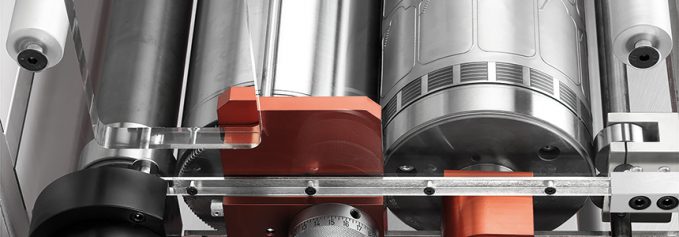
By Cassandra Balentine
The demand for shorter print runs and custom orders are increasing, leading to the adoption of digital print technologies. Digital print providers want to offer the same features traditional clients expect, like die cutting. Several modern die cutters on the market are ideal for digital print environments that must remain profitable on complex, low-volume work.
Above: Kocher + Beck continues its commitment to equipment, employees, and training in order to achieve the high standards and expectations of its customers.
There are many acceptable methods for achieving custom cuts for short runs, including flatbed, laser, and rotary die cutters.
Kevin Chen, product manager, Duplo USA, Corp., says the requirements and specifications of the material, sizing, tolerances, costs, and turnaround time help determine which cutting process is most suitable for a specific environment’s needs.
“Printers have been offering some degree of die-cutting service for many years on legacy equipment like windmill and vertical letter presses. Although much of this equipment is still functional, it is slow, lacking in safety features, and requires a skilled craftsman to run,” shares Don Dubuque, director of marketing, Standard Finishing Systems.
For those without traditional die-cutting capabilities in house, outsourcing is often utilized. “Die cutting presents an opportunity for print providers to offer a unique service in-house and gain control over a previously outsourced job,” offers Chen.
As legacy equipment becomes more difficult to staff and maintain and as an increase in demand for die cut materials makes outsourcing cost prohibitive, many printers look to bring die cutting in house. “Modern, automated die cutting equipment can keep up with the output from digital presses and does not require highly skilled operators,” says Dubuque.
Stand-Out Features
A variety of die cutting options are available to digital print environments.
“Today’s print shops face increasing pressure from customers looking for customized pieces on short as well as longer run jobs. Die cutting—specifically rotary die cutting—allows print shop owners the ability to fulfill unique customer requests while maximizing profits by keeping the job in house. Additionally with the low cost of dies, the per price piece is very affordable to the customer,” comments Russell Carter, director of marketing and product development, Martin Yale.
“Today’s advanced die cutting systems are versatile and handle a wide range of finishing requirements, including die cutting, kiss cutting, scoring/creasing, variable data, perforating, hole punching, and embossing. With such a range of capabilities, these systems are valuable to a many print providers including digital print centers, commercial offset printers, promotional and novelties printers/manufacturers, light packaging and manufacturing providers, invitation and announcement printers, label printers, and financial, insurance, and medical print providers,” says Dubuque.
Chris Raney, VP of Postpress, Heidelberg USA Inc., says many of the latest die cutters have quick makeready features and are easy to operate. For the best registration though look for a machine with an optical registration system. “Traditional die cutters use the sheet edges to register the sheet prior to die cutting; however, an optical system registers the sheet to a printed mark. Thus, optical registration will deliver perfect register on every sheet, regardless of the print to sheet edge position.”
Modern die cutting solutions are quick to set up, easy to learn, and require minimal makeready and floor space. “Combining these efficiencies with the advances in high-speed inkjet and digital technologies opens up a new market in short run and specialty printing, packaging, and labeling,” comments Chen.
“If you look at how efficient the new die cutters are it becomes very apparent that they will make a huge impact on digital printers. Not only are they easy to use, they have a small learning curve and will increase short-run throughput. On top of that you have the option of storing machine set up information in the machine’s memory to help with repeat jobs,” says David Morris, CEO, Kocher + Beck. He says another key area is flexible dies. “Short-run jobs usually mean very fast turnaround times. Flexible dies can be produced within one to two days and shipped overnight for a low cost. This allows digital print providers to maintain short lead times.”
