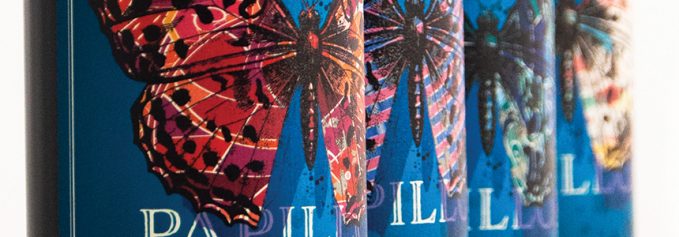
Part one of three
by Cassandra Balentine
The print production lifecycle offers many opportunities for automation. Tools focus on specific stages throughout the process and often support integration.
Shown: Xeikon VariOne is a variable data generation tool for Xeikon’s X-800 digital front end.
A variety of software and middleware tools enable print environments to check and optimize PDF files from the customer, automatically impose multiple products and forward the imposed file to the workflow, or communicate a file to the customer for approval.
However, Tomas Van Rossom, GM, Enfocus, believes that real automation is obtained by software that combines and automates tasks. “It also enables the user to automate the print production processes’ administrative functions, which are often forgotten. The automatic transformation from offer to order, validation, job onboarding, communicating with shipping couriers, and generating invoices with real automation is achieved by processing these repetitive tasks driven by the integration.”
Defining Automation
Varied levels of automation exist within a production workflow. It is easier to digest when broken into smaller pieces.
Marc Levine, director of business development, GMG, divides automation into two segments within print production—software-to-software and software-to-hardware integration.
Software-to-software tools are designed to allow applications to talk and exchange data intelligently.
“This typically includes a backbone platform called a workflow that understands the notion of a job and can orchestrate the process of passing artwork, for example, to a series of connected software agents that do special tasks,” he explains. For example, a workflow might send a file to a color server to either be normalized into a standard workspace or separated into the final print condition automatically.
For software to hardware tools, applications need to interact automatically with the hardware to automate tasks that would typically be done manually. “This naturally increases process speed and reliability,” says Levine.
Some printing presses have an onboard color measurement device that may be used to keep the device color consistent by measurement and correction. “Software-to-hardware tools connect to these measurement devices, automatically print and measure control strips on each print, and ensure that the color of every print is consistent and accurate,” he explains.
To match the standards needed to achieve a level of Industry 4.0, Marc Raad, president, Significans Automation, says fully conditional and integrated workflow software solutions like Enfocus Switch, Esko Automation Engine, or Hybrid Software are needed as a foundation.
This base creates integration opportunities between workflow automation and business systems like a management information system (MIS)/enterprise resource planning (ERP), web to print (W2P)/ecommerce platform, or customer relationship management (CRM).
“Additional best-in-class software solutions from companies like Tilia Labs, InSoft Automation, and Ultimate Technographics facilitate added automation steps in the process for planning, layout/nesting, and estimations,” comments Raad.
He points out that advanced preflighting can be facilitated through software like PitStop powered by Enfocus or pdfToolbox by Callas software.
“Ultimately, all and any of these best-in-class software solutions can streamline operations towards minimizing or eliminating touch points with an expert level of customization and optimization in the form of integration services,” concludes Raad.
Communication for Automation
A common theme across all conversations of automation is communication—specifically integration. “Different levels of automation can be seen in all processes leading up to print from data ingestion to job production,” shares Ryan Semanchik, president, Transformations, Inc.
“A number of solutions add automation to the print production process. Whether you are looking to reduce manual tasks within the design process, manage color, or streamline your impositioning and estimating processes, several tools are available,” echos Carissa Smith, marketing director, Tilia Labs.
It is also important to remember that silos of information may exist. “The trick is to bring together the islands of expertise,” shares Graham Blanks, director of business operations, North America, DALIM Software. “A printer must be able to type once and make the information available to many. Several solutions address automating tasks, but the key thing is how to leverage them in the most efficient way—via integration.”
Many print environments still need integrated automation that provides a continuous, end-to-end workflow and optimization capabilities, agrees Jonathan Malone-McGrew, CMP, G7 Pro, senior director, engagement, Solimar Systems. He says automation is seen less in estimating/scheduling, prepress, color management, and inventory management, but those areas are growing.
