiting because the maximum size of the device is often the dimension of a legal sheet.”
Due to the labor required to place the images inside the pouches, the pouch laminator is best suited for small volumes. It can operate at speeds less than five feet per minute, which Biegel believes makes it less efficient than other laminators.
Heat Shoe Devices
Heat shoe—or hot shoe—laminators are similar to roll devices. The main difference is that a laminating film moves over a stationary heater to activate the adhesive rather than a rotating roller. A non-heated roller set then squeezes the materials together to bond. According to Biegel, stationary heat shoes frequently scratch laminating films, so they are typically compatible with only polyester films due to their hardness.
Liquid Laminators
Liquid laminators apply a special liquid coating that hardens when cured. Biegel believes these systems are efficient for applying thin coatings but are also limited in applications. “Liquid lamination generally doesn’t offer the same amount of protection or durability that a laminating pouch or film will,” he explains. Liquid laminators also require daily purges and cleanup to ensure the device works properly.
Laminating Challenges
Lamination provides added durability and quality, but it also presents challenges. Before selecting a laminator, it’s important to consider the printing technology used—inkjet or toner—and whether it is compatible with the lamination. Applications should also be considered.
In the laminator market, the biggest challenge is ensuring the printer ink is compatible with the lamination adhesive. Ink types vary depending on the printer and poor adhesion is a result. “When the film isn’t adhering, it is best to let the ink sit and dry overnight, turn up the heat, and run the laminator on a slower speed,” suggests Charwath.
Toner-based devices with fuser oils often present challenges with delamination—the film doesn’t stick to the print. This occurs with heavy coverage and dark colors. To avoid delamination, Bondonna suggests print providers use a laminating film with an adhesive formulated to the application. “There are many on the market,” he assures.
Before laminating, the print should also properly outgas and dry. To avoid adhesion difficulty, Carl Hoffman, director of sales, Royal Sovereign, suggests print providers consider how long this process takes. To help, most laminate and digital printer suppliers have specific guidelines for wait time.
Avoiding fading and maintaining color vibrancy for long-term usage is a common challenge when laminating wide format graphics, especially outdoor signage. The simplest solution is to select a laminating film that uses UV inhibitors to reduce fading. “There are plenty of applications where that isn’t needed, and you can use laminates without UV inhibitors to save money,” adds Bondonna.
When shopping for a laminator, it’s also best to choose a device that is as wide or wider than the output device as laminators tend to have a long lifespan. “If you intend in the future to print wider, possibly plan on purchasing a larger laminator now so that you do not need to purchase a wider unit later,” suggests Hoffman.
The Coating Alternative
Lamination isn’t the only form of protection for digitally printed graphics. In some cases, print providers select coatings for a thin layer of protection on a large number of products. However, there are scenarios where a laminator is better suited for the specific job.
Coatings are typically not cost effective for short runs as the equipment can be a significant investment, shares Charwath. “Lamination can offer so many additional benefits, including added rigidity, UV protection, and different finishes,” he adds.
Coaters are also typically big in footprint, while laminators are available in compact figurations. “Coating is more complicated for service and maintenance compared with laminators,” comments Kevin Zhou, sales director, Sunfung Technology Corporation LTD. “Lamination is better for digital print on demand, coaters are for mass production, which is not flexible enough.”
Compared to coatings, one of the largest advantages of lamination is durability. Although coatings enhance the printed image, Bondonna believes they do little to protect against abrasion, creasing, wrinkling, dirt, grease, and chemicals. “Coatings do have their place and look great used as a spot accent over something that is laminated with a matte or soft touch type of laminating film,” he offers.
Lamination also adds to the paper’s structural strength while solving coating challenges, such as cracking and cleanup. “It removes the messy cleanup of the coatings that printers hate,” shares Steve Truan, major account representative, Nobelus. “There are films on the market that are very similar in cost, so to get the protection needed without the cleanup is a huge bonus.”
In addition to better resistance, Radu Vintila, GM, SAS Sustainable Technology Inc., says that lamination can be used for direct contact with food, whereas coatings cannot touch consumables.
Available Laminators
Here we provide a selection of new and popular laminators suited for digitally printed output.
