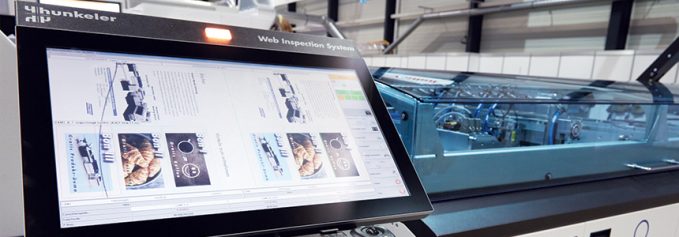
By Cassandra Balentine
Vision and inspection solutions have a range of uses within the production print space, including quality control and data integrity. This is of particular importance as the role of high-speed production inkjet increases.
Above: Standard Hunkeler’s WI8 Inspection System with compact image sensor (CIS) provides precise image monitoring of both sides of the paper web during production and absolute quality assurance.
“Print providers in any industry benefit from integrity solutions, particularly in this era of high-speed production and short-run applications,” says Don Dubuque, director of marketing, Standard Finishing Systems. He suggests it is too time consuming to manually inspect high volumes of commercial publications, direct mail, food packaging, newspapers, pharmaceuticals, transactional mail, tickets, and other applications with large quantities of information. “For some applications, especially applications that rely on sensitive variable data, integrity solutions are essential.”
Applications and Industry
There are several use cases for document integrity systems—including quality control, color management, front to back matching, barcode verification, assembly integrity, form matching, forms verification, and auditing and reporting.
Print verification systems are especially critical in banking and financial services, government entities, and healthcare industries, including insurance and pharmaceutical applications as the integrity of personal information must be upheld. “As federal guidelines for these industries become more stringent, the need for print integrity and security also becomes more urgent,” shares Christine Thomas, VP of sales and marketing, Videk.
Greg Padowitz, director, technical sales support, BÖWE SYSTEC North America Inc., points out that numerous applications across all industry segments—financial, healthcare, insurance, and telecommunications for the processing of statements, policies, checks and credit cards—are often required to uphold requirements set in privacy laws when processing these communications.
The direct mail marketing industry also embraces vision quality control systems. “As that industry moves to higher levels of personalization based on highly stratified demographics, print shops are seeking assurance that the individualized pieces are assembled and printed correctly,” shares Thomas.
Within the mail fulfillment segment, Bow Smith, technical sales support manager, Inserting North America, W+D, says a majority of inspecting systems address one of three primary applications—first the traditional read-and-print applications for direct mail marketing; secondarily, annual healthcare benefit packages; and finally, vote-by-mail applications. “Each of these unique workflows generally require the gathering and matching of multiple personalized inserts or documents that ultimately must be inserted into a single envelope and mailed to the appropriate recipient. One can imagine how sensitive each of these packages are and therefore it is imperative that they are processed with the highest levels of integrity and security to ensure that they only end up in the hands of the addressee.
Anything short of this is unacceptable,” he cautions.
In regards to ballot printing, Thomas says it is an emerging market. “Printers are driven to ensure 100 percent ballot integrity on every ballot printed. Traditional manufacturing methods rely heavily on post-process, human inspections to discover any defects. This is expensive, time consuming, and ineffective,” she states, noting that machine vision systems can detect errors as small as 0.34 millimeter during the press run when running at 100 meters per minute. The increased demand for vote-by-mail ballots in the current environment is also driving the need for automated processes to help produce additional volume with a potentially reduced workforce.
Specific to label printing, inspection systems increase security by performing 100 percent vigilant inspection of all print on every label—including verification of barcodes and braille, according to Ralf Wirtz, sales manager, GmbH Sites, AB Graphics. It also reduces downtime and encourages higher productivity due to faster inspection speeds and offers improved quality through finer inspection resolution detecting subtle defects, often invisible to the human eye—therefore avoiding costly reprints and re-deliveries.
Other markets also embrace vision inspection systems, for example, Thomas sees increased demand for high integrity documenting printing in markets such as book printing, product manuals, and the gaming industry.
Modern vision inspection systems routinely image every page of the web at 600 dpi, while running at full-rated press speeds. “Contact image sensors, higher quality optical elements, and improved performance cameras combined with high-performance processing and complex software algorithms are all integral parts of providing the level of quality inspection needed today,” comments Thomas.
Automated inspection systems provide value at nearly every stage of production for nearly any industry or application. Dubuque explains, at the printer, web inspection systems perform a number of quality checks, including color tolerance, pattern matching, white space verification, ink or toner spills, voids, and jet outs. Integrity systems are also available on almost any type of print-finishing equipment. At the finishing end, verification and integrity software perform sheet and set-level integrity checking during booklet production, for example, or verify the order of signatures in the folding process.
According to Scott Peterson, product marketing manager, Tecnau, integrity solutions enable significant operational savings for all types of print applications. The case for adding these solutions is particularly powerful for print providers operating in heavily regulated industries where there are penalties for either late delivery of communications, or for delivery of documents to the wrong recipient.
Mechanical Evolution
Inspection systems continue to advance to keep up with the latest demands, like increased press speeds.
