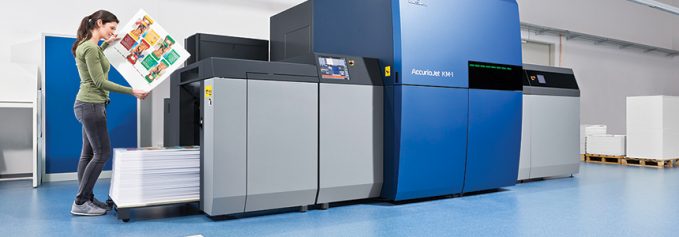
By DPS Magazine Staff
Cutsheet inkjet systems continue to advance in terms of speeds, feeds, and image quality to attract new users. With rising expectations for digitally printed output, image quality enhancements are particularly in demand.
Above: Konica Minolta’s AccurioJet KM-1 features durable, UV ink.
Advancements in printheads and ink formulations factor into quality improvements, along with enhanced drying systems and optimized paper paths.
Quality Improvements
Image quality is always a top priority for print service providers (PSPs). Production inkjet technologies were considered lacking in this area when compared to more mature technologies like toner- and laser-based systems. However, mechanical advancements and new ink formulations are changing this perspective.
Specific to cutsheet inkjet production presses, printhead advancements are changing the scene. Ink development also plays a strong role in continued image quality advancement.For example, the Canon varioPRINT iX series offers 1,200×1,200 dpi printheads. “Not only that, but the combination of iX performance water-based inks and ColorGrip Technology enables stunning image quality on a range of media with matte, silk, and gloss surfaces as well as both coated and uncoated paper stocks up to 350 gsm,” offers Lisa Weese, director of marketing, production print solutions, Canon Solutions America.
Ed Pierce, product marketing manager, Fujifilm Graphic Systems Division, brings up advancements in inks, screening technologies, and printheads such as the Fujifilm Dimatix Samba printhead. “The integration of these technologies has the most significant impact on production inkjet quality as evidenced by the Fujifilm J Press 720S and now the newest generation J Press 750S,” he offers. By controlling where the ink is placed and jetting such a tiny droplet of ink to such an exact specification time after time, the quality is not only advanced but it is also managed where it matters most.
Glenn Toole, VP sales and marketing, MCS, agrees, noting that in regard to image quality, improvements are often related to media and ink development. “Of all the technical print challenges, managing the ink drops after they reach the paper has the largest influence on quality,” he offers.
Bill Troxil, SVP, strategic business development, Konica Minolta Business Solutions U.S.A., Inc., says the newest AccurioJet KM-1 inkjet printheads are designed to render even better quality with increased life expectancy. “This will have the biggest impact for our growing base of KM-1 press customers to gain quality and further improve uptime and operational efficiencies with their previous investment,” he offers.
Many factors contribute to achieving the highest image and print quality. However, if you have to focus on one single advancement with impact on image quality, Hal Stratton, graphics technology center manager, Komori America, says it would be higher resolution of inkjet printheads. He says 1,200 dpi/Stochastic screening allows for greater fine details in printed images and better reproduction of Serif typeface text. “When 1,200 dpi/Stochastic screening is combined with the larger color gamut of the base CMYK inkjet inks, this contributes to the ability to expand the proven match of more Pantone spot colors within a Delta E of less than 1.5 to 2,” he explains.
“You would think reliability and low cost of the printheads would be the primary concern among end users, but it is in fact image quality that takes precedence,” admits Jesse Heindl, marketing manager, RISO, Inc. “Everyone enjoys the low cost and speed of inkjet, but it cannot come at the cost of image quality.” He predicts that improved inks will drive this technology forward.
Speed and Productivity
Rated speeds for cutsheet inkjet technologies continue to climb, further closing the gap between digital and offset.
Weese points out that speed is only one aspect of productivity. “Sheetfed inkjet will never match continuous feed, however speeds have increased up to 312 letter duplex images per minute or 4,500 12×18-inch sheets 4/4 per hour. In addition—media evaluated thus far, up to 350 gsm—all run at rated engine speed. Across the board, PSPs are looking to do more in less time, which is more than just pages per minute (ppm),” she shares.
For example, the Canon varioPRINT iX-series offers high uptime averaging 94 percent reliability, and productivity to produce more in less time.
