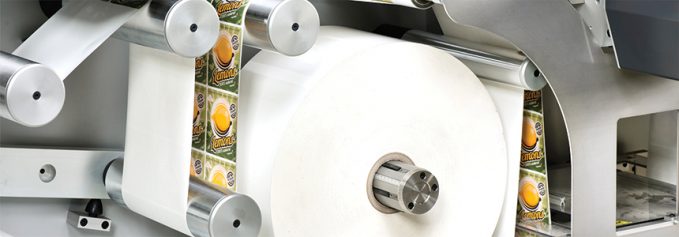
By Cassandra Balentine
Times are changing. Increased demand for customization and reduced warehouse requirements, along with growing environmental concerns make digital print an attractive technology for many brand owners. While digital print still represents a small portion of the overall label industry, it is growing.
With traditional label production technologies, like flexography, conversion is typically performed inline using a range of finishing steps from die cutting and slitting to waste removal and rewinding. As label printers and converters add digital printing capabilities, these functions remain critical, but the process may need to be adapted.
Above: AstroNova’s TrojanLabel T5 is a professional label press and finishing system featuring UV flexographic varnish capabilities.
Evolving Demands
The label converting process covers a variety of post-processing functions, including but not limited to lamination, die cutting, slitting, waste removal, foil stamping, embossing, spot varnishing, and sheeting.
“In general, the major steps are printing—including prepress, and finishing. However, we can break printing down into the types of print, including traditional—for example, flexographic or offset; digital; or a hybrid combination of both,” shares Steve Leibin, president, Matik, Inc. Then comes finishing, which offers options like hot foil stamping, lamination, laser and die cutting, slitting, and semi-turret rewinding.”
Donna Covannon, director of marketing North America, Xeikon, a division of Flint Group, points out that whether the customer’s application is industrial, commercial, or promotional; whether they are producing labels, flexible packaging, books, folding cartons, or wall decorations; auxiliary converting equipment is used to create almost any product.
Mohit Bhushan, director of product management, AstroNova, says basic functions of the modern converting processes include lamination, die cutting, slitting, and matrix or waste removal. An unwinder and rewinder support a roll-to-roll process. Optional functions include foil stamping, varnishing, corona treatments, and other embellishments.
“Printing and finishing all in line has become an enticing new feature available to the digital workflow,” shares Shaan Patel, business development, Arow Systems, Inc. “Producers can now take advantage of the benefits of the inline workflow that flexography offers, but with the cost savings benefits of a short web path, fast set up, limited to no tooling, and the elimination of dies and plates that have burdened flexographic operations for decades.”
James Barnes, sales and marketing, Focus Label Machinery, sees a trend towards enhancements/embellishments, as this is where companies add value and profit as the runs get shorter. He says cold foiling and lamination remains popular.
Christin Park, sales marketing manager, Valloy Incorporation, notes that the latest digital label die cutters are designed as all-in-one finishers and feature lamination, die cutting, matrix removal, slitting, rewinding, and sheeting. Spot varnishing and foiling are digitalized using a UV inkjet print engine. This also enables a semi three-dimensional texture for an embossing effect.
True digital finishing enables label printers to proceed from a PDF file to ready-to-ship, finished, and counted rolls. “It eliminates steps such as creating separate die files and reducing die delivery and die station set-ups, which can take more time than the actual production of the labels,” adds Leibin.
Digital Trends
While the printing process may differ, there are only a few considerations for converting digitally printed labels versus traditional processes.
“Modern label converting is demanding flexibility for the label printers and converters in any possible way. If adding digital capabilities to a conventional press or conventional to a digital press, it doesn’t matter to us. The most relevant thing is to meet the customer’s demand and to give them the highest flexibility possible,” explains Thomas Schweizer, head of product management, Gallus, a member of the Heidelberg Group.
Angie Ostler, VP of finance and marketing, KTI, a Quantum Design product line, agrees, noting that the structure of the label is the same no matter what type of process is running it. “Both need to continue to be innovative while remaining competitive. Manufacturers and their equipment follow suit. Automation of production lines are key to success, including inline converting equipment to keep the lines running continuously with reduced waste,” she comments.
The increase in digital print affects workflow, which Aylwin Spendlow, director of U.S. office, AB Graphics International Ltd. (ABG), says is adapting to include more automation and overall sophistication.
Leibin says digitally printed pieces tend to have a better converting workflow, since traditional finishing is online and digital finishing is offline.
“The customer demands in digital labels regarding quality are the same as for conventionally produced labels. But a digitally printed label has to transport even more, such as individualization and versioning,” explains Schweizer.
Due to changing consumer preferences, job sizes are increasingly smaller. “The design of product decorations is driven by local adaptations—for example languages, legal declarations, temporary promotions for targeted product campaigns, print security, and intelligence elements—such as IDs, RFiD, and other individualized solutions,” adds Schweizer. “In this regard a hybrid production system is suitable for a label printer and converter because it combines the benefits from both worlds.”
Continued Development
Consumer trends lead to higher demand for just-in-time or on demand printing. This means label converters are tasked with producing more complex jobs with little turnaround time. To remain profitable it modern converters need to stand apart from the competition with high-quality print and embellishments and maintain sophisticated and easy-to-use workflows.
