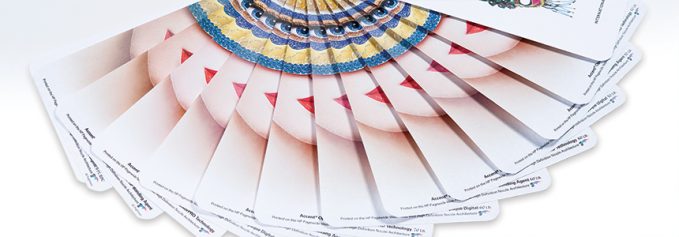
By Cassandra Balentine
High-speed production inkjet printing is gaining acceptance, in part due to improved media compatibility. Historically one of the largest hurdles to inkjet was the availability of well-suited substrates. Printer and paper manufacturers worked together to solve this challenge. Today, print providers running production inkjet presses have access to specially treated and coated options to optimize printed output, utilize on-press treatment options, and/or choose a press designed to handle and run untreated, offset stocks with satisfactory results.
Media selection makes a significant impact on the runability, image quality, and cost of a job. The reaction of different ink types vary on similar stocks. Further, no engine’s inks are the same. Therefore, it is important to properly qualify and profile media.
To ensure the best results, print providers should have an open dialogue with their print engine manufacturers as well as media suppliers to understand the nuances of its specific media compatibility scenario.
Compatible Options
Media options for production inkjet have come a long way in recent years. Treated papers are optimized to improve optical density and color gamut for reduced bleed, show-through, and mottle. Each paper varies in many ways, from pulp to surface chemistry.
For optimal and consistent results, many original equipment manufacturers (OEMs) test and qualify papers based on a critera for ink loading, speed through press, and dryer heat settings.
“We have a strong relationship with our OEM partners. We are continuously testing new substrates to ensure compatibility with their existing equipment as well as working to identify any new technology that could enhance the print experience,” shares Karin King, brand manager, International Paper.
The majority of OEMs have a certified media list that they share with their customers. To earn a spot on the list, the supplier must work with the OEM to trial each substrate to ensure consistent, high-quality performance on press.
It is important to remember that testing can be limited based on time and resources, especially as OEMs respond to market demands to open their platform to a wider variety of papers. “Furthermore, international marketing initiatives to push new ink sets and the compatibility across paper stocks are not only driving what gets tested but what we consider a successful test to be. So, yes, a paper can pass, but what am I sacrificing in terms of speed, efficiency, overall job costs, and return on investment? It becomes a balancing game,” explains Susan Murray, manager, product planning and public relations, Mitsubishi Imaging, Inc.
To ensure papers run smoothly, print providers should ask about paper qualifications and true costs. Sample questions might include—do I need a pre- or post-coating? How do papers handle during finishing? What mode can I print in to reach desired results and what percentage of ink savings do I get in one mode versus another? Does my dry time increase? How fast can I run this paper through the press? I am running a variable print job and some pages have one percent ink coverage and other 60 percent, can I maintain a consistent speed of 500 feet per minute or does the whole job need to slow down to accommodate the heavier ink load? Should I be more concerned about paper dusting with one paper versus another? “Once you start looking at the total picture, a paper’s true compatibility becomes clearer,” shares Murray.
Tyler Sukeforth, brand manager, coated paper, Sappi, says many OEMs provide media certifications, however the quality is wide ranging and the stamp of approval depends on the OEM’s certification process.
OEMs offer a variety of lists or approvals for media compatibility. Ashley Maydak, brand and creative manager, Domtar, says the verbiage is very specific—in the case of licensees, or very broad with a large target audience. “We do our best to engage and know them all. The key to assuring smooth sailing is to be aligned with a paper company up and down the value and relationship chain; that’s where Domtar truly differentiates. We’re close with the color management teams and we’re always working toward trusted advisor status at the highest levels of the organization. From our standpoint, it’s never a paper or equipment issue—when a customer isn’t printing, it’s a collective challenge to solve. No finger pointing.”
Geo Plumberg, senior product manager, Boise Paper, notes that most OEMs are willing to perform paper testing and provide performance results to both suppliers and OEM customers. “OEMs also provide on-equipment or internet-based profiles to support equipment owners/users with optimal performance guidelines for the substrate they are considering. They can only provide these guidelines if the manufacturers collaborate with OEMs to perform tests.”