Pierce comments that throughput speeds for production sheetfed inkjet continues to increase and this is key to delivering an improving return on investment. “The newest generation J Press from Fujifilm, the J Press 750S, runs at 3,600 sheets per hour (sph) compared to 2,700 sph by the previous generation.”
Konica Minolta’s cutsheet inkjet technologies features an imposition gain due to the 23×29-inch sheet size and offers inline finishing to reduce touch points. The AccurioJet KM-1’s durable UV ink gives customers the ability to go directly into the mail stream because there is no need to post treat or coat the finished product, saving time and money. “The result is 9,000 4/4 full-bleed 8.5×11-inch letters, or as another example, 30,000 4/4 4×6-inch cards per hour instantly dry, cut, trimmed, and ready to go,” shares Troxil.
Will Mansfield, solutions marketing, Eastman Kodak, says the PROSPER S-Series and PROSPER Plus inkjet components are integrated on sheetfed presses and transported without slowing down the analog press or finishing equipment. “This allows our customers to transform virtually any traditional printing press or finishing line into a hybrid inkjet printing system, giving them the best of both worlds.”
Stratton feels larger sheet size, physical speed, and the ability to duplex/perfect contribute to improved speeds in cutsheet inkjet. “When the subject of press speed comes up, customers with offset presses are always looking at the maximum printed sheets they can print per hour. As sheetfed toner and now inkjet digital presses have started to make their way into the production printing arena, offset and toner/inkjet press owners need to understand the calculation of sph compared to per page models of other devices—the overall output that this type of press can produce.”
The Komori Impremia IS29 offers a 23×29.5-inch maximum sheet size, combined with set press speeds of 3,000 sph in single-sided mode and 1,500 sph duplexing/perfecting to enable a variety of impositions/sheet sizes—with variable data capabilities.
Toole says improved print speeds are attributed to both higher speed printheads as well as increased sheet size capability. “If the size of the printed sheet doubles then the throughput of smaller, letter-size sheets doubles correspondingly. One of the most interesting developments that impacts speed, cost, and quality is the segmentation of products along feature sets that are important to customers.”
Heindl says every generation of RISO devices improve on prior models in terms of speed. “With our current series, the ComColor FW delivers between 90 to 120 color cutsheet ppm, and our two ComColor GD models deliver 130 and 160 ppm, respectively. The Valezus model delivers 320 cutsheet color ppm. This unit is modified with a perfector device that yields duplexed output without impacting the rated speed.”
Xerox introduced the Baltoro HF last year. The production color inkjet printer produces output speeds of up to 271 A/4 and 276 letter images per minute (ipm) duplex or 197 A/4 and 182 letter ipm siplex. It is recommended for volumes of 750,000 to 3,000,000 images per month. The cusheet press prints to uncoated plain, inkjet treated, and inkjet coated paper.
Drying Functions
The ability to quickly dry affects quality and speed. Several advancements are new to cutsheet inkjet printers.
The Canon varioPRINT iX-series utilizes a two-step iQuarius drying technology and media transport system. The first step is hot air impingement that evaporates water from the ink on the print. The second drying step is heat combined with humidification for robust ink layering so prints can be cut, stitched, perforated, and folded without issue.
Pierce explains that the dryer is more important when aqueous-based inks are used and as speeds increase. In the case of the J Press 750S the entire dryer section of the press is engineered to allow for increased throughput. Heated rollers and heated air circulating within and around the dryer cylinder were incorporated in addition to the use of some IR lamps. “The result is a faster drying design, with a smaller footprint from previous generations and a reduction of electrical consumption by 23 percent.”
With the LED UV inkjet technology of the Konica Minolta AccurioJet KM-1, ink is instantly cured, requiring zero time and no need for inline drying, according to Troxil.
Mansfield points out that ink formulation impacts drying requirements. He says many inks used in drop on demand printheads require higher levels of humectants or wetting agents than inks used in Kodak’s continuous inkjet technology printheads. “The low humectants in Kodak’s proprietary water-based inks enhance drying, offering better compatibility on otherwise challenging substrates.”