“Rotary die cutters use flexible dies mounted on magnetic cylinders and platen press die cutters use high steel rule dies, each have their advantages and disadvantages in the short run/digital environments,” says Chris Van Pelt, president, Therm-O-Type.
He adds that rotary die cutters require less operator skill and are ideal for kiss-cutting applications, including pressure-sensitive labels and stickers, as well as die cutting. They also cut intricate designs that can not be duplicated with a steel rule die. Rotary die cutting limitations include restrictions on paper thickness and waste ejection from the die when die cutting holes and small cut outs. Flexible die cutting dies are generally more expensive compared to steel rule dies, and if a flexible die is damaged or worn, the die must be replaced. Rotary die cutters are also typically single-function machines.
Many platen presses can be used to flat foil stamp, blind and foil emboss, as well as die cut using steel rule dies. To use all these capabilities, operators require additional training and skills, explains Van Pelt. Platen presses can die cut thicker papers, dies are generally less expensive, and damaged or worn dies can be economically “re-ruled” rather than replaced with a new die. The multifunction capabilities of a platen press are a great advantage for some customers.
Digital label cutters enable the production of precut and finished labels.
“Many of them support laminating and slitting together. Any shape of labels can be finished in any volume, with minimum loss. Entry-level employees can run the machine in reliable quality,” says Juan Kim, CEO, Valloy Incorporation.
Investment and ROI
Investing in new equipment always involves a lot of thought. Consider your current and future needs as well as the projected return on investment (ROI) and total cost of ownership.
Modern die cutters have a relatively low acquisition cost when compared to legacy machines or laser cutters. “Automation also reduces the need for skilled die cutter operators, which can help providers save on labor costs. As with any equipment purchase, it is vital to evaluate if and how a new investment will meet your current and future needs. ROI varies depending on the operation volumes and the purpose for the investment, but we have seen many customers achieve a ROI in as little as one year,” offers Dubuque.
In terms of initial investment, print providers should also budget in the cost of building a library of dies—both monetary cost and time cost. “That being said, die makers are used to quickly producing and shipping out a die, so obtaining the dies isn’t normally a big challenge. At the end of the day, die costs can be passed along to the end user and included in the price of the die cut pieces being sold,” he notes.
The cost of investment for die cutters varies greatly, with vendors suggesting a range from $5,000 to $350,000.
Initial investment depends on the type of digital cutter purchased. “Typical die cutters range from $5,000 to $120,000 depending on the technology purchased, the ROI that is typically achieved is relative to the length of the runs that the customer is running,” shares Chen.
The investment cost for rotary or platen die cutting equipment varies based on a number of factors, including sheet size and technology.
Floor space, electrical, and operator training/skill requirements vary greatly depending on the type of equipment that will be used. Van Pelt estimates that new equipment costs vary, commonly upwards of $80,000 for current models.
David McLaughlin, regional sales manager – South East and Shawn Paul, regional sales manager – South Central, Kocher + Beck, say sheet-fed die cutters start as low as $60,000 and go up to $250,000. “Roll-to-roll die cutters—better known as digital finishing machines—start around $120,000 and can go up to $350,000. Each printer needs to review their business to determine which machine best suits their needs and products produced.
Raney estimates investments to be in the $300,000 range for a well-equipped machine. “The ROI can vary dramatically depending on the amount of work to be processed but can be in the two to three year range,” he shares.
New to You
For those without experience in traditional die cutting, the good news is that the majority of modern die cutters are designed to be very user friendly.
