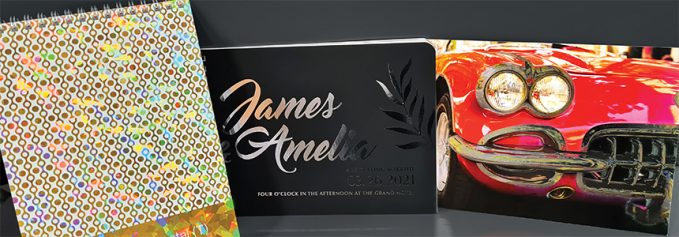
by Cassandra Balentine
Print providers want to go beyond CMYK to move away from print as a commodity while adding value and profit.
Above: Skandacor offers a full line of equipment for applying embellishments and specialty laminate films.
“Printers are looking for ways to add perceived value to their products and make their print stand out—whether it be a book cover on a shelf, high-end packaging that reflects the quality of the product inside, or marketing materials that reflect brand quality—the end customer wants to improve perceived value for their products and brand,” says Oran Gilmore, director of sales and business development, Autobond Laminating, Spot UV, and Foiling Machinery.
A variety of finishing processes embellish/enhance print across all segments, including digital embellishment, lamination, spot coating, embossing, hot and cold foiling, and even die cutting.
Neil Drever, product consultant, Skandacor, sees new ways these tools are used almost daily, making seemingly endless options and opportunities for digital print enhancement. “This being said, the most common uses we see are in packaging—to add product value or make it stand out or on the shelf—and in business cards, greeting cards, etc. Basically, anything needing that luxurious look and feel.”
Several vendors offer solutions that embellish or enhance a print, from spot coating to embossing. We highlight just a few examples here. Visit dpsmagazine.com/webinars to access our archived webinar on the topic.
Digital Embellishment
Digital embellishment is an emerging area for print enhancements.
“With this technology, the classic traditional finishing applications are more profitable because much of the production costs have been removed—dies, outsourcing, time, makeready, etc. Likewise, the new applications increase revenue streams because in many cases they are based upon expansion of both existing and new customers,” says John Dembia, manager, product marketing – Industrial Print Products, Konica Minolta Business Solutions U.S.A., Inc.
Konica Minolta’s latest introduction to this space is the AccurioShine 3600 Multi-Substrate Digital Press with iFoil One option. The device enables in-house spot UV varnishing without the need for screens, plates, or dies.
Another popular digital embellishment provider is Scodix. The company offers a number of unique applications that give print providers a competitive edge among many industry segments such as packaging, web to print (W2P), publishing, and commercial print by leveraging technology and software for their specific needs.
The Scodix Ultra 1000’s Series of Presses offers up to nine enhancement applications on a single press for A3 to B1/41 inches sheet sizes.
“Scodix application embellishments include foil, raised polymer, decoration on metallic substrate, variable data, cast and cure, glitter, braille, metallic, and crystal. These embellishments can be combined, such as polymer-on-foil, to produce incredible visual effects that mimic embossing/debossing that are typical with traditional foiling processes,” states Mark Nixon, VP sales and marketing, Scodix.
Presses in Scodix’s Ultra series print up to B1 sheet size and can promote software that enables an integrative W2P platform solution.
“Since Scodix is a digital process it can print any size run at any time. It saves valuable time and labor for set up, excludes the usage of heavy metal dies traditionally custom made for jobs, and eliminates the usage of caustic chemicals and solvents. This helps print providers provide visibility in the workflow process to their customers of their sustainability efforts,” offers Nixon.
Inline/Nearline Embellishment
In addition to standalone solutions for embellishment, many digital and hybrid print engines—for both label and commercial printing—offer inline enhancement tools, like varnish.
“An embellishment process can increase the value of a label and provide a premium feel to an otherwise normal label. A digital embellishment process can increase the value of a label without the required time and resources that are needed for a similar analog embellishment process,” says Mike Pruitt, senior product manager, Epson America, Inc.
For example, the Epson L-6534VW UV digital label press comes with CMYK + White and a clear ink called Digital Varnish (Dv). “The Dv has three primary uses, both matte and gloss spot varnish, simulated foiling on metallic substrate, and raised embossing. The clear ink can also be used for other security applications, like digital watermarks,” he offers.
The Dv used on the Epson L-6534VW is printed inline with the label—all in one step, and is standard on the press.