Biggest Obstacles
While substrate compatibility for production inkjet printing has greatly improved, issues still exist.
“‘Paper is the fifth color’ is a common mantra that’s been repeated in the print industry for as long as I can remember,” says Maydak. “Even with today’s new printing technologies, it still holds true. It’s been cited that paper compatibility is still the biggest struggle with new adapters to inkjet, and this is largely due to the fact that many do not think about paper until late in the process.”
When choosing a paper, Maydak says it’s important to consider the type of equipment it is made to run on. “Our treated production inkjet paper is engineered to run on production inkjet equipment—so it delivers brighter and more vivid colors, similar to what many print customers are used to seeing on their jobs from other printing technologies—and they’re also made to withstand high speeds and the rigors of post-processing equipment.”
As OEMs continue to invest in this technology they make great advancements towards solving compatibility issues. “The introduction of new HD or magic inks, inline coating solutions, and workflow automation help increase paper compatibility with high-speed inkjet equipment. Additionally, next-generation software promises algorithms for better color management and paper profiling. The best has yet to be seen,” comments Murray.
The ever-changing and wide array of inks available for different equipment makes and models is a challenge when it comes to paper optimization. “Some inks require machine pretreatment, while others call for treatment to be added during the paper-making process, and still others deliver acceptable output without any treatment,” shares Plumberg. She adds that the performance of ink has greatly improved in recent years, with shorter drying times and increased ink densities—all while purchasing has become more cost effective. “It is critical for us to keep up with these continually changing requirements to provide workable solutions for our customers.”
Sukeforth says that for many years, the biggest obstacle for inkjet compatibility was the need for a specialized coating to facilitate ink absorption and drying. However, many of the latest generation inkjet engines are now capable of printing on standard coated offset media as pretreatment, ink, and drying technology have evolved over time.
“Due to the water-based nature of inkjet inks and inkjet press technology, selecting the right paper is an important factor to optimizing the end result,” admits David Field, director, inkjet media, Midland Paper. The biggest challenge he hears from customers is sifting through all of the papers in the market to determine the best match for their application and end user requirements. “Essentially, selling an inkjet printed piece is all about managing the expectations of the print buyer. As such, in addition to the paper component, inkjet printers need to consider the anticipated total ink percentage, color critical elements—such as corporate logos or flesh tones, ink solids versus line copy/screens, press drying capability, finishing requirements, and the OEM press model and ink composition,” he explains.
King believes that every new inkjet customer has different expectations and needs as they evaluate and select equipment vendor, press, ink, and paper. “When it comes to paper, some customers want the best ink density or color gamut while others are looking for a more economical grade,” she offers. Other factors to consider are yield, print show through, ink drying, and convertibility. “Ultimately, every customer values paper attributes differently, and therefore, select a range of paper grades. There is not one grade of paper that works for all customers.”
Murray says education and training are obstacles for print providers. “Print technologies are changing and evolving so fast, as soon as we scratch the surface on one, a newer functionality is released. As exciting as innovation is, it also inhibits our ability to learn the nuances of a technology.” She says if you consider that a standard installation takes less than six weeks from purchase to install to up and running—it’s not a lot of time to be fully up to speed on the capabilities. “Paper profiling and color management often take a back seat to machine operation and trouble shooting. The good news is, we have seen excellent results from customers that use our papers and have invested in experienced and well-trained press operations.”
Supply chain challenges are also a consideration. The benefit of digital printing is that it enables just-in-time production and delivery. The issue with that model—especially when it comes to the increase in volume production inkjet presses handle—is having the media stocked.
“Multi-million dollar investments cannot afford to go down, and this requires a stable supply of paper,” says Maydak.
The biggest challenge of paper suppliers and manufacturers is the lack of forecasting. With on demand printing comes on demand paper. “The challenge with that business model is having available stocks in specific grades, sizes, and weights for immediate, low-cost delivery. In a perfect world, a mill would like forecasting a year in advance, giving them time to produce and deliver in the most cost-effective manner. Usually they only know a couple of months out. Even when print providers have multi-year, contracted agreements, exact mailing dates, files, and paper requirements are often unknown,” explains Murray.
