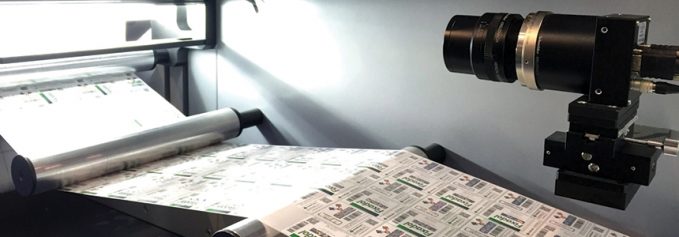
DPS Magazine Staff
Inspection/verification systems improve output quality and document security during the print production process. These solutions help reduce labor costs, improve integrity, implement audit/tracking, and ensure data security. Popular applications include print quality inspection, color quality monitoring, MICR and barcode verification, matching, assembly integrity, and forms verification.
Above: Lake Image Systems has optimized its Discovery Multiscan 3 software to use the latest line scan camera technology.
Inspection/verification systems manage quality control and maintain efficiency on shorter runs while meeting tighter turnaround time demands.
“Vision/inspection systems are integral for print providers in any vertical, particularly in this era of high-speed production and short-run applications,” says Don Dubuque, director of marketing, Standard Finishing Systems. He explains that at the printer, inspection systems perform a number of quality checks including color tolerance, pattern matching, white space verification, ink or toner spills, voids, and jet-outs. At the finishing end, inspection systems perform sheet and set-level integrity checking for booklets and verify the order of signatures during folding.
Role in Digital Print
Inspection and verification systems play an important role within the digital print and finishing space. They are increasingly important as digital printing and finishing equipment is used more widely to produce larger volumes of labels, packaging, and publishing materials.
According to Nick Khatri, group marketing manager, Lake Image Systems Ltd., unlike traditional offset printing, digital printers are allowed a high degree of flexibility and variability between jobs and within the job itself. “For example, serialized or variable data labels can have a unique number, text, barcode, or quick response (QR) code on every label printed in multiple lanes across the web to maximize production. Each code or barcode must be verified to prevent issues when the label is applied to a product, shipment, or document. Also, these camera systems can check for print quality issues such as correct print registration, color variation, toner marks, streaks, and voids,” he offers. Camera inspection systems are increasing important to replace outdated web viewing systems or manual inspection quality assurance (QA) processes.
Khatri says inkjet digital printing has increased flexibility even further. “Inkjet printheads on existing traditional presses, converters, and production lines allow companies to build hybrid systems for maximum efficiency and profitability. Camera inspection systems are a growing requirement to catch inkjet printing errors such as misaligned inkjet printheads, missing or mis-positioned print, or even operator error in setting up dates, lot numbers, or sequential numbers.”
Lucia Dauer, product manager, print inspection, ISRA VISION, points out that digital printing requires new processes, workflows, and high automation. Brand owners face increased demand for customized and short-run goods or individualized corrugated boxes or folded cartons, which means a packaging printer must be able to react to digital print quality issues to keep the quick turnaround and achieve quality control. Inspection systems reduce the lifespan of a digitally printed defect.
Ralf Wirtz, sales manager, GMBH sites, AB Graphics International, says camera solutions are added to digital or hybrid presses and finishing lines. “The camera can detect the defects at much higher speeds in comparison to the printing speeds of the digital press technology, meaning that one finishing line can furnish multiple digital presses.”
Similarly, solutions like the Standard Finishing Hunkeler WI8 Web Inspection System are able to capture high-resolution images at production speed using a Compact Image Sensor (CIS) scan bar. These full-page images can then be compared to a control sample image to quickly catch color shifts, spots, streaks, positions, and contours to help ensure that quality and content errors are caught early.
Vision/inspection systems recognize and classify all standard barcodes as well as check text images for print errors, data in OCR characters, and braille for errors. Specific to AB Graphics’ fleyeVision system, Wirtz says images are recorded by a digital line scan camera with between 1,024 and 8,196 pixels as a color or a grayscale picture.
Image processing is handled in the computer where output like labels are continuously recorded and compared to a previously created master image. There is also the option to verify the master image using a PDF comparison process. “When equipped with two cameras, a fleyeVision print machine can be used to inspect labels simultaneously both front and back or using different light sources at a single path,” shares Wirtz.
When an error is detected, its type and position of the error is indicated on the monitor, allowing the operator to then remedy it. Wirtz adds that any stored errors are then processed in sequence. With bi-directional machines the corrected error is again subject to inspection after fleyeVision has been restarted, guaranteeing 100 percent inspection.