According to Stratton, some cutsheet inkjet machines use solvent- or water-based inks that dry via oxidation/evaporation. Ink manufacturers continue to update the formulations of these inks to speed up the process of the solvent’s evaporation. “As is known with conventional offset solvent inks, these are not the ‘greenest’ options because they evaporate into the air, releasing volatile organic compounds. Some inkjet presses are adding inline or offline IR drying systems to accelerate the oxidation/evaporation process, particularly needed to turn the sheet over for reverse side printing,” he explains.
Komori engineers have experience with solvent- and oil-based conventional ink drying, as well as energy curable conventional UV, H-UV, and LED UV systems. “Using energy-curable inks provides an immediate cure of the inks that allows for the press to immediately turn the sheet over and print the reverse side with no marking to the print on the first side. To avoid the ozone and heat that takes place with conventional UV systems, and to allow for the most compact and energy efficient method of energy curing, LED UV was chosen as the curing system for the Impremia IS29,” says Stratton.
Toole sees modularity for drying options popular for cutsheet inkjet. “Some manufacturers use IR technology and air circulation to enhance drying for coated stocks, while others with low-cost drying are tailored to uncoated stocks. In the future we expect to see manufacturers with options for industrial-style drying along with options for light drying requirements. The benefit of cutsheet is the ability to have multiple options without burdening customers with options they don’t need.”
Heindl says the addition of resin to RISO inks reduced bleeding into the media and improved on what is already a fast-drying, oil-based ink.
Media Path
In addition to drying mechanisms, the paper path is an essential consideration for ensuring productivity.
The Canon varioPRINT iX-series features a seamless, stainless-steel belt with small perforated holes and air suction to accurately position sheets to transport at high speeds, allowing for a combination of papers with proper registration. Further, sheets with deformations are automatically detected and discarded before entering the print process.
“The J Press 750S is built on an offset frame using the same gripper system and paper path. Using a robust vacuum feeder, the paper path is quite simple and does not introduce the pitfalls and registration challenges associated with using multiple paper drawers,” offers Pierce. Even running at 3,600 23×29.5-inch sph, he says the J Press “barely challenges the capability of the offset frame it is built on.”
The AccurioJet KM-1 inkjet press is designed to efficiently and reliably move all types of media through the printing process. “Because of this, we can run media from light-weight offset stocks up to 24 pt board with no complex changes on the press. The media path uses a feed and gripper guide system—just like offset,” adds Troxil.
When implementing a cutsheet hybrid solution for a customer, Kodak engineers mount the PROSPER printheads within the host press or finishing equipment’s paper path, preserving the simplified design of the analog equipment.
To produce the best quality product, Stratton believes a cutsheet inkjet machine must exhibit excellent side-to-side and sheet-to-sheet registration. “The lack of precise registration shows up when printing and then again when folding and/or trimming the final product. Visually evaluating perfect bound/saddle stitched books or brochures can show that simplified media paths designed to accurately register side-to-side and sheet-to-sheet may not give the most accurate registration,” he offers.
Like its sheetfed offset presses, Komori’s Impremia IS29 has a media path that provides accurate registration of each sheet through a path that begins with the feeder, aligned to the print cylinder/printheads with an offset-based side-guide, and transfers sheets using offset style, gripper-to-gripper sheet transition cylinder-to-cylinder through the press to delivery. For sheet turnover, the internal reversing device is a Komori perfecting device, giving an accurate, offset-like, side-to-side alignment for front-to-back register.
Toole says the imaging process related to inkjet technology helps simplify paper paths compared to toner-based digital technology. “Without the need to charge paper, drums and transfer charges and images and toner, the paper path for inkjet systems is inherently simpler. This helps certain devices handle substrates that were previously untouchable by digital presses—specifically, packaging board, thick plastics, and heavy paper board,” he shares. “The simple paper paths corresponding to many cutsheet systems also provide great benefits for finishing. Traditional drying drums “can be effective in driving water out of the sheet, they can also in-duce curl into the product—and hence, more complexity related to de-curling or challenges in the bindery department,” Toole comments.
In the example of RISO’s patented FORCEJET technology, Heindl explains the press design allows for printheads to remain fixed while generating the image on paper. The 24 printheads are aligned in a compact manner that allows for a very short paper path.
Expanded Opportunities
Cutsheet inkjet presses continue to advance in quality and productivity, making them well suited for a range of applications, including the commercial print space. dps
Jul2020, DPS Magazine