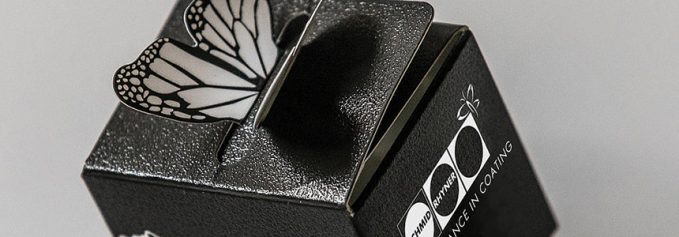
By Cassandra Balentine
Primers, coatings, and over print varnishes (OPVs) are used pre- and post-print for function and haptics. In digital print environments, primers are utilized to optimize substrates for ink or toner while coatings are popular for direct mail, brochures, as well as labels and packaging to add protection or embellishments.
“Coatings and varnishes are popular for two reasons; protection and embellishment,” offers Danielle Wood, marketing specialist, Harris & Bruno. Coating is practical, adding a layer of protection to the print that improves durability and preserves the brand image. It protects print from smudging, scuffing, rubbing, and tearing in downstream finishing, the mailstream, and handling.
Coatings are also an effective way to enhance prints to stand out from the competition. For example, in the last few years, Pedro J. Martínez, CEO, Afford Inks, has noticed an increased interest in tactile/visual effects and aroma encapsulation that complement printed output.
Trends in Coating
Coatings provide protection and embellishment. Specific effects are gaining ground, including low-migration solutions, options that withstand more aggressive cleaning, and offerings with antimicrobal properties.
Steven Barry and Shawn Scheel, technical applications managers, ACTEGA, point out that soft touch, grit, tactile, benzophenone free, and blister coatings are some of the latest trends for digital print in addition to high hold out for porous substrates.
Matt Apke, coatings product manager, Kustom Group, says soft touch is especially popular in the shrink sleeve and flexible packaging market.
Another demand is for coatings that are low migration or approved for indirect food contact, and solutions that can withstand more aggressive cleaning solutions. “We are seeing an increase in requests for coatings to have greater resistance to chemicals, higher rub characteristics, and provide fade resistance,” says Apke.
Martínez points out that COVID-19 has lead to an increase in antimicrobial coatings.
“Antimicrobial is a big one right now, for obvious reasons,” agrees Wood.
Susan E. Bailey Ph.D., business development manager, digital and specialty printing, Michelman, sees press owners doing more with their presses—such as moving into folding carton from commercial. Because of this, new fluids may be needed as well as an understanding of different application requirements. “Digital is allowing for more jobs as well as shorter print jobs. Liquids must be efficiently run, cleaned up, and changed over. Another trend is extra robust durability for aqueous inkjet preprint liner through the corrugation process,” she explains.
Differentiating Characteristics
For production printing, characteristics that differentiate coatings, OPVs, and top coats for digitally printed output include wetting capabilities, dry time, and odor.
Barry and Scheel say excellent flow and wetting capabilities, fast drying, high adhesion, no penetration into unprinted areas, no yellowing, low odor, and good slip, scratch, and rub resistance are important product aspects for coatings in digital printing.
“There are different digital printing systems—mainly toner and inkjet—and varying ink types used in each of these processes. These influence varnishes. One major impact is on the wetting of the varnishes on these systems as regular UV varnishes are not, in general, suitable for digitally printed systems,” shares Martínez.
“Coatings can have many characteristics for the desired output—gloss, satin, or matte finish; receptive to further finishing like stamping, gluing, or imprinting; high rub; low or high slip factors; low odor; and migration; as well as FDA, Nestle, and Swiss compliance,” explains Apke. He says the substrate, ink chemistry, drying capabilities, application method, and handling further differentiate the coatings within the individual characteristics above. “It’s critical to know all of the parameters ahead of time to select the correct coating,” he states.
Coatings, primers, and OPVs play different roles in the digital production environment, but together they provide increased protection of printed material including water, chemical, scratch, and thermal resistance, as well as the prevention of color fading, according to Bailey. “Typically, primers help improve the adhesion to the substrate and print quality. However, it really depends on the substrate and the technology you print with if you utilize coatings, primers, and/or OPVs. For example, if you print with an HP Indigo press, you will utilize primers for improved adhesion. When printing with UV or aqueous inkjet on paper, your technology will need to provide both improved adhesion and print quality. The primer improves hold out, reduces bleed and mottle, and makes colors more vibrant. Aqueous overprint coatings for inkjet offer durability and resistance properties, and opportunities to tailor surface finishes such as gloss, matte, satin, or provide haptic effects.”
Bailey points out that aqueous OPVs designed to interact with multiple layer inkjet print stacks and provide a robust protective layer and low-coat weights for the aqueous inkjet print—allowing them to dry faster, thus increasing production efficiency. They also protect inkjet-printed images on pre-print liner during the corrugation process.
In addition to coatings that enhance aesthetics, Bailey shares that coatings have been developed to provide increased functionality—especially to packaging. “Used in food and other consumer goods packaging—on both plastic film and paper applications—coatings offer gas, mineral oil, and moisture barriers, with options for food contact compliance. Coatings are now developed for the Circular Economy, with opportunities to reduce waste, provide product protection, and use fewer raw materials,” she explains.
Printing Process
Various methods of digital printing include toner/electrophotographic (EP) solutions and UV and aqueous inkjet.
Barry and Scheel say each digital technology has its strengths and weaknesses and the application of the product generally dictates the supporting solution that would be used with each product. Differences between dry and liquid toner/inkjet create the environment where top coat choices become focused on which product provides the best adhesion properties. “In digital printing, coatings and primers fulfill specific requirements. Printing processes and the way of varnishing play an important role. Correlations between substrate, toner/ink, primer and coatings must be carefully considered,” they share.