“Generally speaking, supply issues for the production inkjet market are few and far between compared to where the inkjet industry was four to five years ago,” argues Field. Today the availability of common inkjet web roll sizes such as 18, 19, and 20 inches is much more prevalent, but can vary depending on the paper grade and basis weight.
Treatment on Press
In addition to treated and coated media options, production inkjet equipment manufacturers develop inline priming solutions to help optimize paper on press.
Sukeforth says pretreatment options are effective in improving print performance on traditional offset media, and greatly expands the media catalog available to printers.
Although inline primer treatments can be effective, it is important to consider cost, maintenance, and efficiency issues. “First and foremost, there is the price of the primer itself. Second, applying to the primer is another step in the print process, which effects your overall production speed both through application and drying time,” says Murray. She adds that total running costs, carbon footprint, man hours, and speed to market are negatively affected. “The primer can also cause wrinkling, mottling, or misregister, which, in a worst-case scenario, could make your job unusable. Your total cost of ownership also goes up, additional printheads and drying capacity increase your machine cost.”
Inline treatment options are beneficial for spot colors or projects that don’t require large, solid areas of ink coverage. “For jobs that require vivid graphics, realistic skin tones, and bold blacks, we recommend an inkjet treated sheet like Accent Opaque with ImageLok Technology. Additionally, if ink drying is a concern, inkjet treated sheets tend to perform better than inline treatment because they do not add moisture to the sheet,” says King.
While the pretreatment options available on press are best discussed by OEMs themselves, from a paper perspective Maydak says Domtar offers papers that can be used with or without these pretreatments. “Which is correct?” she asks. It is truly a customer by customer decision that should take into account price models, expectations, and availability—media flexibility.
Murray points out that generally, papers specifically engineered for a process typically work best. “Even as systems continue to develop, it is most likely that inkjet papers optimized for inkjet printing will continue to outperform standard offset papers if optimized resolution and maximized production speeds—speed to market—remaining driving factors.”
“Every print environment and print job has different requirements and rapidly changing printing technology continues to evolve to address market challenges,” shares Plumberg. It is critical to understand the needs of customers and support their decision making processes for each job.
Coated Stock Considerations
Coated paper options are available. These papers are specifically designed for high-speed production inkjet and feature coatings designed to trap ink before it can penetrate the fibers of paper.
Inkjet coated papers provide the benefit of lower ink consumption and faster dry times enabling jobs to move directly to inline finishing. “Although these papers can be more expensive than standard offset papers, the price differential can be less than the associated cost savings gained through efficiencies—quicker production speeds with no pre- or post-coating—and lowered ink consumption. In addition, the typically more expensive high definition or magic inks are not required for most coated papers,” shares Murray.
“Inkjet coated paper—specifically designed for inkjet looks amazing; it also comes with an impressive price tag, as it should,” says Maydak. “It delivers near offset quality for an industry that has long struggled to replicate this quality with standard papers. You are truly paying for the chemistries that deliver premium output.”
That said, customers tend to balk at pricing; it has proven unsustainable when used on high-volume jobs. “One of the value propositions of inkjet is that it is a one-stop shop—combining color with variable data. Inkjet delivers both, but at varying levels of print quality. Customers need to decide if this works for them,” says Maydak. It is important to note that offset shells will remain until there are reasons for them not to—inkjet must print on everything and deliver offset-quality results. “We’re not there yet, but getting closer.”
“Our goal is to help our printers cost-effectively maximize overall product quality, ink savings, color gamut, and paper performance in the pressroom and finishing department. Inkjet treated/coated papers are manufactured to work specifically with water-based inkjet inks. The treatment/coating allows the inkjet inks to fix the colorant to the surface of the paper, resulting in vibrant ink densities, optimal paper drying capacity, faster press speeds, and high-performance finishing techniques,” shares Field. Depending on the OEM press mode and drying capacity, the printer may achieve faster press speeds with an inkjet treated/coated paper as compared to standard coated fine paper. Further, the price delta between certain inkjet treated/coated papers and commercial coated fine paper has narrowed in recent years.
Primed for Print
OEMs and media manufacturers collaborate to offer solutions for media challenges historically associated with production inkjet printing. While print engines offer inline priming options and support for standard offset stock, media manufacturers present treated and coated options to ensure optimal results. dps
May2020, DPS Magazine