“An inline digital varnish can be used to create spot varnish effects, tactile printing, or simulated metallic foils. Rather than creating and mounting multiple plates and preparing multiple ink stations, Dv can be controlled via software, eliminating plate costs and reducing makeready and clean-up times drastically. The digital application of these premium features results in higher values per label and enables embellishment to be offered for short-run sizes, without significantly increasing the burden on the production operators,” comments Pruitt.
He points out that a press that can print white, CMYK, and Dv during one operation in a single pass can be beneficial to shops looking for a solution designed to streamline operations, run print production effectively, and most importantly, deliver quality, differentiated labels for both large and small runs without the need for an expensive analog plate or long lead time.
Nilpeter offers label solutions with inline embellishment. It recently added High-Build Varnish and High Opacity White inkjet units to its portfolio, which John Crammer, sales consultant, Nilpeter USA Inc., says are well received in the market.
“The High-Build Varnish InkJet Unit offers extensive embellishment capabilities perfect for requirements in the health, personal care, wine, and spirits segments—to name a few. Similarly, the easy-to-use, time saving, and cost-efficient High Opacity White InkJet Unit allows you to increase shelf appeal and break into new markets,” says Crammer.
He points out that both units are seamlessly integrated or can be retrofitted on any Nilpeter printing press. The High-Build Varnish and High Opacity White InkJet Units offer a unique opportunity to align the operation of traditional analog and digital inkjet printing processes.
Furthermore, he says both units provide a lower overall cost of production, less material waste, faster makeready, and increased production rates compared to traditional methods.
Coating and Laminates
UV spot coating is a popular option for adding embellished effects to digitally printed output.
Autobond manufactures a range of inkjet spot UV machinery from 14×20 to 41×41 inches, available both as standalone digital embellishment machines utilizing a Heidelberg feeder, or more commonly configured inline with new or existing Autobond laminators.
“Autobond delivers the ability to inkjet spot UV inline with laminating to enable customers the ability to laminate, inkjet spot UV—either flat or raised/textured UV, with the option of foiling all in one system. “In this way, our customers streamline these finishing processes on one system with a very quick makeready. Users really appreciate the higher productivity—at up to 60 meters per minute on flat UV, more robust build quality, and minimal maintenance requirements. They also appreciate the relative lower cost of ownership and inexpensive varnish we developed with an ink partner specific for this system,” says Gilmore.
He says spot UV, especially when applied over a high-end laminate such as Soft Touch, exudes quality, and increases perceived value of the printed product. “Further, there are many printers that have run traditional screen press equipment or sent out to finishers running traditional screen press equipment. In either case, screen making and make ready times associated with screen technology increases cost. Especially, for digital printers it does not fit with their print on demand business model. Therefore, there is increased demand for inkjet spot UV coating/digital embellishment machinery in the digital market.”
Duplo introduced the DDC-810 Raised Spot UV Coater in April 2017. “The machine was an immediate success as it was the first affordable raised spot UV coater that catered to the small- to medium-size printer. Along with it being affordable it did not require high power consumption, a temperature-controlled environment, or any additional costly buildout,” shares Bob Massa, national production finishing director, Duplo USA, Corp.
The company also offers the DFL-500 Dry Coat/Foil/Laminator and is often sold along with many of its DDC-810s, providing printing businesses with a variety of embellishment options.
Duplo recently built on the success of the DDC-810 with the launch of the DDC-8000 B2 Dusense Raised Spot UV Coater earlier this year. “The B2 Dusense is Duplo’s first machine to enter the B2 market,” notes Massa.
The B2 Dusense has many of the DDC-810 features, such as ease of use; Duplo’s patented Air Management System; PC Controller software; barcode reading for automatic file loading; dual camera system that corrects for stretch, skew, or shrinkage; and a compact design. The B2 Dusense offers a modular design that can grow as a print provider’s needs change.
Further, the addition of a Surface Treatment Unit enables operators to need only one polymer, regardless if the output is offset—digital, or inkjet. Another benefit is the ability to do a ten micron build, which Massa says is popular in the packaging industry.
The B2 Dusense also offers an optional inline cold foiling unit. The advantage of cold versus hot foil is the elimination for the need to laminate the stock first, saving both time and money. The B2 Dusense also has the ability to perform cast and cure coating.
A variety of lamination films are utilized to add embellishments to digitally printed output. These also lend themselves to the process of sleeking.