Features in Demand
Because vision/inspection systems are essential for printing, Dubuque points out that print providers who produce commercial publications, direct mail, food packaging, newspapers, pharmaceuticals, transactional mail, tickets, or any other application that requires variable data and precise information benefit from the technology.
Paul Stinson, sales director, Lake Image Systems, points out that certain applications require higher levels of inspection sophistication than others. “In the security printing industry for example, where every document, label, or stamp has a monetary or security value such as ID cards, vouchers, authentication labels, tax stamps, or lottery/gaming applications, every item has to be checked for printing defects before it can be used.”
He explains that here, even a small printing flaw must be caught to meet very high levels of quality standards. The camera inspection system checks for glitches, ensures variable data is printed correctly and in the right place, and confirms there are no missing or duplicate items within the entire print run. “Sometimes, the check must go across multiple print runs. In most cases the data requiring verification is on highly reflected/holographic surfaces or printed in UV/IR fluorescent ink, which require special lighting, filters, and optics to do the job correctly.” Here, an inspection systems provider must be able to verify that both static print quality and variable print data is printed to the required standard. The system must inspect the end-to-end integrity of the job for missing, out of sequence, and/or duplicate items.
“In this era of short turnaround times, manual inspections are no longer feasible. Inspection systems can be placed on printing presses, sheet-feeders, saddlestitchers, perfect binders, paper folders, and mail inserters to identify errors in production in real-time. Inspection systems can perform verification of material imprinted with virtually any standard symbology, including 1D and 2D code, OCR characters, MICR, addresses, or even OMR markings at the click of a mouse or via touchscreen. Any print provider knows mistakes are costly, so inspection systems are integral in guaranteeing product quality without increasing labor costs,” explains Dubuque.
The demand is for 100 percent defect detection. Dauer says this means using the features of defect classification to detect and warn on all typical digital printing defects, including streaks, banding, missing prints, spots and splashing, miss registration, and color variations.
One important feature of vision/inspection systems is the ability to detect relevant defects, for example the CartonSTAR vision system will inspect only relevant defects to avoid false alarms that may lead to unintended waste. “When we talk about material, our substrate compensation feature is in demand by digital printers in corrugated packaging,” says Dauer, as corrugated boards show structures in their material and the typical waves may be visible.
Color measurement features on vision/inspection systems are also attractive. “Measuring color—both relative or absolute—is important for digital printers to see the color stability within a job run or trace absolute color values to see if it matches the brand owners’ requirements,” shares Dauer. She explains that threshold charts allow operators to see if the print run is within a given delta E deviation with one look.
For Consideration
With any technology, there is generally room for improvement or specific considerations that should be addressed. There is a continued push for heightened productivity and more automation.
“Inspection systems are not one-size-fits-all,” admits Dubuque. They must be properly programmed to meet the specifications and needs of each print provider, which can require a lot of setup and a complex integration process. “This is especially true of shops that are new to automated inspection systems. Each new generation of inspection systems are improving on the steep learning curve, but this is an area that still needs to progress in order to bring more print providers on board. Easier integration and more compatibility are on the horizon.”
Martin Keats, managing director, Lake Image Systems, says it still encounters sites where camera inspection systems are an afterthought, when it should be considered an integral part of the planning process. “Some view camera inspection as a ‘nice to have’ until they are required to meet a contractual or regulatory requirement, or find that their in-house manual QA or sampling process is just not good enough and is reducing operational throughput and increasing print waste.”
Dauer says every print house that goes into digital printing faces the demands of a digital workflow. She points out that ISRA VISION is also a part of the digital workflow. “For the future, we see room for improvement in standardized interfaces that will allow even higher automation of the digital print workflow. Also, the movements in Industry 4.0, standardizing interfaces and workflow of data, also support the packaging industry—especially the digital printing workflow.”
Today, in order to manage customer print jobs in a digital workflow, a vision system can be integrated to receive production management data of an MIS. “This is a good start for the digital printer towards a centrally controlled digital workflow through sharing and making use of the data at each process step,” says Dauer.
Product Evolutions
As digital print systems and supporting technologies advance, vision/inspection systems also continue to evolve.
“Over the past few years, inspection systems have evolved to keep up with higher speed presses so that quality control doesn’t come at the cost of production speed,” states Dubuque.
“As digital printing technology has advanced, camera inspection systems have also evolved alongside,” agrees Khatri. While digital printers increase their print speeds and image quality, advances in camera, optics, LED lighting technology, and PC processor and networking speeds have also enabled inspections systems to keep up. “For example, at Lake Image Systems we have optimized our Discovery Multiscan3 software to use the latest in 16K line scan camera technology, run on the latest PC hardware, and on Microsoft Windows 64-bit operating system. This has allowed us to increase the image resolution we can capture to detect smaller and smaller defects, increase image capture rates, and perform inspection processing at higher speeds, whilst maintaining hardware costs.”