Blanks points out that CIP4 has been the advocate of the XML-based JDF standard. “Years after its birth, the dream of JDF is a challenging goal and is still being refined. Concurrently, software developers continue to develop modern, API-first solutions to make integration easier and simpler for vendors of different solutions. JDF is a large specification and is an attempt to map all the requirements of different print systems based on what they each need.”
Tools of the Trade
From order entry to post-processing, workflow automation tools help streamline the print production lifecycle.
David Lunardi, VP of sales, OneVision, points out that automation workflow is based on functions for filtering, sorting, and routing files based on metadata.
“The most automated part of workflows tends to be W2P, document composition, imposition, output management/post-composition, MIS/ERP, and data analytics,” states Malone-McGrew. He says that while automation is available, it doesn’t mean that each area is consistently automated in individual production print environments.
On the front end, particularly with jobs that are reasonably rote or repetitive, automation starts with order entry. “Typically, CRM will get involved in describing the job in MIS/ERP systems. This provides not only job specifications, but can trigger the workflow to operate in a particular way,” explains Mike Agness, EVP, Americas, HYBRID Software.
Then you get to artwork approval and production software. Preflighting will assure that all the pieces of a job are available for processing correctly. “This could include editing software to fix problems in the file—or to make customer-requested changes; or AAs. Automated print production takes the file and prepares it for the press—traditional or digital. Color management will get involved to assure the job’s colors are printed correctly, no matter the output device. Often a layout optimization application will prepare the plate or print job to save as much resources and materials as possible,” explains Angess.
Amanda Newman, head of marketing, Tharstern, says the most common areas for automation include estimating, job management, shipping, purchasing, and financials. “Other companies, perhaps those that are a little bigger or have more complex workflows, also want to automate areas like scheduling, inventory, picking, and packing.”
Over the last few years, Newman notices a rise in demand for CRM integration with marketing software to help better align sales and marketing teams to target the right audience with the right products.
“We find that most areas have been automated within companies. Perhaps packaging companies require greater time-to-market efficiencies to compete. Maybe it also has to do with quality or error reduction. However, we find that W2P, prepress/preflight, color management, estimating/scheduling, MIS/ERP, document composition, imposition, output management, post-press, and inventory management systems are commonly implemented,” offers Agness.
A great deal of automation occurs when you tie a W2P system to a comprehensive MIS system. “The orders then become no touch until ready to print, as in a digital workflow. The job ends up on the queue for the machine that will produce it,” says Jack J. Lafler, VP of sales and technology, HiFlow Solutions.
Another common area of automation is estimating. Estimating and quoting can be greatly expedited with an MIS, meaning less labor in creating an estimate and a quote, shorter turnarounds, and improved client experience. “Scheduling systems that are part of an MIS and use rules-based automation can greatly optimize the production capabilities of a company, saving time and money,” comments Lafler.
Analytic Solutions
Workflow tools gather and utilize data, which can be invaluable to a variety of organizations. Data and analytics are part of a sophisticated MIS and provide real-time information that identifies costly errors so that they can be quickly corrected. “Data automation gives management the tools needed to grow a business and make informed decisions,” shares Lafler.
“A vast amount of really useful data is within an MIS, and I still don’t think the majority of companies with an MIS are making the most of it,” agrees Newman. The software contains data from every facet of the business—from sales, marketing, and estimating right through to delivery, and everything in between—and yet it’s still not exploited as much as it should be.”
This is where business intelligence tools come in. “We try to encourage our customers to use a business intelligence tool to do this, whether that’s provided by ourselves or by using third-party artificial intelligence (AI) tools like Power BI or Qlik,” explains Newman.
These tools analyze information from multiple software applications and highlight trends and connections between the data. “The one piece of analysis we try to push our customers is to create a BCG matrix using the historical order data from their MIS, so they can see which of their products and target sectors are making them the most profit,” says Newman. “Often the results of this analysis will have changed because of the pandemic, so it’s more important than ever to carry this out and reassess sales and business strategies based on the results.”
