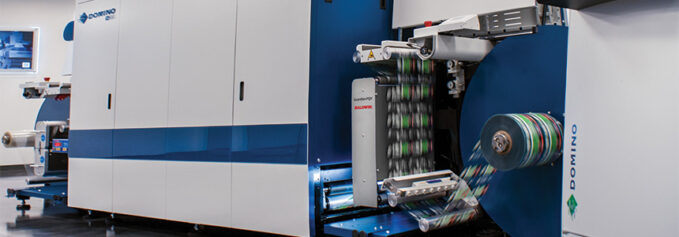
by Cassandra Balentine
Primary uses for vision systems include print inspection, intuitive operation, and compliance with industry standards for label and package production. As more digital print technologies are adopted, these systems become increasingly important to ensure accuracy, quality, and compliance.
Above: Baldwin’s Guardian PQV 4.0 features advanced automation, micrometer inspection precision, and its new Wizard-iQ Interface.
“The most significant demands for inspection or verification systems include ensuring print quality, detecting defects such as color variations, misprints, registration errors—ensuring accurate barcode readability, and verifying the correctness of all variable data, such as expiration dates or product codes,” says Dr. André Schwarz, director marketing and documentation, EyeC.
Print inspection systems that detect and verify the correctness of text, graphics, and other printed elements are crucial for preventing errors in packaging. Senol Feizi, technology manager, director of technology and business solutions, Complete Inspection Systems, Inc., says this includes identifying and flagging defects such as misprints, smudges, streaks, or missing print.
Verification and inspection systems provide a solution that includes all functionality required for inspecting various label components. Comprehensive vision and inspection solutions are in high demand. “A typical label contains multiple components including text, graphics, specific colors, barcodes, and sometimes braille. This requires a solution capable of inspecting the entirety of the label all at once without having to switch between systems,” offers Julie Meredith, CMO, GlobalVision.
Doron Ben Avraham, business development manager, digital printing and vision inspection specialist, BST North America, a subsidiary of BST GmbH, an elexis company, feels the industry’s goal is to establish closed-loop systems that combine register calibration, color process control, and quality assurance inspection into one efficient and cohesive process.
“The realization of such closed-loop systems points towards more collaborative OEM development with press machine manufacturers, reflecting a strategic shift towards more integrated and advanced manufacturing solutions. Such collaboration is essential for achieving the seamless functionality and enhanced efficiency these systems offer, marking a significant advancement in the realm of printing technology.”
Meeting Evolving Demands
The evolution of digital printing techniques bring a range of innovations that drive even more demanding requirements from inspection/verification systems providers. John Cusack, product line manager, Inspection Products, Baldwin Technology Co., says the main areas include variable content, more data-driven workflows, more complex brand owner requirements, and the ability to support shorter run lengths.
Guy Yogev, senior director product marketing, AVT Inspection Product Line, Esko, points out that the global packaging and labels markets faced many challenges in recent years after the COVID-19 pandemic and the situation of economy, instability, high interest rates, and inflation; sustainability and recyclability; rising costs of materials and energy costs; and limited, experienced professional labor; as well as changes in brand owners’ needs with increasing number of SKUs and shorter job lengths.
Further, special features are increasingly added to print and packages, as well as special coatings, variable codes, and security factors that need to be verified. “Quality standards remain high and require high-resolution, high-speed inspection solutions,” shares Yogev.
Inspection and verification systems for labels and packaging segments are expected to ensure quality and reliability. “Users are looking for a quality inspection ‘insurance policy’ for consistent flawless output and minimal errors,” shares Meredith.
It is also important to consider prepress. “Of course, an inspection/verification system needs to know what it is looking for, and this is best prepared in the prepress system,” shares Mike Agness, EVP, Americas, HYBRID Software. Solutions like HYBRID PACKZ and CLOUDFLOW prepress systems set up each job for inspection/verification and advise inspection systems to look for items such as color, variable data, and barcodes—among many others.
Particularly with digital presses, time is of the essence. “As jobs race through the facility, a prepress system must be able to set up these parameters quickly. Remember that two PDF files are usually created—one for the RIP and press, and one for the inspection system. A good prepress system prepares them automatically and from the same incoming file. What makes them different is the removal of die layers in the PDF for inspection, but these might be on the print file for lead-in/lead-out creation. Just as important, they have to be accurate in defining what to look for. You don’t want to stop a 1,000-foot roll from a digital press either because the verification parameters have not been defined or, worse, defined incorrectly,” explains Agness.
Meredith says security and traceability also play a role, and these areas have become more critical as companies are expected to protect data integrity and comply with regulations.
Rising demands in different industries, such as food, pharmaceutical, or fast-moving consumer goods, increase the complexity of information on labels and packaging.
We cannot forget about sustainability. By preventing printing errors and minimizing reworks, Schwarz admits that vision/inspection systems eliminate a large amount of waste and ensure environmentally responsible production processes.
Looking Ahead
As digital print technologies continue to advance, shifting market needs and demands, vision and inspection systems are on par to keep up. One technology in particular is poised to have a big effect on the future of verification/inspection systems. You guessed it—artificial intelligence (AI).
“AI is going to be one of the innovations we see getting into print inspection to improve manual processes, streamline quality standards, and improve the focus on sellable product versus rejected/non-sellable,” agrees Yogev.
Feizi sees AI impacting inspection systems over the next couple of years through the development of AI algorithms trained to automatically detect and classify various defects, such as misprints, color variations, streaks, and registration errors and thus reduce the rate of false positives flagged. This will reduce time spent on verifying alerts that slow down production.
“As AI continues to expand, our inspection systems will have the ability to learn from extensive data sets, leading to more intelligent defect detection and automatic classification. This will enhance the accuracy and efficiency of the systems, reducing instances of false positives and negatives,” predicts Schwarz.
By integrating machine learning algorithms and cloud-based systems, Schwarz says inspection systems will become more adaptable and proficient in handling intricate printing and finishing environments, optimize packaging, as well as labeling efficiencies.
Yashashree Potdar, workflow solutions analyst, Standard Finishing Systems, finds it difficult to speculate on what role AI will have in print inspection in the future. “Going forward, any technology that removes manual touchpoints and improves end-to-end automation will be important in the development of vision/inspection systems. At this exact moment, print inspection requires a level of precision that most market-ready AI still hasn’t mastered. But that doesn’t mean that day will never come. Companies are already making in roads with high-precision AI image classification.”
Further, Ben Avraham points out that predictive maintenance will be a game changer. “It will enable the systems to anticipate and address potential failures before they occur, thus minimizing downtime,” he offers.
Getting it Right
Vision and inspection systems are important to label and packaging environments. As digital adoption grows, the pressure is on to ensure not only quality, but accuracy complies with shorter runs and variability in a way that doesn’t impede production and profit.
Read more on the topic in our three-part web series:
Part one, New Demands
Part two, Addressing Challenges
Part three, Inspection and Verification Systems
Mar2024, DPS Magazine