“There’s one quick, seven-second opportunity to get the ‘wow,’ catching the eye of the customer,” admits Leibin. Tools like hot and cold foil and laser cutting help achieve this effect.
Label converting is facing some of the same trends as the printing industry. The introduction of new technologies—laser cutting and digital finishing—drive product evolution. “Decreasing run lengths in label printing drive moves toward flexibility and compactness as essential features. We expect to see more mergers and acquisitions in the market as good financial health will be a critical factor in making investments for the future,” offers Bhushan.
Barnes sees the trend for more complex labels continuing, and new technologies will accelerate to be incorporated within labeling.
“The converting market will continue to shift to digital as the technology becomes more affordable, both in capital cost and production costs. High-speed inkjet is specifically going to displace older printing technologies and the current advancements in laser finishing will become more viable for traditional converters,” shares Patel.
The increase in digital means that it is harder to differentiate on print quality alone, “therefore 2020 will see the continued drive towards the use of finishing as the quality differentiator,” says Spendlow.
Covannon agrees, commenting that added-value opportunities of customized embellishment and quality driven by the fast moving and ever-evolving consumer hunger for differentiation and a unique product will continue to accelerate the need for a diversity of innovative finishing and converting options. “There are no visible signs of any slowdown in the demand for creative, clever, and unique products that stir consumer interest and appeal both online and on the shelf,” shares Covannon.
Park believes that label converting machines must be digitized in order to reflect diversified customer needs. This is especially true for small printing companies that run short quantity, batch production. “These companies typically don’t have enough space to install big and huge machines; therefore label converting machines need to be more compact.”
A streamlined, digital workflow is also increasingly important. Leibin sees heightened use of web portals that thrive on a complete digital workflow that allow jobs to get on press the same day. “If a company does not have a digital finishing system, for customized labels they must rely on mag dies. That’s costly—usually $150 to $200, and there is a one to two day wait to have them delivered. Then, there are unseen costs. If it takes five to ten minutes to make the die change, and new jobs are undertaken 20 times during a shift—that adds up very quickly. With a digital finishing system, if you print today, you can also laser cut today. Digital finishing completes the digital workflow and improves profitability.”
It is also important that modern systems be easy to use and incorporate automation. “Digital printers are well automated by JDF workflow for web to print environments. Digital finishers need to be automated for a web to finish in combination. For this purpose, all finishing functions need to be recorded as a job ticket and every job needs to be automatically converted for different effects,” shares Park.
Spendlow comments that on account of increased workflow and automation, we see an increase in short runs in digital printing. Flexography remains a core part of the industry, but is moving towards more automation.
The most important consideration, given that there are always going to be long and short runs, is that converters need two different workflows, says Leibin—an analog/flexographic printing workflow and a digital workflow. While many label converters have digital presses, they are still operating traditional cutters with mag dies. The digital workflow has not been completed,” he adds.
“The label market is a growing one but, for sure, label printers and converters are facing several challenges in today’s narrow web production,” admits Schweizer. “In general, two aspects will be predominantly visible in the print shops of the future—on the one hand the machine equipment as an enabling platform and on the other hand the data cloud as an intelligent framework for connecting the diverse interfaces.”
He points out that overarching the already mentioned trends, the aspect of sustainability is gaining momentum and will dominate the matter of product decoration in the future. “The reduction of waste in daily operations and the durability and recyclability of our machine equipment has always been a crucial decision element for our product design under the umbrella of investment security from an ecological and economical sustainability. However, the fast changing market requirements and legal regulations will culminate in the future and encompass basically all elements of label printing such as substrates, curing systems, waste figures, and production choices, among others. This holistic view will impact all actors in the packaging supply and value chain—consumers, brand owners, printing houses, and suppliers of equipment and consumable,” states Schweizer.
The market is always changing and there is a push for digital. Ostler expects declining run lengths as companies demand smaller quantities and more personalization to appeal to different customer groups.
Taking Care of Digital
Existing and new converting machines support traditional flexographic processes as well as hybrid and digital environments.
ABG offers a range of label converting equipment well suited for digital print environments. One solution is the RTS Sheeter, which is equipped with an electromagnetically braked unwind air expanding unwind mandrel, splice table with interlocked web clamps, servo-driven in-feed nip roller, guillotine cutting mechanism, and 39-inch long shingle delivery table with an accelerator/jog function for batch separation. The machine is controlled via a six-inch color TFT touchscreen HMI with multilingual operating instructions. Optional equipment includes alternative unwind mandrel diameters, razor and slitting units with five knife sets, venturi trim extraction, and a fully programmable inter-sheet waste trim function.
Additionally, the ABG Converter is available in 330, 430, 530, and 670 millimeters (mm). “We are seeing additional capacity for packaging applications. The increase in the need for e-commerce labels is also driving demand for wider converters,” shares Spendlow.
AstroNova, Inc. recently launched the TrojanLabel T5, a larger version of the company’s TrojanLabel T4, a professional label press and finishing system with the addition of UV flexographic varnish capabilities.
