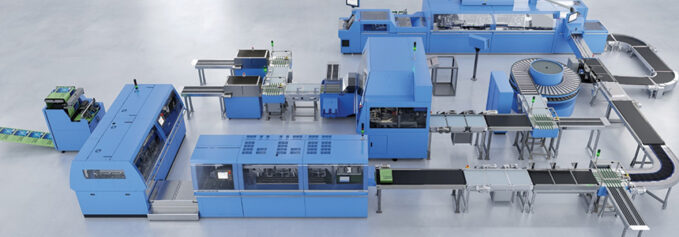
by Cassandra Balentine
The digital transformation of print offers many benefits for those that embrace it. However these advantages are only met when the environment is optimized. Automation drives higher profit margins and helps reduce turnaround time, waste, makeready, and the need for skilled labor. It also improves the quality assurance of complex documents that include personalization and custom finishing.
Above: Müller Martini offers its complete Connex workflow solution, which is broken into Connect LineControl, ImpoWhiz, and Info Cloud.
“Automation is maybe the single most defining feature of the digital transformation of print in the past several decades. As we continue to switch from analog to digital processes, the capacity to automate procedures that used to take lots of manual effort and time has opened up huge avenues for efficiency and expansion for print businesses,” asserts John Henze, VP, sales and marketing, Fiery.
Tom Peire, founder/CEO, Four Pees and chief evangelist, Atomyx, envisions a future in which individualizing print jobs and producing runs as low as one is not just possible and profitable for the happy few, but for any print service provider (PSP). “To achieve this, printers need to take a holistic approach to the entire printing process from concept and order through to production and delivery, instead of focusing on single tools. This means looking for automation solutions that will be scalable as they grow and, more importantly, that will enable them to integrate their management information systems with both their input and output systems.”
With shorter print runs, tighter delivery schedules, and varying printing substrates, an intelligent workflow is a must to organize and prepare jobs. “This intelligent workflow must not only affect printing but also finishing—it must be a complete closed loop,” explains Carlos Martins, head solutions management, Muller Martini North America.
“The numerous benefits of a complete closed loop workflow from printing to finishing include optimizing efficiency in finishing to eliminate makeready times and reduce errors by eliminating manual interventions,” he adds.
Roadblocks to Automation
The benefits of automation are well understood. However, many PSPs are stuck with manual, inefficient, and siloed processes.
It can be challenging for PSPs to narrow down what is holding them back from implementing more automation. “It could be one of many possibilities, but the most important thing for the company manager or owner to recognize is that automation is coming and it’s coming fast. If you don’t recognize the potential, your competitors surely will,” suggests Ray Hillhouse, VP sales and marketing, Plockmatic Group Offline Business Unit.
Suzi Hagay, director of workflow solutions, Landa Digital Printing, sees the order submission process as the biggest challenge towards implementing automation. “If you can streamline the order placement from an upstream system, you’ll be on the right track.”
The sheer volume of information available about automation and workflow optimization can be overwhelming, particularly for companies that may not have in-house expertise. “Adding to this challenge is the fact that much of the advice or many of the resources might not apply to a specific company’s needs, making it difficult to determine the best path forward,” offers Bob Waddington, product line leader for curing and drying, BW Converting.
Finding the right partner is critical to success. “Trying to reinvent the wheel on your own and learning all the potential costly lessons that others have already solved will not benefit an organization looking to effectively implement automation. It may take some trial and error to find the right partner and what level of automation you require,” recommends Tim Bolton, manager, inkjet technology, Ricoh USA.
Don Dubuque, director of marketing, Standard Finishing Systems, suggests visiting vendors’ demonstration centers to see these automated solutions in action as well as connecting with other print providers who have already made these investments.
Company culture often prevents PSPs from embracing automation.
“A well-trained production staff works to get orders through as completely and accurately as possible based on the tools and methods that have been available to them. The roadblocks can often be those members of the staff that have been so ‘good’ at their job using what they have, that they may have lost sight that there may be additional/alternate ways of doing things, and taking time to learn something new is, from their perspective, taking time away from production,” explains Joe Lehn, director of product management, PressWise.
“Change is hard and our day-to-day work often means we deprioritize the future. To be able to transform the workflow, a PSP must understand where the bottlenecks are located and redesign the process. This issue involves hardware, software, people, and processes,” says Kevin McPherson, senior client executive, digital, Quadient.
To overcome these challenges, Ernie Crawford, president/CEO, Crawford Technologies, says businesses must shift their mindset and view automation as a long-term investment, not a risk. The best approach is to start small with manageable changes that provide immediate value and build momentum.
Lehn admits that introducing and successfully implementing an automated workflow is an investment in both time and money.
“When a print provider automates something, it means new ways of doing things. Like any newer technology, investing in the equipment and training resources to implement these changes can be a challenge. The technical know-how and expertise to operate and get the most out of automated systems can require investment in machines, software, and personnel, but the benefits of optimizing production workflow can help offset those initial costs in time,” notes Lisa Weese, director, product strategy and business planning marketing, Digital Press Printing Solutions, Canon U.S.A., Inc.