The digital print process plays a critical role in selecting the proper solution. “The surfactants used in both toner and inkjet typically feature lower surface tension requiring specific solutions,” agrees Apke. He says these solutions are further impacted by the substrate used. “Non-porous, flexible substrates require a more flexible coating than paper. Inkjet papers are typically more absorbent requiring higher viscosity solutions. Some toner-based inks require a primed or treated substrate to achieve good adhesion, which can affect the solution selection.”
EP/Toner
When it comes to EP technology, Bailey says that in her experience, the right solution depends on the substrate, application, and printing equipment. “A primer may or may not be needed based on the substrate and specific printing equipment. Regarding OPVs, it depends on the applications. For example, if you need more scratch resistance, then a coating makes sense.”
Toners used in EP may contain specific oils. “On one hand, these oils are important for the printing process, but on the other hand, they may disturb the development of an even coating film. They accumulate on the printed surface, depending on the toner application amount. Results are improved by means of a lagged varnishing process (offline) or by means of a heat treatment prior to varnishing. If the applied toner amount is very high, effectively a relief structure, the coating shows a rough surface, too,” say Barry and Scheel.
“While digital printing with toner may require an electrical discharge via corona treatment to get proper coating adhesion/laydown, the same coating on inkjet printed media might be just fine without any special equipment,” offers Wood.
In order to find the right primer or coating it is important to consider the overall printing process including consumables applied. “This requires a high expertise for product formulation as well as for the suitable product recommendation. Dry toner is easiest to apply a top coat application, compared to liquid toner due to the differences in the types of fusion oils, waxes, or silicones being used as a vehicle for the inks. These components can potentially create problems with wetting, flow, and adhesion. High-adhesion top coats provide a solution for these issues,” comment Barry and Scheel.
When using UV coatings, they believe there is the possibility of an unrequested matte and gloss development considering unprinted and printed parts of the sheet. “The reason—a different penetration behavior of the substrate printed with toner in contrast to unprinted areas. The solution is coatings with anti-penetration characteristics for a homogenous gloss effect.”
The biggest challenge for both dry and wet toners is overcoming the effects of either the carrier solution with wet or the residual fuser oil with dry. “The surface tension created by both require different wetting properties to achieve proper leveling of the coating and can adversely affect adhesion. Corona treating the inks prior to coating provides simpler solutions for achieving improved lay and adhesion,” explains Apke.
High-Speed Inkjet
For high-speed inkjet printing, primers are necessary to improve the quality. “Because the inks are 95 percent water and production inkjet technology allows for printing up to 500 feet per minute, press owners need to get the water absorbed and/or dried quickly. Primers allow this to happen. Additionally, aqueous overprint coatings or OPVs increase overall resistance and durability.
Water-based inkjet often works with primers or bonding agents. “These products increase a dot-sharp and high-contrast reproduction of the printed image. They also prevent ink absorption into the substrate. However, fluids are often characterized by a low pH-value and do not only react with the inkjet inks (coagulation), but also with the water-based topcoat. The latter loses its gloss and may show a level of grayness. Choose OPVs that have been adapted to the applied primer in order to allow a good gloss development,” recommend Barry and Scheel.
For water-based inkjet, substrates used are typically very absorbent requiring a different solution than energy curable inkjet. However, they are not as challenging to coat as they don’t seem to impact surface tension as greatly, offers Apke.
Bailey says that primers for UV inkjet improve hold out, reduce bleed and mottle, and make colors more vibrant. “Coated offset substrates are ideal for high-speed commercial printing with pigmented water-based inks, including folding cartons and corrugated packaging. UV inkjet is best on coated, uncoated, and direct thermal paper substrates-particularly wine labels.”
When it comes to UV versus water-based inkjet inks, Martínez shares that in general, both UV and water-based inkjet inks can be coated with UV-curable coatings. “However, some UV inks have a very low surface energy, which is difficult to wet. For these cases, we suggest a little bit of undercuring to help with wetting,” he offers.
Additional Considerations
Coatings and primers allow for more substrate options for digital print providers.
“Coatings and primers provide improved functionality and quality, which allow for printing higher end applications. Priming and coating technology allows for higher levels of water, thermal, mechanical, and chemical resistance that enable printers to enter into markets that they would not otherwise be able to,” shares Bailey.
Barry and Scheel point out that the customer’s end use or downstream processing plays a key role in the decision for a specified top coat or primer coating. “Whether talking about packaging, labels, or brochures, the coating of digitally produced printed products affects all printing processes. The more information a coating manufacturer receives, the better and more reliable the coating or primer recommendation. Apart from the coating equipment used, toner/inks, substrate, the intended final product, and the requested finishing effects play a major role,” they comment.
Another consideration is application method.
Primers can be applied offline or inline, and press owners can choose to do the priming themselves. Bailey says typically, printers apply primers inline while paper mills, substrate manufacturers, and converters apply primers offline. Printers with offset presses have a large stock of offset papers. When they purchase digital equipment, they can utilize their offset papers and other substrates because of inline priming access.
In terms of the application method, Martínez says the major limitation is in the customer capabilities. “The most flexible application method is screenprinting, which allows for applying coatings with multiple size particles. However, this process is usually carried offline and is slow. For most applications, roller coating is excellent system—fast and leaving a thin layer, which will make the system economic,” he explains.
Helpful Layers
Primers, coatings, and OPVs have specific roles in the digital printing process. However, these steps can complement each other to provide the ideal canvas for inks or toners, add durability, increase functionality, and embellish for a stand-out effect. dps
Nov2020, DPS Magazine