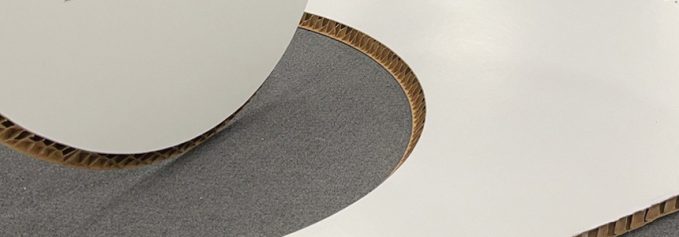
by DPS Magazine Staff
There is increased demand for automation and easy-to-use cutting systems that do not require skilled operators to run. Each segment of the print industry has specific cutting requirements. Advancements are propelled by a need for automation and versatility.
Cutting by Segment
Automation is increasingly important in finishing. Here we focus on several popular areas of digital print—labels and packaging, direct mail, publishing, and wide format. Continued advancements in finishing are fueled by the latest trends and demand for short-run digital printing.
Labels and Packaging
One segment where digital printing and finishing is gaining continued popularity is labels and packaging in markets like cosmetics, food and beverage, craft beer and spirits, electronics, and accessories.
“Demand for high-quality consumer products, which are sold in folding cartons continues to grow at a healthy pace, requiring package printers to keep up with production runs of smaller SKUs or personalized runs,” says Susan Corwin, marketing manager, Rollem International. She points out that the shorter runs must meet retail marketing targets and tight delivery schedules.
Traditional die-cutting methods are not particularly well suited for shorter run lengths and frequent changeovers, explains Corwin. In addition, many printers are seeking automation in the die-cutting process to produce products faster with less staff.”
Chris Van Pelt, president, Therm-O-Type, suggests that newer die-cutting equipment is better suited for small quantity, digitally printed boxes. “New die-cutting equipment technologies, using flexible or steel rule dies, feature touchscreen computer controls, fast set ups, and improved productivity,” he shares.
Versioning and personalization continue to drive interest in this market. “The switch to digital production continues to grow with the introduction of high-volume, off site and low-to-mid-volume onsite production systems driving demand,” adds Terri Winstanley, product and marketing manager, Intec Printers. Accessibility has improved with the introduction of sophisticated, but cost-effective solutions that allow both commercial printers and manufacturers in a range of industries to produce short-run packaging and labelling onsite.
Mike Maze, marketing and digital communications coordinator, MBO America, sees short-run, die-cut projects trending in this space. He notices a need for short makeready solutions that are able to go inline with other finishing operations.
In a similar vein, sticker applications require cross cutting a backliner for an easy-peel feature. “To enable this, cutting software needs to create backliner cross-cut lines automatically depending on the cutline design on front. Also cutting sequence and starting points need to be optimized for stable and fast process,” states Juan Kim, CEO, Valloy Incorporation.
Direct Mail
Direct mail is another popular application for digital print and finishing.
Direct mailers are always looking to produce pieces that stand out in the mailbox. “This means experimenting with even greater personalization, more varied and challenging substrates, or more interesting shapes made possible with die cuts and perforations,” offers Don Dubuque, director of marketing, Standard Finishing Systems.
Van Pelt adds that mailers with round corners and/or snap out membership/discount cards are common products that utilize die-cutting equipment.
Maze says direct mailers also look for roll-fed finishing lines capable of producing multi-up postcards, heavy-stock letters, and self-mail seam. “This is likely driven by the upgrade in print quality that the OEM press suppliers like Canon, HP, and Screen are able to provide. We now see white paper, variable data direct mail production in very high demand.”
Publishing
The publishing segment is heavily impacted by cultural changes that are supported with digital production technologies.
Dubuque believes that publishing is increasingly turning to cutters and trimmers that can keep up with the rest of their production line. “The continued increase in demand for personalization and customization has shortened run lengths and increased the level of variability from job to job. If trimmers can’t keep up, massive bottlenecks can occur. Cutters and trimmers with increased levels of automation are in high demand, particularly those with barcode-driven setup and workflow software support.”
Wide Format
Wide format relies on versatility on the cutting end in order to create a range of applications from banners to floor graphics and packaging.
