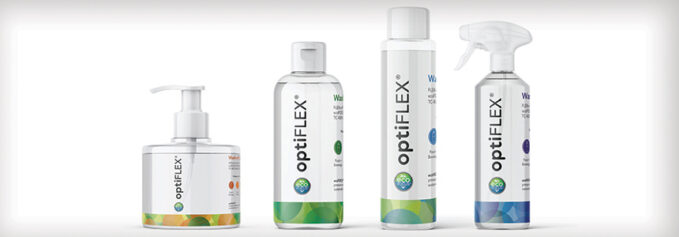
by DPS Magazine Staff
As environmental concerns continue to make headlines, consumers and business owners search for ways to reduce waste and make products more sustainable. Labels/packaging is one area that can create added waste. However, media providers are diligently working to find solutions.
After a product is purchased, used, and placed in a recycle bin, it is sorted at a material recovery facility before being shredded and chopped into small pieces at a polyethylene terephthalate (PET) reclaimer, shares Dan Riendeau, strategic business unit manager, packaging, FLEXcon Company, Inc.
Some modern label materials are designed to easily debond from the packaging they adhere to, which helps the process of separating recyclables.
Melissa Harton, marketing manager North America, Fedrigoni Self-Adhesives, explains that debonding occurs when a container is processed utilizing a water temperature of 88 degrees Celsius/190 degrees Fahrenheit or higher with an alkaline solution.
“Container pieces receive a warm caustic water bath where the labels wash off and float to the top while the container pieces sink. The container pieces then start their journey to becoming a new container, free from adhesive and label materials,” adds Riendeau.
Christina Barajas, sustainability manager, Mactac, points out that PET has a density of 1.38, so labels need to be formulated in a way that the adhesive will cleanly remove from the PET container during the wash process at a materials recovery facility and float, so they can be skimmed off and leave behind a clean PET container.
“This sink/float recycling process cleanly separates the label from the container and PET flakes. The PET fragments, now clean and free of residue, can be used in a PET bottle-to-bottle recycling process,” comments Harton.
Debonding Demand
As consumers become more environmentally conscious, they drive demand for eco-friendly packaging.
“In fact, according to research by Trivium Packaging and Boston Consulting Group, 74 percent of consumers are willing to pay more for items in sustainable packaging, and 60 percent say they are less likely to buy a product in harmful packaging. In addition, many consumer brands have committed to the U.S. plastic pact, which addresses key challenges. One commitment is to make 100 percent of plastic packaging reusable, recyclable, or compostable by 2025. This is a lofty goal for most brands as according to the U.S. Plastics (USPP) annual report, only 36 percent of plastic packaging put on the market from USPP activators by weight is reusable, recyclable, or compostable. Their goal is to reach 100 percent by 2025. This is going to require brands to start looking at more options to help enable the recyclability of their PET containers,” offers Riendeau.
“One of the keys to a truly circular system is having enough ‘clean’ material going into the recycling stream to allow for high-quality materials to be made from recycled content on the backend,” agrees Harton.
James Allen Howell, product manager, UPM Raflatac Americas, says because PET plastic packaging is lightweight and economical to manufacture, it is in high demand.
“Although PET has the highest recycling rate among plastics, less than half is collected for recycling and the vast majority that is recycled is downcycled because it is not suitable for turning back into bottles or food containers. This can be due to the labels not separating well during the recycling proecss. As more global brands seek recycled content in their packaging materials, label choice becomes critical.”
Due to the increasing focus on sustainability and the need to reduce waste, Harton also sees a growing demand in the packaging industry for debonding of non-recyclable materials from containers before recycling. “When non-recyclable materials are included in the recycling stream, they contaminate the plastic flakes. Contaminated flakes cannot be used to make products that include post-consumer content.”
There is also increased demand for recycled PET (rPET) versus virgin resin PET in the marketplace. “Having a label solution that will cleanly debond from a PET container is a critical step in the PET recovery process,” comments Barajas.
Consumers expect more from brands when it comes to their overall environmental impact, shares Harton. “Therefore, brands demand more from their label material suppliers, which pushes the industry as a whole to find solutions.”
Certified Solutions
When it comes to sustainable media options, certifications help provide confidence in the process.
One certification is by the Association of Plastic Recyclers (APR) Critical Guidance, which provides recyclability of PET and high density polyethylene (HDPE) offerings.
The APR offers certification of certain label materials that meet its critical guidance protocols. “The APR has also published container labeling guidelines to help ensure recyclability. The Sustainable Packaging Coalition offers brands The How2Recycle Guide to Recyclability, which provides clear messaging on whether a package is recyclable or not,” offers Riendeau.
Barajas notes an increased need for APR Critical Guidance tested solutions for white or clear biaxially-oriented polypropylene (BOPP) offerings.
Barajas says the Mactac PUREfloat offering provides no adhesive residue during the PET washing process.
She explains that this differs from HDPE, where the preferred guidance is for the label to stay on the container, but being recycling compatible, of which Mactac has both hot melt and acrylic APR Critical Guidance HDPE label offerings for its customers.
Fedrigoni Self-Adhesives’ Ri-Move PET products are also certified by the APR. Ri-Move PET’s AR842 adhesive provides debonding of non-recyclable label materials from PET containers, making them recoverable. “APR certification means that plastics using label materials from Fedrigoni Self-Adhesives were subjected to the industrial recycling process. After undergoing the recycling process, the labels were evaluated and certified as compatible with industrial recycling,” comments Harton.
UPM Raflatac’s SmartCircle RW85C Wash off products are recognized by the APR as meeting or exceeding its Critical Guidance testing requirements. Available as clear, white, or silver metalized film face materials, these labeling solutions add sustainability benefit when paired with UPM Raflatac’s PCR liner—featuring up to 90 percent post consumer recycled content.
Finding Success
Common PET labeling applications include bottles, clamshells, health and beauty products, food and beverage packaging, and household goods, notes Barajas.
At this time, Harton says any product in a PET container can successfully utilize its Ri-Move products as they are specifically formulated to cleanly remove from PET containers. The product inside of the container does not impact the ability of the label to be removed during the recycling process.
Riendeau says BOPP is one of the best label materials to use for debonding from PET because it is lighter than water and will float to the surface. “This allows for the label material to be screened off during the reclaim process. Otherwise, it would contaminate the clean rPET flake.”
Alternative Considerations
In addition to media solutions that debond, there are benefits to an alternative method, in-mould labeling.
The idea behind in-mould labeling, according to Louis Rouhaud, global marketing director, Polyart, is to use a label made of the same material as the container itself to have a mono-component container that is easy to recycle. “The concept is to place the label inside the mold at the time of production of the container/bottle. This is an efficient labelling technology as it optimizes the process and energy of forming the bottle/container to affix the label. This also avoids a second energy consuming step of offline labeling.”
Moreover, there is no additional glue required to bond the label to the container, avoiding further contamination and decreasing the quality of the recyclate.
Rouhaud points out that in-mold labels are liner-less, thus avoiding millions of square meters of liner that are most of the time landfilled. “It is a very efficient, and globally sustainable labeling technology.”
Sustainability Gains
Media and adhesive suppliers are working diligently to create sustainable solutions, including debonding label solutions as well as in-mould options.
Rouhaud says the demand for recycled material is high as in some states, like CA, where the law is already requiring that containers contain some recycled material.
“This requirement will increase, and by 2030, it will also be a requirement in Europe; and this will keep on rising; to achieve that, we need good quality recyclates, thus organizing recycling loops, harmonizing containers, and generally speaking, designing containers and their labels to be easily recyclable,” he comments. dps
Jul2023, DPS Magazine