“Over the past few years, inspection systems have had to evolve to keep up with higher speed presses so that integrity doesn’t come at the cost of production speed,” says Dubuque. For example, inkjet systems can now quickly find defects like nozzle streaks, color issues, and other special defects, reducing waste and overprints. When used effectively, quality assurance systems can also prevent waste by identifying defects earlier in the production process. These systems can identify printing errors in real-time to prevent costly re-work and generate a variety of production reports for compliance.
Thomas points out that printers are now capable of operating at speeds of up to 1,000 feet per minute and resolutions greater than 1,200 dpi, making high-performance imaging and computing a requirement for most systems.
Padowitz says systems process more complex applications, such as the merging of multiple print streams in the case of explanation of benefits with checks or the need for greater levels of personalization in the processing of credit cards and the evolution to printserts where it is important to create a personalized advertisement within the statement creation print stream.
Digital inkjet provides greater composition freedom, requiring robust software solutions for handling high levels of personalization and variability across print jobs. “Companies printing at such high rates of speed require machine vision to minimize waste and maximize asset utilization/throughput,” shares Thomas.
Peterson believes that integrity solutions become even more important in today’s production inkjet environments, as the speed at which the latest inkjet presses operate simultaneously make it harder for an operator to do an eye check, while any issues that do arise in a job run might quickly consume a great deal of print before they’re caught.
Importance of Integrity
Smith says simply put, inspection and verification systems offer print providers a peace of mind, knowing that the mail you processed and shipped was fully verified during the gathering, inserting, and printing processes.
Digital print technologies enable variable data processing, which is a benefit, but also a challenge. Inspection systems help ensure integrity.
“The increased variability made possible by digital print drives the need for inline verification and integrity checking. Inspection and verification systems can be placed on print lines, sheet-feeders, saddlestitchers, perfect binders, paper folders, mail inserters, and more to identify errors in production in real time,” shares Dubuque. “Mistakes can be costly, so job tracking is critical to prevent expensive reprints. Integrity systems can perform verification of material imprinted with virtually any standard symbology, including 1D and 2D code, OCR characters, MICR, addresses, or even OMR markings at the click of a mouse or via touchscreen. Inspection systems are integral in guaranteeing product quality without increasing labor costs,” he explains.
Padowitz feels that by embracing document integrity processing, companies broaden their business base by producing a wider range of applications that meet the appropriate legal requirements and offering customers visibility into the production process. Further, document control software is available to provide insight into the daily production process and the meeting of SLAs with piece-level status for every client.
Thomas says the biggest immediate advantages of implementing a vision integrity solution typically include cost savings from document waste reduction and reduced labor requirements. Operator errors, such as loading the wrong stock, loading the stock in the incorrect orientation, or choosing the wrong printer presets, are inevitable and costly when conducted manually.
The ability to view the print web in real time, combined with automated printer stops when errors are detected, allow issues to be caught early in the printing process. It is critical that errors are found before documents are mailed. Additionally, automated quality inspection tools allow operators to focus on higher level, critical tasks, offers Thomas.
Upstream document preparation and management prior to fulfillment for processing and insertion is a challenge for many. “It is not a matter of if the print room or bindery will have problems during their processes, but a matter of when and how often,” cautions Smith.
Xing-Fei He, senior product manager, Teledyne DALSA, explains that in many cases, the print room has to restart from a given point because of a system failure that interrupted the print process and that process of restarting is not always accurate. “Sometimes documents get printed again that are already generated for mail or maybe missing some documents all together. It is also not a matter of if but when the bindery has personalized inserts that get stacked out of sequence because one went under the other after they were folded and then stacked. The mail fulfillment inserting system is the last stop gap to catch failures and avoid duplicate documents or miss-matched inserts from being mailed out as well as identifying packages that are missing altogether.”
Without document integrity reading solutions working in combination with fully intelligent/inserting platforms, inaccurate mail would be going out undetected. “This is just unacceptable and can be very costly to the company that allows such mail to be sent,” states Smith.
Important Considerations
Inspection systems provide many advantages, but may be complex and costly to implement correctly.
Inspection systems are not one-size-fits-all, stresses Dubuque. They must be properly programmed to meet the specifications and needs of each specific print provider. This may require a lot of setup and integration, particularly for shops new to automated inspection systems. “Transactional and direct mail companies have an advantage due to existing software/compliance infrastructures,” he adds.
Padowitz says many existing, older technologies do not feature document integrity capability. It often requires a capital investment for the acquisition of newer systems. In addition, physical mailing volumes have reduced, requiring companies to invest in fully automated, multiple format systems to gain of all the modern benefits available on one platform.
Paper handling also presents challenges for imaging systems, suggests Thomas. She comments that for many print shops, the additional footprint required for inline solutions can also be an issue.
Document variability presents the biggest challenges to automated inspection systems, especially when the system only inspects predefined regions of data, she continues.
Getting It Right
Document inspection systems are critical for many digitally printed applications to ensure integrity and quality. They are implemented to reduce risk, ensure compliance, aid in customer retention, and automate quality control. dps
Jul2020, DPS Magazine