“From our standpoint there are two areas where the operators have a learning curve,” say McLaughlin and Paul. They note that learning computer controls as well as getting familiar with handling and using flexible dies sometimes pose a learning curve. “Operators new to flexible dies need to follow the handling and care instructions. We have seen that companies new to flexible dies will normally damage one of the first few dies used. This often happens during the installation/training of the equipment. After that it is generally smooth sailing.”
Chen feels that the biggest learning curve of any die cutting machine is the technology offered on a specific die cutter. On a rotary die cutter, the processes to setup a machine involve the steepest learning curves. “As mentioned, most die cutter units are easy to setup but a slight learning curve is required if one is not used to the technology,” he offers.
The level of automation on the machine has a significant impact on training. Dubuque says older and manual machines tend to need more investment in training and often require a specialized operator. “However, machines like the Standard Horizon RD-4055 feature greater automation that allows for easy job changeover and simple operation—even for non-specialized operators. There will still be a learning curve, especially for shops new to automation, but it will not be as steep as legacy equipment. In many cases, we have seen new operators become proficient in just a matter of a few days.”
Kim says Valloy products are designed to be compact and easy to learn, and should only take one day of training and a week of practice for an operator to be fully ready to run the machines.
“In case of digital die cutters, the operation is simple,” agrees Christin Park, marketing manager, Valloy Incorporation.
Van Pelt says training an operator to run its RDC-Flex rotary die cutter is normally accomplished in one day. “Usually, within a week of initial training, an RDC-Flex operator can run the machine efficiently, making all the necessary adjustments quickly and correctly,” he shares.
When an operator is trained on a platen press, like the NSF Excel, customers receive training on die cutting, flat foil stamping, and blind and foil embossing so the training period is typically at least three days. “To effectively use the press for all functions, it usually takes a few additional weeks of machine set up and operation,” explains Van Pelt.
“As with every new process, there is a learning curve such as understanding the capabilities of the die cutter, how to lay out a job for optimum processing speeds, etc. What is also important is to find a good, reliable, and experienced die maker to support your operation,” offers Raney.
Laser Alternative
While we dedicate most of this article to automated rotary and platen die cutters, laser cutters are another option for digital print environments.
“Today packaging applications and customers are focused on new market needs like faster speed to market, on demand solutions, more production flexibility, high value add, and smaller production runs. New capabilities create new opportunities and free creativity,” shares Uli Kretzschmar, VP, laser sales, SEI.
He believes that laser cutting is a profitable complement to digital print and creates a fully integrated digital workflow that responds to demands for quick turnarounds, as short as hours.
“True digital finishing and laser cutting does not require cutting dies,” he argues. “The printer streamlines the finishing process and eliminates order or inventory management. You can print and finish from file to ready to ship in hours by eliminating manual changeovers. Jobs and die lines can be generated offline in prepress and loaded into the machine for immediate execution, stored, and recalled when necessary. The integrated quick response code reader allows job change on the fly without stopping the machine for changeovers and with zero waste between jobs. It provides peace of mind and allows users to cut one pieces or a million since it’s easy and quick to setup. The operation is safe and easy.”
Further, Kretzschmar says the flexibility of the laser allows many different operations in one pass—cutting, kiss cutting, scoring, micro-perforating, but also security marking, versioning, and other personalization—making it a versatile tool to finish, customize, and embellish at the same time.
Digital finishers from SEI Laser are modular in design and are configurable to meet specific demands. Kretzschmar says laser cutting can be combined with additional digital and even conventional processes. Investments range from $50,000 to $600,000 USD with a typical ROI of about two years.
Cutting Edge
The draw of digital print technologies includes the ability to cost-effectively produce shorter runs. However, if finishing equipment lacks, then the benefit diminishes. Many digital finishing providers offer die cutting solutions ideal for complex, short-run work. Not only are they designed for smaller volumes, they enable customization and the introduction of new products.
Print providers should consider their current and future cutting needs, evaluate opportunities, and calculate ROI before deciding to invest in an automated die cutter or laser cutting solution. dps
Oct2020, DPS Magazine