“Most would agree inkjet spot UV looks superior when printed over laminates. At a functional level it eliminates the variability of inks, coatings, paper, dyne level, and other factors that may impact print quality of inkjet UV inks and provides a nice printable surface. Therefore, digital embellishment technologies have driven further demand for lamination,” offers Gilmore.
Skandacor offers a full line of equipment for applying embellishments and specialty laminate films.
“Most importantly, we work directly with print providers to increase adoption and grow their profits with print embellishment,” notes Drever.
The company also offers an extensive line of SPECIALTYpro laminates, ranging from SOFTpro to DECOpro Wood, in addition to SLEEKpro foils in almost every configuration from gold to crystal red. “Our flagship machine—the PODTopic laminator series—is capable of doing the specialty laminates and all the SLEEKpro foils with very high-quality results. As our main entry-level machine, it is ideal for anyone looking to dip their toes into the embellishment market or build a customer base for high-quality print,” adds Drever.
He points out that Skcandacor has offered digital print enhancement/embellishment products for a few years now, and learned many things about what can and can’t be done with the process. “With the current, exploding market of print enhancement and embellishment, new players are regularly entering the market and going through the same growing struggles we had. So we’re ahead in this regard because having this experience has led us to re-tool our equipment and supplies to overcome these obstacles,” he shares.
Cast and Cure
Cast and cure is a decorative coating process that integrates casting and curing techniques to produce ultra high gloss, matte, and holographic finishes on a variety of substrates. “This is a process in which a decorative, clear holographic pattern or matte finish is applied to a printed substrate—from paperboard and paper to labels, flexible plastic, and even mylar balloons,” explains Tim Cain, president, Breit Technologies.
The cast and cure process is simple, explains Cain. First, a UV coating is applied to the substrate, then casting film is nipped in contact with the wet varnish. UV light passes through the casting film and cures the varnish while the film holds the varnish in the desired shape, much like a mold. The film is then delaminated and separated from the printed web or sheet and is carefully re-wound so it can be used again. The process leaves behind a micro-embossed shape in the coating’s surface that can be holographic, matte, or a texture.
“Unlike laminated holographic board or cold and hot foils, cast and cure film can be reused up to a dozen times—and sometimes even more. This means there is a significant cost savings in terms of the amount of film needed for any given job. Moreover, less film means less money spent on shipping fees and warehousing,” he offers.
The cast and cure process is also eco-friendly in that it does not use any adhesives or metals, so it won’t affect the recyclability of the label substrate used. “That’s great news for brand owners with a corporate sustainability strategy,” says Cain.
Cast and cure is used everywhere from liquor and beverage labels to printed collateral and direct mail, magazine and book covers, and even food and pharmaceutical cartons. “Brand owners find cast and cure’s holographic patterns an excellent way to grab the consumer’s attention. Since it is transparent, the printed graphics and text is easily readable,” adds Cain.
Hot Foil Stamping
One tried-and-true area for offline embellishment is hot foil stamping. The process utilizes a die along with heat and pressure to release foil to a compatible substrate.
OR Printer USA is a hot foil stamping equipment provider focused on offering more accessible hot foil solutions, meaning you do not need prior experience to produce high-quality foil images or lettering on a variety of products. “Simple menu controls allow you to easily adjust the temperature, timer, and other settings. Our stamping machines can also store up to 20 settings so users can quickly switch back and forth between projects,” notes Geza Solar, CEO, OR Printer USA.
One area that sets OR Printer’s hot stamping products apart is its ability to tackle thick media. “Even with foil sleeking or digital metallic inks on the market, there is no way to hot stamp on surfaces or media with thicknesses up to 2.5 inches in height, that being said our machines do not compete with digital machines or other kinds of foil transfer machines. With OR Printer machines people can stamp, deboss, or emboss materials or stamp on really thick like a finished book. Hot stamping on finished materials is a big advantage over digital machines,” shares Solar.
Stepping it Up
Increasingly, finishing solutions add value to printed pieces. From traditional hot and cold foiling and cast and cure options through to UV spot coating and varnishing and full-on digital embellishment systems, print providers have options to enter and master the art of embellishment.
“As more digital embellishment tools become available, the awareness of the process is becoming mainstream, driving the uptick of short-run, high-end print. It offers agencies, designers, and brands more flexibility with what they can accomplish, giving print the extra pop that it deserves. For printers, it de-commoditizes regular print on paper, adding the extra margin that is not always easy to find,” adds Drever.
Learn more on the topic of embellishment at dpsmagazine.com/webinars.
Sep2022, DPS Magazine