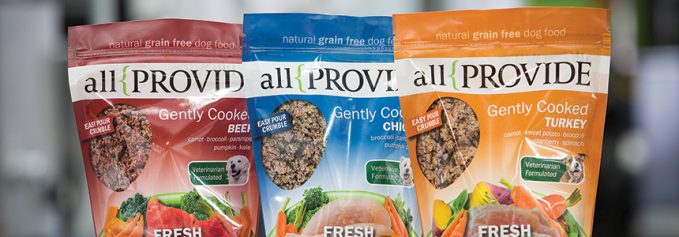
By Melissa Donovan
It’s important to invest in trusted technology, especially when at the forefront of the next big innovation. Once predominately produced via flexography, flexible packaging benefits from increased advancements in digital technology. Brand owners and their agencies demand shorter runs and increased versioning at faster times to market—all requirements met by digital printing. Print providers who identify the advantages of digital printing and are able to implement these capabilities in house are poised to offer customers exactly what they want.
Above: ILS is a digital print and packaging company utilizing HP Indigo technology to produce pressure-sensitive labels, shrink wraps, and flexible packaging applications.
Label Converter to Packaging
Innovative Labeling Solutions (ILS) began in 1996 when a family partnership spurred a printing business. Starting as a small, flexographic label converter it now is considered one of the leading digital printers for packaging. It operates out of a 65,000 square foot facility in Hamilton, OH with 120 employees.
Serving North America, the digital print and packaging company offers turnkey solutions for pressure-sensitive labels, shrink sleeves, and flexible packaging. It routinely partners with consumer packaged goods and private label companies from backgrounds in craft beer, wine, nutraceuticals, specialty food, personal care and beauty, cannabis, and household products.
These customers request a variety of flexible packaging applications including stand up pouches, four-sided sealed pouches, packettes, stick packs, and custom shipping mailers.
First in Line
Kevin Bennitt, director of flexible packaging, ILS, admits that ILS was and continues to be an early adopter of digital printing technology. In 2005 it was one of the first companies to venture into the digital segment of label printing. A decade later in 2014, the company implemented the first HP Inc. Indigo 20000 Digital Press for flexible packaging in the U.S.
Adding the HP Indigo 20000 Digital Press allowed ILS to not only grow its product offerings but reach new markets, specifically new industries not yet immersed in leveraging digital print capabilities. Using the new printer enabled the company to produce digitally printed packaging like stand up pouches, pillow type bags, and stick packs commonly used for dried foods, lotions/oils, drink/powder mixes, pet food, lawn care, and nutraceuticals.
“With the need for shortened product lifecycles, the demand for short runs, high SKUs, and quick turns are required. The HP Indigo platform provides the ideal solution to achieve this,” notes Bennitt.
The new machine was an instant success and spurred ILS to add two more HP Indigo 20000 Digital Presses in 2019 and 2020. According to Bennitt, the wide 30-inch web makes them ideal for larger format flexible packaging.
While the company operates flexographic presses in house, for flexible packaging it often uses digital technology. “Personalization, customization, and the proliferation of SKUs are trends that aren’t going anywhere and they’ve been pushing the flexible packaging market forward. The power of digital print technology, with its short runs, versioning, variable print capabilities, and design flexibility positions brands well to respond to these growing trends,” explains Bennitt.
The convenience of fulfilling custom order quantities is also why digital print is so well regarded in the flexible packaging space. “You only print what you need, when you need it, avoiding inventory obsolescence and reducing wasteful overproduction,” says Bennitt.
This has led ILS to offer trial runs, especially when a customer has pre-approved, specified materials on hand. It allows for the material to be validated on the HP Indigo 20000 Digital Press prior to the client committing to a full run. If isn’t up to standard, the ILS team can provide an expert recommendation based on the application.
A Word on Finishing
Aside from the three HP Indigo 20000 Digital Presses, part of what makes ILS’ flexible packaging operation so successful is its finishing department. The company runs two 30-inch wide web finishing presses—one A B Graphic International Ltd. Digicon 3000 and another Digicon 3000 integrated with ebeam’s electron beam (ebeam) technology.
The Digicon 3000 is designed for digitally printed self-adhesive labels, shrink sleeves, flexible packaging, and point of sale materials. Equipped to offer rotary and semi-rotary printing and die cutting to laminating, slitting, decoration, and perforation, the device is fully compatible with the HP Indigo 20000 Digital Press—either operating offline as a standalone solution or inline for printing and finishing in a single pass.
ebeam technology enables ILS to create gloss, matte, and soft touch finishes on flexible packaging. Designed for packaging, the ebeam curing technology lays down a thin layer of coating, which covers and protects the digital inks, as well as the material during the converting process.
Additionally, Bennitt says the ebeam process “cross links” HP Indigo ElectroInk. “This makes the inks more resistant to deformation as a result of being subjected to heat during the pouch converting process. These ultra-low migration coatings are free of initiators, making them the ideal solution for food and cannabis packaging applications,” he continues.
The Digicon 3000 finishing devices are complemented by two Karlville Development, LLC wide web slit rewinders.
Crunchy, Yet Flexible
McCabe’s Granola is a family owned and operated gluten-free granola company headquartered in OH. Recognized as an innovator in its food category, the company grew quickly and introduced several new and unique products in record time. Originally, its packaging was produced using traditional flexography printing, but McCabe’s required more flexibility to alter the design of its packaging as needed.
The solution was ILS and its HP Indigo 20000 digital presses. Switching to digitally printed flexible pouches helped provide McCabe’s with the ability to quickly revise designs while still meeting FDA guidelines. In addition, it was able to get to market faster with its newer products.
McCabe’s also appreciated the influence digital print had on its product versioning. The digitally printed packaging increased engagement by providing different stories on the back of each pouch about the types of oats and grain-less granola offered by the company.
Achieving Success
ILS is an ideal representation of digital printing and flexible packaging success. Ahead of the curve when implementing its first HP Indigo 20000 Digital Press, it built on this investment when it acquired two more presses close to ten years later. These printers—in addition to its finishing lineup—allow the print and packaging provider to meet the needs of its many customers, including McCabe’s Granola.
Sep2020, DPS Magazine