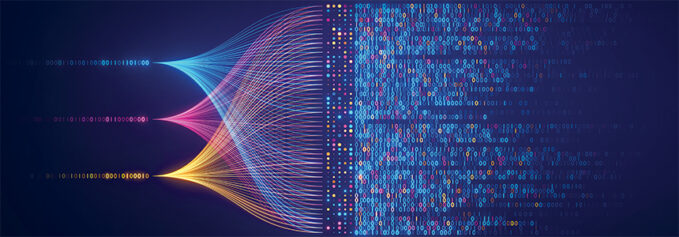
by Cassandra Balentine
Print management information systems (MIS) continue to evolve beyond the traditional intuition, moving into enterprise resource planning (ERP) territory. Because digital print encourages more frequent, highly complex, shorter run work, it is imperative that print providers have the right tools on hand to remain effective and efficient. Modern print and service providers offer this.
Certain tools and functions enable more power to managers and operators alike, making for a productive shop floor no matter the application. From ease of use to accessibility and reporting, modern MIS solutions offer value to the production workflow.
Accessibility Considerations
Accessibility is a key consideration in an increasingly mobile world.
Mark Alioto, CEO, Revshop, points out that this is because users need to be able to get system access wherever they might be. “We live in a new hybrid on/offsite working environment,” he asserts.
“Accessibility is vital, which is why most software is now cloud based. This allows for access anywhere in the world,” seconds David Graves, CEO, Aleyant.
“We have some organizations where the majority of users are remote. Having an easy way to manage teammates and federate authentication play a big role in making an MIS simple to administer,” says Adam Homsi, founder, InkCloud.
Matt Prusa, senior director, software sales, Avanti Slingshot, RICOH Graphic Communications, also feels that modern software should be browser-based, allowing secure access from multiple and remote locations. “Owners and leaders need access to information 24/7, and CSRs and salespeople often receive inquiries outside of business hours.”
“In our experience, providing a cloud-based solution that does not require an additional client installation but rather a browser accessible platform greatly increases the usability and efficiency of a platform,” suggests Craig Powell, GM, North America, printIQ.
Depending on the functionality, Jef Stoffels, head of marketing, Dataline, believes remote log-on functions are a useful addition to MIS software, including CRM, dashboards and reports, basic calculation, and estimation features that can be accessed by a salesman or management while out of the office/on the road. “Logistics and installation—signage—can be connected remotely to the MIS as a natural extension of the production project. When an installation is completed successfully, the customer signs off and installation pictures are added to the project so post calculation and invoicing can be triggered after that.”
The main drivers for investing in remote services include reducing machinery downtime, optimizing performance, and speeding up support. “As we continue to navigate the hybrid model of remote and in-person services, we believe that the print industry is undergoing significant transformation. Embracing technological advancements like remote services not only enhances efficiency and reduces costs but also prepares the industry for future challenges,” says Alfonso A. Hernandez, Jr., VP of sales, HiFlow Solutions.
Intuitive Interfaces
We’re in a technology era. User interfaces are expected to be easy to navigate and understand. This is essential to an MIS, especially as a changing labor force is a top challenge for the foreseeable future.
Some production facilities struggle with high turnover rates. “A system that does not have a high entry barrier is critical in such cases. At the same time, management expects true and reliable data that will be visible in the system in real time. This is crucial for making data-driven decisions and closely monitoring the company’s margins,” offers Hernandez.
Alioto sees intuitive user interfaces (UI) as a mission-critical element of any print MIS platform.
“An intuitive and easy-to-use interface is a must-have today. High entry points with difficult interfaces are simply not acceptable. Considering the current challenges in acquiring a workforce, adding another hurdle with complicated software is a clear mistake,” asserts Hernandez.
Graves feels there are always detractors within any organization. An easy-to-use interface allows users to overcome some of the detractors.
Helle Vogt Mikkelsen, head of marketing and strategic partnerships, PrintVis, feels that an intuitive UI reduces the learning time for new users, enabling them to become proficient quickly. “An intuitive UI can guide users through complex workflows, ensuring that all necessary steps are followed correctly—for example in estimating. Satisfied users are more likely to embrace the system and utilize its full range of features.”