“The demands of the global wide format, sign, display, and packaging markets continue to grow with manufacturers and converters under increasing pressure to produce faster, safer, and more efficiently, without any restrictions that limit the imagination,” notes Stuart Fox, president, Kongsberg Precision Cutting Systems.
The Push for Automation
Automation is increasingly critical as runs get shorter, variable data demands increase, and labor shortages bring new challenges in terms of efficient production.
Maureen Damato, accounts manager, Colex, says automation features are primarily in demand to reduce operator error and improve productivity.
In smaller companies where limited staff are available, Winstanley points out that automation allows operators to free up time to address other key tasks while the systems do the hard work for them.
Maze believes there is always an increased demand for automation, “the labor market is pushing most industries that way in general,” he explains. “As it becomes increasingly difficult to acquire and keep skilled, knowledgeable operators, the need for automation grows. Even systems that are difficult to fully automate are benefitting from partial levels of automation.”
Angelo Chapa, postpress product manager, Heidelberg, says customers are requesting more automation solutions to reduce touch points, improve makeready times with less experienced personnel while also looking for the automation to relieve the physical stress on operators by adding automatic joggers and unloaders to a standalone cutter.
“Automation makes set-up and changeover from job-to-job quick, accurate, and operator-friendly,” asserts Dubuque. It can help shops reduce downtime, eliminate bottlenecks, and increase productivity. Automation also allows operators to be more versatile and multi-task. With automated cutting, operators can move easily between the cutter/trimmer and other areas of the production line.
Van Pelt sees a huge push to improve automation, especially with die-cutting equipment. “Important automation features include touchscreen computer control with the ability to easily store/retrieve and adjust set up information, provisions to pre-register and align dies, step-and-repeat functions so one-up dies can be used to die-cut products printed multiple-up on sheets, inline waste stripping, and provisions for product delivery and collection.”
In addition, Van Pelt points out that inline waste stripping technologies now include quick-change stripping assemblies for various die-cut formats, programmable stripper fingers, and air blast nozzles to eject exterior and interior die cut waste. “All of these technologies are designed to simplify operation, ensuring fast set up, high throughput, and overall efficiency while reducing waste and operator fatigue.”
Poor ergonomics is an issue that is common with older equipment reducing productivity while increasing operator fatigue and the potential for operator injury. “It is critical that companies review these considerations. Hiring additional employees to operate low production equipment to meet production goals is no longer a viable option.”
With growing concerns for skilled labor, automatic job changing features are gaining importance. Kim says printing barcodes or quick response codes together with artwork requires a cutter to recognize a job ID and select proper cutting data from the database. “Furthermore, job setting information needs to be collected together with cutting data for various parameters of the cutter, like depth and pressure, cutting speed, and other device-specific parameters.”
Labor shortages play a big role in the push for automation. “Companies are frequently struggling to find full- or part-time employees and new employees often lack experience in operating die-cutting equipment. This problem is magnified during peak production periods when additional temporary staff is needed—often on multiple shifts—to handle the increased workflow. This situation creates some additional considerations regarding equipment selection. In these cases, it is important that equipment incorporate high levels of automation, intuitive controls, and good ergonomics—for the widest range of employee body types, and high production speed,” recommends Van Pelt.
He notes that older equipment, which is often slower, requiring higher levels of training and experience, and lacking automation, will only frustrate production goals and require additional labor/cost. Older equipment often does not meet current safety standards for guarding and interlocking. While this equipment might be operated safely by highly trained and experienced operators, this is certainly not the case with new or temporary operators with limited training.
Maze sees another role for automation. “Automation is not just putting a servo motor on a machine adjustment. It can be viewed as ganging together steps in a process,” he notes, pointing out that older finishing models can have many separate processes run in succession taking a lot of time and having many touch points. With modular machinery design, modules are integrated to perform multiple tasks with a single operator. “For example, direct mail printers are not required to make a sheet at the exit of the roll fed inkjet press, then take it to their old bindery for a multi-step process. They can make the folded product direct from the web at very high production rates.”
The Right Cut
Cutting equipment is essential to nearly every print environment. A push towards automation is driven by skilled labor shortages and increased demand for personalization and faster turnaround times. dps
Sep2021, DPS Magazine