Room to Grow
Because there are so many opportunities and levels of automation, some areas stand out as being more quickly adopted while others trail behind.
For mid-level adopters, Raad says depending on the technique, it may be common to have manual workflow interventions at certain intervals of production that combine with workflow automation. This practice is commonly observed where there is complexity in the files that require the attention of a skilled prepress operator/artist.
“Amazingly, one of the largest gaps in automation resides in the still very manual process of client job approvals, which can be fully automated electronically via a web portal for example. In most cases during many of our engagements, automation is underutilized and presents a huge opportunity for improvement,” admits Semanchik.
One area he feels automation is underutilized is in combining like jobs. “Cleaning up data, preprocessing activity, combining files, and optimizing print output are typically repetitive steps that take place prior to print. Automating these steps and combining jobs makes it possible to gain better postal rates and a more efficient use of run time on the production floor. The goal of an efficient workflow is for a file or files to enter the system and show up ready to print, fully optimized without the need for human intervention.”
Danny Mertens, corporate communications manager, Xeikon, believes that printing workflow software itself could stand to be automated more, as all software packages available target different parts of the production floor. This causes inefficiencies that could be solved through a single, shared workflow package that eliminates the borders between client, prepress, operators, and production managers.
Other common underutilized areas include inventory integration for postal configuration and verifying quantities on demand, producing optimized print output based on file size or equipment capacity, or even the automation of report creation and delivery, comments Semanchik.
“Areas that we find less often utilized include CRM, data analytics, and content management. Perhaps this is because these are not 100 percent directly tied to production. These are important tools in their own right, but more to serve customers, offer a marketing service—in the case of content management, and help printers improve their processes,” notes Agness.
Blanks says it’s not unexpected that most printing companies look at the printing press, as the most important facet of production. “It’s what dictates the quality and speed of their work. Then they build around the press. How much does this cost and what can I charge? How much am I making?”
However, he feels that somewhere in middle are the tasks necessary to get the jobs done. “It is not rare to find that it’s the one facet of a company’s operations that senior management care least about. They just rely on prepress experts to solve their problems within their area of focus.”
In the case of labeling, Bob Tilling, VP global sales, Kallik, points out that the least common type is technology to extract content in a digital form from a company’s existing labels or artwork.
Personal Automation
Investing in automation is business specific. Levine believes priorities vary with the type of organization.
“If your business is designed around W2P applications, automating W2P functionality means you will need to look at the commercial workflow pieces as much as the artwork pieces. A traditional packaging business serving color-critical brand customers may need to focus more on building a sturdy, automated color management workflow or even automating the print quality management process to match color with high-performance consistently.”
“We suggest providers start automating at intake, which can feed points further down the stream,” says Adam Homsi, founder, InkCloud, admitting areas of automation depend on the type of operation.
“Every environment and organization are different and priorities change over time and by job,” agrees Ernie Crawford, president/CEO, Crawford Technologies. “Currently, the most important area is the one that utilizes the most staff and tribal knowledge. As we exit a pandemic, it has become clear that you cannot rely on a specific staff member or team to be at work on a given day. If that staff member is not there, can the job be processed, printed, and shipped or mailed? Do you have a documented process for each job? Is every employee backed up by multiple people? All too often we hear about production sites losing staff to Amazon and Target as minimum wages increase; you do not want your production to stop, or even worse be incorrect, because of a single person.”
Smith suggests taking a strong look at overall processes and identifying key areas creating the most time or errors. “Less manual touches not only lead to speed, but also provide better output in the end.”
Therese McGady, marketing manager, Aleyant, agrees, recommending that companies first figure out what their biggest pain points are and then automate that area. “Automate your most routine work so that you can spend your time and resources on larger jobs and more profitable work.”
Automation often means streaming variable content as required, including aspects such as the batch number direct to the end-of-line printing process, shares Tilling.
Finding Automation
Workflow automation is increasingly important. The right tools can streamline production processes and eliminating manual touch points.
The role of workflow in a print production environment is vast and complex. We tackle workflow automation in a three-part series. Stay tuned to our September and October issues for more. Also check out dpsmagazine.com/webinars for archived and upcoming webinars on this topic. dps
Jul2022, DPS Magazine