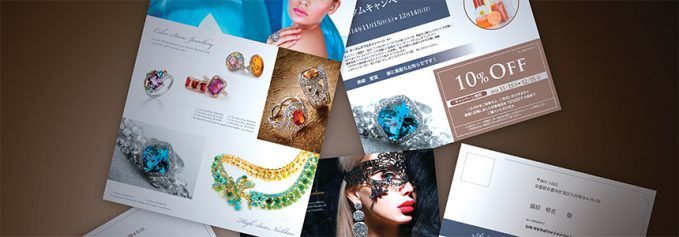
By Cassandra Balentine
Continuous-feed inkjet solutions hit volumes of more than ten million impressions a month. These machines continue to get better, faster, and cheaper to operate. With cultural changes driving demands for shorter, more personalized runs, the technology continuously gains momentum.
Above: Rollem provides slitting, creasing, perforating, and semi-slitting equipment.
Ongoing Evolution
Just recently, output from production inkjet didn’t meet the needs of high-end direct mail, commercial printing, packaging, and décor. “For these markets, there was no balance between volume, value, and velocity and limited print service providers (PSPs) to mostly transactional and book printing,” points out Marybeth Gilbert, VP production inkjet business, Xerox Corporation. Inkjet has evolved to produce higher image quality on a wider range of media, enabling PSPs to move jobs from offset into a more flexible continuous-feed inkjet production process.
Michael Poulin, director of marketing, production print solutions, Canon Solutions America, agrees, noting that continuous-feed inkjet presses have always set the bar high in terms of speed and productivity, but recently it’s transformed into high-quality image and color production devices, thanks to advances in ink sets, media testing, and improved drying mechanisms.
“Five years ago continuous-feed inkjet was primarily limited to publishing and mostly black-only work in that space, transactional print, and some lower end direct mail work. Advancements in printhead technology that improves image quality, drying systems to enable heavier coverages and higher densities, and ink technologies to expand to coated papers all contribute to the successful migration of continuous-feed inkjet into just about every print segment,” explains Mark Schlimme, VP of marketing, Screen Americas.
Mike Herold, director, global marketing, Ricoh USA, Inc., adds that paper transport capabilities make the handling of heavier, lighter, and coated papers simpler and more cost effective for continuous-feed inkjet. Further, improved vision systems provide high-resolution image capture of printed documents as they print. This helps ensure accuracy and empower print providers to more reliably meet tight turnaround requests and avoid costly reprints.
Dan Cavallo, director business development WEBJet, Konica Minolta Business Solutions, U.S.A., Inc., says workflow is another consideration. “Printing is almost anticlimactic. Sure it is a critical component, but designing proper workflow to feed the press really streamlines an operation. Automation is paramount and perfectly rounds out a solution.”
Print volumes and quality have become more demanding and continuous-feed inkjet has come into its own, demonstrating the required performance, shares Sue Cardot, director, worldwide marketing and sales operations, Enterprise Inkjet Systems, Eastman Kodak Company.
Specific Advancements
Industry players introduce advancements to continuous-feed inkjet platforms to remain competitive and attractive to those looking to add or establish the technologies within their production workflow.
In 2018 Canon introduced the Océ ProStream Series to the U.S. market. The Océ ProStream features a floatation drying technology in which the web is kept free floating for optimal image quality, process control, and consistency on a range of media. This press also includes a new engine design with the latest generation piezoelectric drop-on-demand printhead, ColorGrip, and a new polymer pigment ink set.
Building on the successes of previous iterations, Document Data Solutions (DDS)’ third generation iDataPrint FS-1200 inkjet print system is capable of running a broad range of inks including dye, pigment, latex, and UV-curable. It now includes an option for automated cleaning of the printheads. The FS-1200 is equipped with 1,200 dpi printheads and offers speeds of nearly 2,000 feet per minute (fpm).