“An implementation project to get the MIS built is already a lot of hard work and the last thing you want to see after all that effort is slow acceptance from shop floor staff because the system is hard to navigate,” comments Powell.
“While an intuitive UI is consequential, the MIS must address intricate job requirements and handle varying complexity across multiple job functions—eg. customer service operators (CSR), estimating, production floor operators, and finance,” asserts Prusa. “When evaluating MIS vendors, it’s important that they demonstrate capabilities to properly address each user’s unique role requirements.”
At the end of the day, the UI of every software needs to enable the user to work fast and easy. “As there are different levels of users for print MIS software, the experience will be different,” suggests Stoffels.
With this in mind, Stoffels says MIS should include expert sections of the software needed to offer all the information in one the place; manager levels can use a limited set of functions to get the information they need; and operators on the shop floor need limited functionality that allows them to use and feed the information they are required to.
Hernandez believes that layouts and views that are self explanatory and intuitive are essential to meet the modern challenges the industry is facing. “When an MIS has an interface that most users already know, like the Microsoft interface, it makes initial onboarding very easy.”
When evaluating print MIS options, Homsi recommends looking at your most common workflows. “Ask yourself what actions are done most by your team and ensure the MIS makes this easy for your organization’s users. Not only are these actions done over and over again but having a good user experience also translates into less upfront training.”
Reporting and Analytics
In a data-driven world, what is measured is managed. It is important to consider analytic functions when looking into an MIS.
Todays’ reporting and analytics functions use real-time data for everything going on in the print company, which provides the ability to feed all users with the information needed at any given moment.
A modern print company should be driven by clear data. “Only in this way they can be assured the business processes are running as they should,” says Stoffels.
Hernandez feels that analytics is what an MIS does best, and it does it across departments—production analytics provide insights into the efficiency and performance of the production process. Warehouse analytics provide information on inventory levels, turnover rates, and supply chain performance. Reports on sales trends, customer order patterns, and profitability by customer segment can inform marketing strategies and customer relationship management efforts. “Modern print MIS solutions provide analytics on quality control measures, including defect rates, rework rates, and inspection results.”
Reporting is a rapidly changing aspect of MIS. “As data becomes more easily accessible to decision makers, how it is consumed will evolve as the business grows,” says Prusa. “While standard reporting should meet a business’ base requirements, business intelligence (BI) has the power to customize how data is presented from multiple sources such as MIS, accounting, web to print, and printer device data. Centralized access to real time and historical information will drive accountability, functional visibility, and better business decision-making across the organization.”
BI is essential in the print and packaging industry, enabling companies to collect, analyze, and use data for informed decision making and process improvement, ultimately enhancing efficiency, quality, and profitability, agrees Vogt Mikkelsen.
Powell points out that modern print MIS solutions are increasingly asked to provide advanced reporting and analytics functions to enable data-driven decision making.
When investigating reporting capabilities for an MIS, Graves feels that custom reports are a must.
“We see a lot more complex scenarios where you’re processing jobs from various intake channels, which can include a storefront, the back-end dashboard, API, etc. You’ll want to look to MIS solutions that allow you to segment data by these additional dimensions so that management can understand the analytics,” suggests Homsi.
It is important for the system to provide users with the possibility to generate new reports/dashboards or change existing ones by themselves. “As both the specialized designer, developer, implementer, and the owner of the system, we can address many of our clients’ custom needs. We see that this flexibility is crucial in the current ERP/MIS market,” says Hernandez.
“Self-serve, non-technical user data access is critical,” adds Alioto. He suggests looking for a MIS that is intuitive and has robust dashboards and alerts, which can replace old industry practices of needing to run reports to get reporting and analytic data.
Next-Gen MIS
A data-driven approach to business operations is essential for future success. Print MIS is well adept at gathering, analyzing, and organizing mission-critical information. It is essential that owners and operators are able to leverage this data with intuitive UIs, remote accessibility, as well as complex and custom reporting capacities.
Check out our webinar on this topic.
Sep2024, DPS Magazine