Integration concerns also play a role. “One of the biggest roadblocks to automating production print workflows is the integration of new automation technologies with existing systems and equipment, especially in operations with a mix of old and new equipment. Additionally, ensuring different systems can communicate and work together seamlessly requires detailed planning, investment in training, and possibly seeking external expertise to ensure a successful transition to automated workflows,” says Matt Raab, marketing director, global product offerings, Xerox Corporation.
Nick Bruno, president, Harris & Bruno International, warns that the road to optimization isn’t always smooth, and for many providers, this can make the journey seem daunting. “One of the most common challenges is the upfront investment cost—automation systems require a significant initial outlay that can deter smaller providers. There’s also the challenge of revamping workflows, as adopting automation means training staff and reevaluating production strategies to ensure a seamless transition.”
On top of that, Bruno believes there’s the lingering perception that automation is too complex or not a fit for smaller operations. “The biggest hurdle is uncertainty about return on investment (ROI). Providers often hesitate without clear data showing how quickly automation can pay for itself. However, once the benefits of faster production speeds and reduced material waste become evident, the hesitancy is replaced by enthusiasm.”
First Steps to Automation
PSPs are able to address labor challenges through automation.
Industrialized automation is not new but it is gaining traction in the printing industry. “We are talking about new technologies on different levels. There is software and mechanical automation and joining those together creates automation where ‘the whole is greater than the sum of its parts,’” shares Alan McLean, regional sales director, Duplo USA.
Those looking to adopt automation have many areas of opportunity to explore, notes Raab, including quality control systems, workflow, job management, fleet production monitoring and management systems, finishing tasks, and inventory management.
Start with an assessment of the process. “The differences between facilities and existing equipment and automation mean there is no silver bullet answer to where to start,” says Dr. Mark Bohan, director, Color Solutions, Konica Minolta.
Jamie Reber, product manager, Software, Kodak, suggests first evaluating and understanding where your inefficiencies reside when automating print workflow. “In order to select the right software and equipment to help you automate it’s important to have a solid understanding of your current set up, where the gaps are, and what those gaps are costing your business. Being proactive upfront will ensure that you research, select, and implement the right software for today and tomorrow. Automation platforms need to be flexible and adaptable to inevitable business and marketplace changes.”
The best place to start with any automation is where it’s needed the most.
“Identifying the manual steps in the worklow is extremely important because those are the areas that can benefit the most from automation—in time, efficiency, and accuracy—all that directly impact the bottom line,” adds Lehn.
You must have a crystal-clear understanding of your current print production processes in order to effectively implement end-to-end automation technology. “Once you have clearly defined your processes from the time a job comes in, you’ll be better able to identify steps that can be automated, areas of redundancy, or other processes that can be improved. This is referred to as ‘mapping the process,’” stresses Marc Raad, president, Significans Automation.
Next, detailed process documentation ensures that everyone involved in the production process is on the same page. This is usually followed by creating standard operating procedures. “These are essential for establishing consistent processes and ensuring that they are followed on a daily basis. Once the processes are mapped and areas of opportunity are identified, creating new, more efficient automated procedures will become much easier, setting the stage for future success,” says Raad.
Start Small
It may be wise to start by taking reasonably sized steps. “Automation of some single processes might be good for a learning experience and yield fast returns. This could set up great awareness of next steps and a foundation for larger scope projects. A large scope can be daunting, and some experience is valuable,” suggests Lance Martin, VP product marketing, Komori America.
Weese agrees, pointing out that looking for small wins is a good place to begin while simultaneously starting the conversation in regard to larger investments and longer term solutions that may need to be made in order to streamline processes and improve productivity. “Moving to automation may be as simple as going from an analog piece of equipment to one that’s digital or, it could get much more complex with new software to aid in automation or even robotics.”
Raad says many printers choose to deploy customized automation in stages, realize the immediate productivity gains and fast ROI, then move on to other areas of their business that would benefit from automation.
Make Way for Automation
Production print automation is increasingly important and prevalent in modern print environments.
Production print automation is able to eliminate cost and errors resulting from manual touch points, streamline workflow from raw materials in to finished goods out, reduce overall production time, and minimize the impact of labor shortages, offers Jacquie Perno, business development manager, ACCO Brands.
However, the complexity of automation can be daunting for companies new to the process. “Understanding where to begin and which solutions to adopt often feels overwhelming, especially with so many options available. It’s critical for businesses to engage with companies offering automation tools and to clearly articulate the value these tools can add to their operations. Gaining this understanding helps secure internal support and capital expenditure approval for automation investments,” says John Cusack, product line leader, BW Converting.
Find a webinar and web-exclusive articles on print automation online at dpsmagazine.com.
Mar2025, DPS Magazine