The D&K Group, Inc. offers the AutoKote Pro, an automatic digital laminator for hot lamination. With a 26×30-inch maximum size capability, it is suitable for short-run and large-volume digital projects. The AutoKote Pro runs up to 50 feet per minute (fpm) and features a compact design complete with an automatic sheet feeder, laminator, and diagonal cutter. “This system allows a single operator to place a stack of prints onto the feeder and retrieve laminated sheets on the back end with minimal adjustments and labor required,” offers Biegel. It is available for $50,000.
The Duplo USA DFL-500 Dry Coat/Foil/Laminator is a three-in-one roll laminator for hot lamination. It features a standard dust removing system, de-curling system, and auto film slitting and cutting system. The device handles media up to 13×24 inches with a maximum 15 page per minute speed. It’s intended for run lengths from 1,000 to 2,000 sheets. According to Chen, the DFL-500 is available for $17,500.
The new GBC Foton 30 is an automated cartridge desktop laminator with hot lamination. It offers a maximum 11×36-inch size and laminates three documents per minute. The Foton 30 has a deskew functionality to ensure documents are properly aligned. Three operation modes allow any paper thickness or shape to be fed and ensures the machine processes quality lamination for most digitally printed products. “Simply place your documents in the feed tray, press run, and walk away,” comments Charwath. MSRP is $840 and subject to change.
The Graphic Whizard PT 33LSC is a thermal roll laminator for short-run to high-production run lengths. It slits and cuts to finished size, saving time on trimming and cutting after lamination. The device handles sizes up to 13×19.7 inches with variable speeds up to ten fpm. The PT 33LSC cuts to bleed and also includes pouch mode with several encapsulation sizes or true single-sided laminating with the anti-curl device. “Automatic setup, productive speeds, and the efficient pile feeder makes for a set it and forget it laminating experience,” says Allen.
Nobelus offers the Komfi Amiga 52 fully automatic laminating system with top feeder. Options include an inline slitter, inline perforator, flying-knife separator, and Sleeking feature. With a maximum 65 fpm laminating speed, the device handles sheets up to 20.5×29 inches and produces a maximum 1,800 sheets per hour. The Amiga 52 offers two automatic feeding options—bottom suction feeder or deep pile Komfi feed head. It is available with a fixed table, jogging table, or built-in stacker for unloading.
Royal Sovereign provides the Paramount 65X pneumatic laminator with heat assist functionality. With a run length up to 200 feet, it handles sheets up to 65 inches wide with speeds of 28 fpm. The Paramount 65X offers pneumatic pressurized rollers for trouble-free lamination. Safety features include a photoelectric eye and easily accessible emergency stops. It is available for $13,860. “This is the first pneumatic laminator placed into the market that has a price point aimed toward your sign shop owner,” comments Hoffman.
SAS Sustainable Technology Inc. offers the Tecnomac Easy 3, a dry thermal double-sided lamination system. It handles materials up to 20.5×35 inches with a maximum speed of 98 fpm. The Tecnomac Easy 3 laminates run lengths from ten to 5,000. According to Vintila, it features an automatic feeder, electronic overlap control, pressure roll with pneumatic movement, film trimming device, de-curling device, automatic sheet separator, and a big diameter calendar with electrical heating that is sensor thermos-regulated. It is available for $55,000.
Released in 2013, the Spiral Binding RSH-1651 wide format laminator uses thermal and pressure-sensitive films. With the ability to run up to a 500-foot film roll, it handles products up to 65 inches wide. The RSH-1651 operates up to 9.8 fpm with thermal film and 13.1 fpm with PSA film. “It has the ability to handle all types of laminating applications with the ability to run both thermal and pressure-sensitive laminate as well as do board mounting applications,” shares Bondonna. The RSH-1651 is available for $12,000.
Sunfung Technology’s Hydraulic Laminator is a hot roll laminator that allows single-side polypropylene roll film lamination and encapsulation. It features a maximum 690 mm width and operates up to 12 meters per minute. It offers a heavy-duty design, steel roller heating, automatic hydraulic press, and overlap feeding and automatic separations. Sunfung roll laminators include anti-curling technology—in sync with the control panel—to ensure laminated products are produced flat with no curl or uplift. Zhou says the SF 520Z model is available for $8,950 and the SF 720Z for $11,950.
Versatile Finishing
From business cards and ID badges to outdoor signage and wall graphics, lamination protects and enhances digitally printed output. Laminators are available in a variety of sizes for both narrow and wide format applications with inkjet or toner technology. Before selecting a device, consider if the digital printing technology and applications are compatible with the laminator to ensure success.
May2019, DPS Magazine