The T5 is an all-in-one digital print and finish inline labeling solution. It is built around AstroNova’s TrojanLabel T3 Digital Inkjet Label Press platform with a smart, compact converter unit featuring UV flexographic varnish, lamination, rotary die cutting, slitting, and waste removal. Following the introduction of the T4 two years ago, the T5 is the company’s latest high-production label printing and converting solution for the professional printing market. The T5 adds several additional embellishments with spot and super-gloss varnish, lamination, slit and rewind, and cold foil application for silver, gold, and metallic decorative accents—all in a single platform.
Focus Label offers a range of rewind/die cutting machines. The Servo controlled solution features a re-register system. Last year, Focus Label added an option for semi rotary, which he finds increased interest in.
Gallus offers a portfolio of digital and conventional presses including the cost-efficient conventional press Gallus Labelmaster; the hybrid Gallus Labelfire; or the conventional label press Gallus RCS 430.
The Gallus Labelfire combines the flexibility and versatility of digital printing and the reliability and precision of hybrid technology, with a production speed of up to 70 meters per minute. With the optionally available integrated Digital Embellishment Unit this digital production system includes a range of label printing and embellishing possibilities.
The Gallus Digital Printbar was first shown in 2019. It is an inkjet printing unit designed specifically for digital insetting of highly opaque, digital white. With a printing width of 17 inches, the new, shiftable Digital Printbar benefits from inkjet-based digital print technology and can be integrated into all modular Gallus machine systems. The movable print unit will be launched on the secondary level of the narrow web press in 2020.
KTI’s products include automatic butt splicers, matrix rewinders, and turret rewinders designed to improve efficiency on new and existing process lines. All of KTI’s equipment helps increase production throughput by eliminating the need to stop for roll changes.
KTI recently released the newest generation of the popular MTR Series Turret Rewinder. The latest generation turret rewinder is ideal for running pressure-sensitive paper label stock. The MTR rewinder offers a new roll closure system with inline print-and-apply technology, which enables customers to add various product and production information to the roll closure labels. This may include information such as product codes, lot numbers, job numbers, and date of production. These labels are automatically printed and applied to the finished rolls before they are removed from the machine. Features of the print and apply include digital inkjet printing technology with industrial, large capacity ink cartridges; prints alpha-numeric text strings up to 15 characters long as well as one and two dimensional barcodes; printing height to half an inch; resolutions up to 600×600 dpi; and True Type fonts and Unicode character support.
In addition to the print and apply, the turret rewinder has optional automatic core loading, which automatically loads cores onto the machine eliminating the need for an operator to load it. The automatic core loading allows for faster turret cycle times permitting shorter rolls to be run at higher line speeds.
The Matik SEI Labelmaster offers true digital finishing, delivering on-the-fly cutting of a variety of printed jobs—including through cutting, kiss cutting, perforating, micro-perforating, and single-pass engraving. With the Labelmaster digital system, jobs of one to one million are cut without die tooling. This is all done on roll to roll, roll to sheet, and roll to part cutting, producing intricate designs, cutting, and engraving on a variety of substrates at speeds of up to 330 feet per minute with quad lasers.
Valloy Incorporation offers the DUOBLADE SX, a digital roll label die cutter. Using a knife system, it is designed as an all-in-one total label finisher. It is equipped with two cutting heads for faster cutting speed. Park explains that if you assume a job cutting 100×100 square mm, the maximum cutting speed is six meters per minute. The maximum cutting area is 320×400 mm, but for length it can cut by split cut without length limit. Recently, Valloy’s sheeter, CHOPIN 350 was added as an option to use as a roll to sheet machine. With this, customers choose the type flexibly depending on their needs.
Xeikon offers comprehensive and complete digital printing and converting solutions or “Suites” designed and adapted for a diversity of business models. Each Xeikon Suite consists of five components that work together seamlessly as one complete digital solution and this includes the converting functions. The Suites include a Xeikon digital printing press driven by a dedicated front-end workflow that controls the whole production process from start to finish. It comes with appropriate inks or toners and a wide range and selection of substrate availability. The Suite is intelligently designed to include specific and appropriate machinery for inline and offline converting processes for a variety of applications. For example, a laser die cutting unit can come inline with the Xeikon 3030 digital label printing press along with workflow software, print media, dry toners, and pre- and post-converting equipment.
Additionally, Xeikon’s Fusion technology offers converters the flexibility to produce virtually any label on demand. Fusion consists of a series of embellishment modules presenting a digital alternative to hot and cold foiling, screen printed white, tactile varnish, spot print, and braille.
In 2019 Xeikon demonstrated its latest embellishment technology for tactile textured printing as well as new developments for flexible pouch printing, which includes the lamination process—the Xeikon LCoat is designed to have zero after cure time. “Feedback from customers is overwhelming as they see the advantage in this modular approach,” says Covannon.
Label Printing & Converting
Label printing and converting environments rely on a range of finishing tools to meet evolving consumer and brand owner demands. In addition to variability, complex and unique finishing tools as well as a sophisticated, but easy-to-use workflow is required to support a print on demand environment.
Mar2020, DPS Magazine