HP Inc. offers its PageWide industrial presses for high-volume commercial print. The continuous-feed lineup includes the HP PageWide Press T200, T300, and T400 HD series. These machines feature HP’s High-Definition Nozzle Architecture featuring 2,400 nozzle-per-inch native resolution and dupal drop weight for fine image detail.
Kodak Enterprise Inkjet Systems Division manages a balanced portfolio enabling reach into new market applications including its PROSPER Presses and Imprinting Systems, which focus on commercial print, direct mail, publishing, and packaging. Introduced in February, the PROSPER Plus Imprinting Solution is the newest KODAK Stream Inkjet Technology component product line, developed based on KODAK PROSPER S-Series Imprinting Systems. The four hardware products include two narrow formats and two wider format models that print at speeds of up to 850 or 2,000 fpm, maximum.
In addition, Kodak ULTRASTREAM is the next-generation, continuous-feed inkjet technology that enables expansion into packaging and labels, magazines/catalogs, and décor.
Konica Minolta partners with Superweb Digital and Memjet to become the exclusive reseller of WEBJet solutions in Canada, Mexico, and the U.S. Superweb Digital manufactures print lines from end to end with a variety of inline post-print options such as perforating, hole punching, offset stacking, letter folding, and camera inspection systems. Konica Minolta offers a resolution of 1,600×1,375 dpi using a drop size of 1.2 picoliters with its continuous-feed inkjet solutions to provide excellent definition in graphics as well as small print. The press comes configured at three speeds and three resolutions to accommodate a variety of applications and requirements for color and achieving service level agreements.
Ricoh offers new radial-assisted dryer technology in the RICOH Pro VC70000, which is designed to increase ink limits. “Customers using this technology can run applications with ink limits as high as 210 percent at speeds that were unimaginable just a few months ago,” shares Herold. This dryer—and the accompanying inks—also eliminate the need for priming.
The company also developed ink sets that expand color gamut and substrate versatility, driving savings of up to 40 percent for production of in-demand applications, such as retail circulars on gloss-coated stocks, according to Herold.
Screen made several important technological advancements in continuous-feed inkjet across all platforms. Its Truepress SC Inks are pigment inks designed to print to standard coated offset stocks without pretreatment or primers. “These inks also provide superior adhesion to coated stocks while providing a thinner ink film and opacity to the ink so that a paper’s unique characteristics could still contribute to the look and feel of higher-end print, thereby enabling designers to design for inkjet just as they would for offset,” adds Schlimme.
Screen collaborates with Adphos on NIR Drying technologies that create flat book blocks and sheeted pieces without the curl and warp inherent with high-energy, heat-intensive drum drying.
Gilbert says Xerox provides the ability for its clients to choose an inkjet solution that best fits their workflow, floor space, application mix, price point, and growth strategy. This commitment to accessibility has driven a number of advancements in its portfolio including Xerox High Fusion Ink and advancements in high-density ink. “As we continue to push inkjet toward higher image quality standards, we have developed technologies to achieve optimal color-to-color registration. This means advancements to paper path stability as well as print quality monitoring with missing jet detection and compensation.”
Driving Adoption
The commonly known advantages of digital are the same characteristics bringing new business to continuous-feed inkjet technologies. However, it’s happening at a larger scale.
“The market factors driving inkjet adoption are the same as what has always driven digital print adoption and conversion just at much greater scale because of the speeds achievable by inkjet and the ever-improving image quality—shorter run lengths, faster turn times, SKU proliferation, personalization, regional customization, shorter time-to-market development, and the need for late stage changes and corrections,” says Schlimme.
Poulin says continuous-feed inkjet is one of the most economical and productive forms of printing. “With recent advancements, print providers no longer have to sacrifice color or quality for productivity, they can achieve it all with continuous-feed inkjet,” he offers.
Companies are looking to optimize costs and get more out of their existing operations. “For commercial printers, color at higher degrees of productivity and lower variable costs makes color printing a viable investment. For in-plant printing, inkjet allows printers to diversify product offerings, use color more effectively, and drive value for the company. It allows for operational efficiency—consolidating redundancies and finding growth without needing more space or employees,” says Gilbert.