When used effectively, vision/inspection systems can reduce waste by identifying defects in real-time—even on high-speed presses—to prevent costly re-work and generate a variety of production reports for compliance. This is especially important when presses are installed roll-to-roll because there is no longer an opportunity for a visual check. “Print providers need to catch errors before the web is rewound. Inspection systems can automatically stop the line if there are extreme issues in production. This level of detection on inline systems helps reduce waste and overprints for the end user—catering to the digital printing model of short runs and print on demand technology. For offline or near line systems, vision/inspection systems verify that everything is printing in the correct order without duplicates and mark individual pages for removal further down the production stream,” comments Dubuque.
Wirtz says its inspection technology is constantly evolving. “The fleyeVision 4k color system is the latest model, which shows a 50 to 80 percent higher level of performance—maximum inspection speed. This enhanced performance is driven by an OCR and barcode inspection rate four times faster than before and is linked to hardware with higher performance and software optimization.
In addition, Wirtz says fast makeready times and integration with MIS/ ERP helps aid digital printing and the production of many short-run jobs is an evolving area.
Dauer adds that the ISRA surface vision system and inspection technology are ready for use in networked production processes, concentrating on detecting the typical defects of digital print through intelligent algorithms. “As digital workflows produce a lot of data, it becomes valuable once it is turned into relevant information. With our EPROMI software we aggregate information and analyze and visualize data to provide reporting and analysis tools, like statistics, trends, and charts—so a digital printer can determine the future strategy of flawless production.”
Waste Reduction
One area where vision/inspection systems excel in is waste reduction. Early warning and immediate reaction once a defect is detected helps in terms of waste because the vision system is at each production step starting at the beginning of the lifecycle.
“Simply put, an inspection system can inspect 100 percent of the printed output, 100 percent of the time, so that it can alert the operator—or for re-occurring errors, stop the press—on finding a defect to prevent the press from producing more bad prints,” shares Khatri. “The human eye simply cannot do this at production print speeds.”
For most operations it is inefficient to stop the press for every defect such as a random spot, streak, or variable data error. Khatri says camera inspection systems log the precise nature and location of each error, allowing the press to continue and complete the print run. “The printed roll can then be mounted on to an inspection station, and the roll map is used to instruct the station to stop at the precise location of the error, allowing the operator to make good the defected piece.”
Dubuque adds that when used effectively, today’s vision/inspection systems prevent waste by identifying defects early in the production process. Systems can be placed on print lines, sheet-feeders, saddlestitchers, perfect binders, paper folders, and mail inserters to identify errors in production in real time.
Dauer comments that when a human quality control manager realizes at final production steps of a folding box that the quality is not acceptable, the detection is too late—and again, more waste is created because all earlier production steps have to be performed over. “The most economic way is to detect only relevant defects right at the time of printing and thus allowing as much waste as absolutely necessary, but not more,” she says.
On the Market
A number of vision/inspection systems target digital print environments. Here we highlight solutions from companies mentioned in this article.
AB Graphics’ fleyeVision is a 100 percent print inspection system designed to prevent customer rejections. As a stand-alone system, fleyeVision can be integrated into any press, converting machine, or control system.
ISRA VISION print inspection systems have a high-level classification for defects, to reliably detect only relevant defects. The system has an interface to connect to a MIS or the printing machine and delivers reporting and live inspection data.
Lake Image Systems offers two primary solution platforms for print inspection—Discovery Multiscan3 and Discovery Enterprise. The Discovery Multiscan3 platform takes inputs from a range of linescan and area scan camera technologies. Discovery Enterprise provides a comprehensive process integrity control and management, document quality control, and reporting solution.
Standard Finishing offers Hunkeler’s WI8 Web Inspection System and Standard VIVA Inspection Systems for Horizon products. Hunkeler’s WI8 Inspection System uses CIS to provide precise image monitoring of both sides of the paper web during production and absolute quality assurance. Standard’s VIVA product line is an automated integrity and verification system that can be deployed across a range of Horizon finishing solutions including perfect binding, bookletmaking, and saddlestitching. It provides tracking, end-to-end system control, and production reporting.
Seeing it Through
Vision/inspection systems are essential for print providers in any vertical, particularly in this era of high-speed production and short-run applications. Continued integration advancements help these systems evolve to support digital workflows and Industry 4.0. dps
Jul2021, DPS Magazine