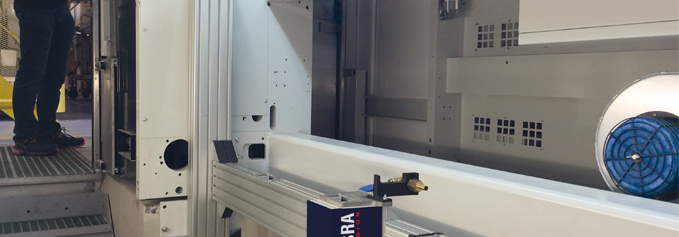
By Cassandra Balentine
Part 2 of 2
Verification and inspection systems ensure consistency and accuracy across the print production lifecycle or within a manufacturing setting. These systems automate manual processes that become insufficient in high-volume, digital and hybrid printing environments.
Part one of this series looks at the evolving demands and advanced benefits inspection and verification systems bring to the market today. Here we highlight several examples of these systems.
System Highlights
Baldwin Vision Systems offers several print inspection/verification systems, including PQV, GV, Defender and Web Viewer. Businesses it targets include printing press OEMs—like Comexi, Gallus, Mark Andy, PCMC, SOMA, and Uteco; as well as larger print groups such as Amcor, International Paper, Tetra Pak, and Westrock.
The company’s focus on OEMs sets it apart from competing systems. “These OEMs are leading the technology drive within the industry. They offer high-value, high-performance solutions to printers that inherently need products that Baldwin offers to enhance their offering,” notes John Cusack, business development, Baldwin.
He adds that large print groups share similar dynamics to the OEMs. “These larger print groups all have corporate driven strategies. These corporate entities typically have technology divisions whose role it is to find and leverage value-adding technologies to their groups. They are therefore typically proactive in their engagement with us or at the very least fully understand the topic and don’t need to be convinced of the value. Finally, their scale makes then ideal candidates to implement our workflows.”
Together with Landa Nanography, EyeC is currently working on an inspection systems for sheetfed digital presses.
According to Benedict Fiedler, product manager and Nico Hagemann, product management director, ProofRunner Sheetfed, EyeC, the new inspection system, EyeC Sheetfed, evaluates high-resolution images of the Landa AQM system in full sheet width without limitations in inspection accuracy even at full press speed. In addition to the 100 percent percent inline print inspection against the prepress data. The new solution will also provide seamless documentation and control of variable data such as barcodes and OCR.
EyeC Sheetfed is fully integrated into the printing process with no additional work for the press operator. In the event of deviations, the operator is alerted for immediate rectification. “The inspection system enables printers to provide complete proof of the high print quality of the Landa Nanography digital press and increase their customers’ confidence in the new technology,” say Fiedler and Hagemann.
The main target markets are pharmaceutical and high-quality packaging printers that produce small- to medium-sized batches for their customers on short notice and with high flexibility. “However, this type of print image inspection has now also become an essential component in commercial printing for optimizing and automating internal processes to increase productivity and customer satisfaction,” they note.
ISRA VISION GmbH’s flagship inspection system is dedicated for pre-print on HP PageWide presses. It considers the new possibilities in this digital printing technology like inspecting defects on big boxes—like five meters long in open layout, and is able to properly inspect different repeat length on the same material.
Code reading can be applied to identify sheets/boards on the material or read out content of code if customized. “Of course, interfaces into the digital print workflow are a crucial precondition we have developed for this. Furthermore, our inspection system can be complemented with our viewer system ViewSTAR and our inline absolute color measurement system ColorSTAR,” offers Lucia Dauer, product manager, print inspection, ISRA VISION GmbH.
Standard Finishing Systems offers two leading inspection solutions—Hunkeler’s WI8 Web Inspection System and a barcode verification system for Horizon products.
Hunkeler’s WI8 Inspection System uses compact image sensors (CIS) to provide precise image monitoring of both sides of the paper web during production and quality assurance. The system checks each individual page during production to detect errors in real time, including color variation in pictures and logos, incorrect page content, distortions in printed images, errors in text, and jet-outs. The compact WI8 was designed for simple, space-efficient installation in printing and finishing systems. CIS sensors can be easily installed in inkjet presses and Hunkeler devices, and the sensors require no adjustment or mechanical calibration. The WI8 System can be integrated with Hunkeler’s CS8 Cutter, DP8 Dynamic Perforator, and WM8 Web Merger. Hunkeler also recently added Intelligent Print Inspection (IPI) to the WI8. IPI will compare the ripped data going to the printheads with the actual printed image. This means that a golden template is no longer required. IPI is ideally suited for full page comparison of every single printed page, of highly variable information such as books or direct mail.
Horizon’s barcode verification system can be deployed across a range of Horizon finishing solutions including perfect binding, bookletmaking, and saddlestitching. It provides tracking, end-to-end system control, and production reporting. This system can be used to complete the required audit trail of package assembly for the production of documents with personal and sensitive information, but it can also be used with non-sensitive pieces for automated, full-time assembly inspection. It virtually eliminates common errors caused by improper loading of stock, book blocks, covers, and intermingled jobs and sets.
Teledyne DALSA’s Piranha4 line scan camera is a global leader for print inspection, due to its excellent color performance and price/value.
Dale Deering, director, market development, Teledyne DALSA, says the soon-to-be-released Linea2 RGB/NIR camera is also targeted for print applications, adding NIR as an independent channel for security features like polymers and foils.
Teledyne DALSA covers a wide range of applications and requirements.
Scalability Score
The scalability of an investment is a major consideration.
According to Cusack, Baldwin does offer scalability.
Individually, a given inspection system can be enhanced either through hardware or software upgrades. Sometimes a user needs higher resolution, which he explains would be a different camera, due to a new contract with higher inspection requirements or a new software functionality to measure the position of a digitally printed code where a dimensional measurement software feature can be enabled.
“The inspection system is part of a defect tracking workflow. We have defect databases but we also have tracking systems downstream that access the data in the database in order to locate defects in the finishing processes so they can be removed and not shipped to brand owners,” shares Cusack.
EyeC provides all-in-one systems that Fiedler and Hagemann say don’t need to scale in hardware, but can scale in software functionality. “Of course, a scale of mechanical width is necessary to fulfill customer requirements— nevertheless, the functionality is always identical.”
ISRA VISION GmbH’s CartonSTAR for digital systems is “absolutely” scalable. “We have implemented CartonSTAR both in corrugated board post-print presses as well into the big HP PageWide digital presses,” notes Dauer.
Potdar says inspection systems such as the Hunkeler WI8 are scalable to fit specific customer needs. “These systems provide ‘pick and choose’ software packages so that the customer will only pay for the software package/functionality that they need for their shop. The inspection system can be extended from a basic visual inspection system to a fully automated tracking solution,” she offers.
For example, if the customer is only looking to check for jet-out/ink-related errors, they can choose a software package that supports only this functionality. If the customer needs a fully automated system that, for example, will detect an error and automatically divert the errored sheet on the finishing line, they can go for a fully automated version. “Verification systems for finishing lines from Horizon also offer scalability in such a way that the customer can choose a version depending upon need,” adds Yashashree Potdar, workflow solutions analyst, Standard Finishing Systems.
Improving Processes
Verification and inspection systems are implemented in many areas throughout the print production workflow in both print and manufacturing environments, catching errors and inconsistencies before they escalate into a bigger issue.
Read part one of this series, Inspect and Verify.
May2022, DPS Magazine