Continuous-feed inkjet provides many key advantages over other platforms such as higher reliability, less demand on operators’ time, reduced energy consumption, lower costs, scalable upgrades, and fast turnaround times. “Simply put, inkjet’s been poised to be a powerhouse for decades, and with recent additional enhancements—like ink formulations and enhanced drying—the segment is really coming into its own, expanding far beyond its roots in the transactional space to also include book printers, direct mailers, and now commercial printers in the graphic arts space,” says Herold.
Bill Papp, product manager, DDS, points out that customers demand variable data as well as short-run capabilities from PSPs. The challenge becomes how to offer these services and maintain or even improve profitability. For some, the answer may be a hybrid print solution. “Adding high-speed, high-quality inkjet print modules to existing offset presses not only allows static information to continue to be printed with offset, but existing post-processing equipment can be repurposed for new applications. The result is a highly cost-effective inkjet print system providing the utmost flexibility while retaining all of the unique capabilities of offset,” he shares.
Addressing Challenges
Technical and cultural challenges still hold some back from taking the chance on continuous-feed inkjet. Gilbert says businesses are hesitant to invest in a technology that they believe may not serve them well in the future.
Poulin admits that there is still a learning curve associated with production inkjet, both sheetfed and continuous feed. Applications need to be designed differently and printers need to learn the optimal balance of ink levels and select the right profiles.
Ten years ago, the biggest barriers to inkjet adoption were technical—image quality and media versatility. Today, with the rise of new printhead, ink, and dryer technologies, those problems are all but eliminated. Herold says the challenge of today is in getting the word out to end users that this isn’t their father’s inkjet. “Modern inkjet can go pound-for-pound with offset in terms of image quality and color gamut, so now vendors and PSPs are looking to get the word out,” he shares.
Cavallo agrees, stating that there must be education at the creative or agency level so designers understand the capabilities of these presses in terms of data and graphics and how to use them effectively.
Those who have implemented continuous feed platforms have done so as the model fits their operations. “As continuous-feed inkjet presses creep into traditional offset shops, these companies have to think more about variable information and graphics on a page-to-page basis to take advantage of these solutions. For large static runs, an offset press is still king,” he adds.
Schlimme says the paper market might be the biggest hurdle to larger scale inkjet adoption. “The full printing market—across all technology platforms—is down even as inkjet grows. This market shift means the paper mills are shifting mills and lines to other paper markets that are seeing growth—corrugated and packaging for example. But this is lowering capacity for the print market and keeping paper prices high. When so many inkjet platforms require additional treatment for ink adhesion, these increased costs can drive marketers and buyers away from inkjet and back to offset print. The ability to print to standard coated offset stocks greatly improves a printer’s position with continuous feed inkjet.”
Another big challenge of inkjet, compared to offset, is running costs. Papp admits that it is costly to produce high-quality, heavy coverage pages with inkjet alone. Increased operating cost—ink, printheads, service agreements, and click charges—can make inkjet cost prohibitive. He explains that companies are purchasing offline or near-line finishing equipment being fed by multiple inkjet presses. “Finishing lines can cost nearly as much as the inkjet press and dramatically increase the challenge of getting the complete system running,” he offers.
Continuous Needs
As print volumes come down and complexity ramps up, more jobs that once only make sense for offset production are now contenders for digital print. This is especially true as the speed and quality of continuous-feed inkjet steadily improves. While more industry education is needed, inkjet expands into new markets like commercial print, packaging, and décor.
“Inkjet’s recent surge in image quality, color quality, and throughput introduced or expanded its presence into several markets,” offers Herold. These advancements mean campaigns for luxury goods and experiences produced on inkjet can finally capture the beauty of a cruise or the sheen of a new sports car. Increased substrate versatility and the added punch of variable data make it an attractive solution for a range of applications. dps
Sep2019, DPS Magazine